JH-3D Prototype
Изготовленная на заказ 3D-печать, силиконовая форма, вакуумное литье, небольшая партия, пластик ABS, PP, нейлон, POM, гибкие силиконовые статуи, детали модели
Изготовленная на заказ 3D-печать, силиконовая форма, вакуумное литье, небольшая партия, пластик ABS, PP, нейлон, POM, гибкие силиконовые статуи, детали модели
Не удалось загрузить сведения о доступности самовывоза
Уведомления
Это ссылка только для того, чтобы показать наши технологии и материалы вакуумного литья в силиконовые формы, пожалуйста, не заказывайте напрямую.
Если у вас есть какие-либо требования к пластиковым деталям мелкими партиями, пожалуйста, свяжитесь с нами.

Вакуумное литье кремниевых форм
Мелкосерийное производство
Мульти материалы:
Стандартный АБС
Термостойкий АБС-пластик
Огнестойкий АБС-пластик
ПП
ПК
ПОМ
Нейлон
Кремниевый Шор 30А
Кремниевый Шор 40А
Кремниевый Шор 50А
Кремниевый Шор 60А
Кремниевый Шор 70А
Кремниевый Шор 80А
Кремниевый Шор 90А


Что такое вакуумное литье в силиконовые формы?
Вакуумное литье в силиконовые формы — это производственный процесс, используемый для создания нескольких копий прототипа или детали с использованием формы из силиконовой резины. Этот процесс часто используется при быстром прототипировании, мелкосерийном производстве и создании сложных деталей или компонентов.

1, мастер-форма для 3D-печати
2. Поместите мастер-форму в рамку, а затем заполните силиконом.
3. Вылечите силиконовую форму и разрежьте ее на 2 части.
4. Налейте смолу в силиконовую форму.
5. Вылечите деталь, а затем извлеките ее из формы.
6. Кастинг завершен.

Как сделать нестандартные детали?
1. Отправьте нам ваше требование
2, ценовое предложение
3. Разместите заказ
4. Начало производства
5. Проверьте качество
6. Доставка и доставка
Материалы: стандартный АБС-пластик.
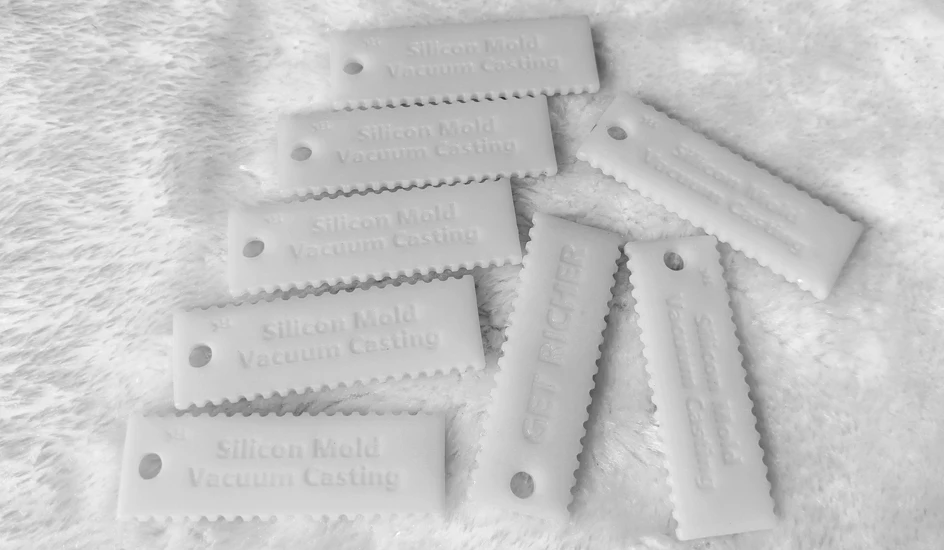
Технология вакуумного литья в силиконовые формы
Материал Стандартный АБС-пластик
Исходный цвет Белый/черный/пользовательский цвет
Термическая деформация 70-100°C
Твердость 83D
Состояние поверхности Небольшие следы инъекций и царапины
Размер печатной платформы 900*650*450 мм
Модуль упругости при изгибе 2000-2200 МПа
Прочность на изгиб 80-100 МПа
Предел прочности 75-85 МПа.
Удлинение при разрыве 8-16 %
Ударная вязкость с надрезом по Изоду 12 КДж/м².
Допуск. Локальная точность продукта составляет 0,3–0,5 мм~5 ‰, тогда как общую точность трудно контролировать.
Постпроцессная сборка, медные гайки от насекомых, физическая полировка, покраска, гальваника, шелкография, водная печать, покрытие
Толщина стенки должна быть выше 0,8 мм, крупные детали согласно 3D-чертежам.
Преимущества стандартного ABS для вакуумного литья в силиконовых формах:
1. Точная репликация: точно воспроизводит свойства и детали деталей из АБС-пластика.
2. Гладкая отделка: в результате получаются детали с полированной поверхностью, напоминающей литье под давлением.
3. Экономическая эффективность: более доступная, чем методы массового производства, такие как литье под давлением.
4. Быстрое производство: быстрый цикл производства для малых и средних тиражей.
5. Универсальность дизайна: позволяет создавать сложные конструкции и подрезы в конечных деталях.
6. Совершенство прототипирования: идеально подходит для прототипирования и функционального тестирования перед массовым производством.
7. Гибкость при небольших объемах: подходит для мелкосерийного производства.
Недостатками стандартного ABS для вакуумного литья в силиконовых формах являются:
1. Ограниченные свойства материала: Свойства готовых деталей из АБС-пластика могут не полностью соответствовать свойствам высококачественного АБС-пластика, отлитого под давлением.
2. Не идеален для больших объемов производства: лучше всего подходит для низких и средних объемов производства; может оказаться нерентабельным для крупномасштабного производства.
3. Износ пресс-форм. Силиконовые формы, используемые в этом процессе, могут со временем разрушаться, что влияет на качество и долговечность отливок.
4. Время выполнения: включает время создания и отверждения пресс-формы, что может повлиять на сроки проекта.
Термостойкий АБС-пластик
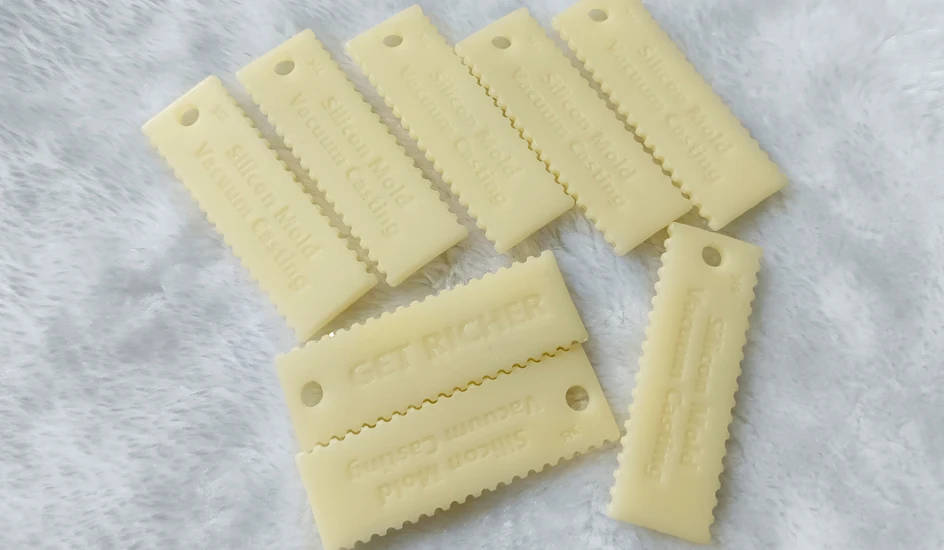
Технология вакуумного литья в силиконовые формы
Материал: термостойкий АБС-пластик.
Исходный цвет Белый/черный/пользовательский цвет
Термическая деформация 100-150°С
Твердость 80D
Состояние поверхности Небольшие следы инъекций и царапины
Размер печатной платформы 900*650*450 мм
Модуль упругости при изгибе 2000-2200 МПа
Прочность на изгиб 90-115 МПа
Предел прочности 55-60 МПа.
Удлинение при разрыве 8-16 %
Ударная вязкость с надрезом по Изоду 35 КДж/м²
Допуск. Локальная точность продукта составляет 0,3–0,5 мм~5 ‰, тогда как общую точность трудно контролировать.
Постпроцессная сборка, медные гайки от насекомых, физическая полировка, покраска, гальваника, шелкография, водная печать, покрытие
Толщина стенки должна быть выше 0,8 мм, крупные детали согласно 3D-чертежам.
Преимущества термостойкого АБС-пластика для вакуумного литья в силиконовых формах:
1. Повышенная термостойкость: термостойкий АБС-пластик может выдерживать более высокие температуры по сравнению со стандартным АБС-пластиком, что расширяет возможности его применения в средах, подвергающихся воздействию тепла.
2. Долговечность и прочность: детали, изготовленные из термостойкого АБС-пластика, сохраняют свою структурную целостность и свойства даже при повышенных температурах, обеспечивая долговечность.
3. Широкий диапазон применения: идеально подходит для деталей, необходимых в различных отраслях промышленности, таких как автомобильная, аэрокосмическая и электронная, где часто наблюдается воздействие тепла.
4. Хорошая химическая стойкость: термостойкий АБС-пластик обычно обладает хорошей устойчивостью к химическим веществам, что повышает его пригодность для различных промышленных сред.
Недостатками термостойкого АБС-пластика для вакуумного литья в силиконовых формах являются:
1. Ограниченная термостойкость: хотя термостойкий АБС-пластик может выдерживать более высокие температуры, чем стандартный АБС-пластик, он все же имеет температурные ограничения и может деформироваться или терять свойства при очень высоких температурах.
2. Стоимость материала: термостойкий АБС-пластик может быть дороже стандартного АБС-пластика, что увеличивает общую стоимость процесса вакуумного литья.
3. Сложный процесс формования. Для достижения термостойкости АБС-пластика может потребоваться более сложный процесс формования, что усложняет и требует больше времени для создания силиконовой формы.
4. Износ формы. Более высокие температуры могут ускорить износ силиконовой формы, сокращая ее срок службы и влияя на качество отливок.
Огнестойкий АБС-пластик
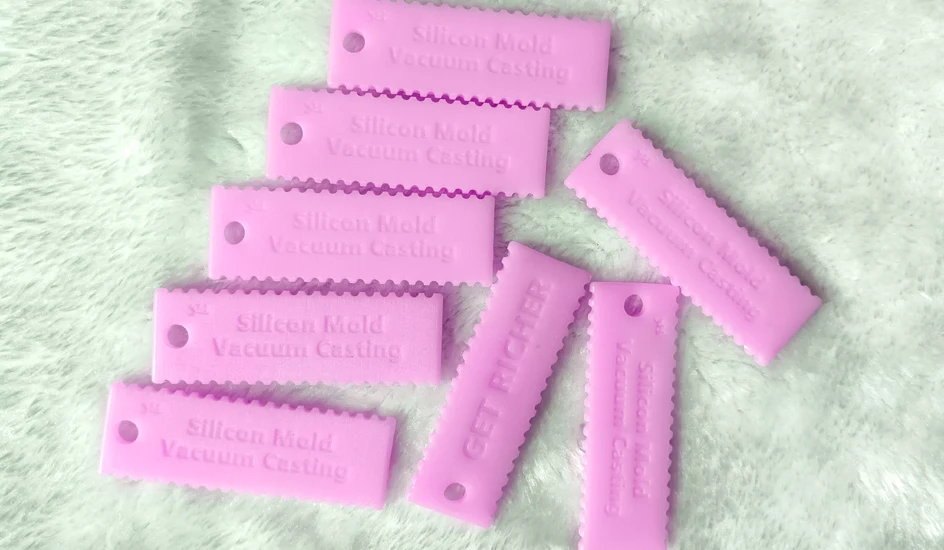
Технология вакуумного литья в силиконовые формы
Материал: огнестойкий АБС-пластик.
Исходный цвет Белый/черный/пользовательский цвет
Термическая деформация 70-80°C
Твердость 82D
Состояние поверхности Небольшие следы инъекций и царапины
Размер печатной платформы 900*650*450 мм
Модуль упругости при изгибе 2100-2300 МПа.
Прочность на изгиб 80-90 МПа
Предел прочности 60-70 МПа.
Удлинение при разрыве 8-10 %
Ударная вязкость с надрезом по Изоду 15 КДж/м².
Допуск. Локальная точность продукта составляет 0,3–0,5 мм~5 ‰, тогда как общую точность трудно контролировать.
Постпроцессная сборка, медные гайки от насекомых, физическая полировка, покраска, гальваника, шелкография, водная печать, покрытие
Толщина стенки должна быть выше 0,8 мм, крупные детали согласно 3D-чертежам.
Преимущества огнестойкого АБС-пластика для вакуумного литья в силиконовых формах:
1. Повышенная безопасность: огнестойкий АБС-пластик обеспечивает повышенную пожаробезопасность, препятствуя воспламенению и замедляя распространение огня.
2. Соответствие нормативным требованиям: идеально подходит для применений, где соблюдение стандартов пожарной безопасности и нормативных требований имеет важное значение, например, в автомобильной и электронной промышленности.
3. Долговечность и функциональность: сохраняет долговечность и функциональность АБС-пластика, одновременно обладая огнестойкими свойствами, что делает его пригодным для широкого спектра применений.
4.Широкое применение: Полезно в средах, где пожарная безопасность является проблемой, включая электрические корпуса, салоны автомобилей и бытовую электронику.
Недостатками огнестойкого АБС-пластика для вакуумного литья в силиконовых формах являются:
1. Сложность материала: огнестойкий АБС-пластик является более сложным материалом, что потенциально усложняет процесс литья.
2. Стоимость: огнестойкий АБС-пластик может быть дороже стандартного АБС-пластика, что увеличивает общую стоимость проекта.
3. Ограниченные варианты материалов. Выбор огнестойких материалов может быть ограничен по сравнению со стандартным АБС-пластиком, что ограничивает выбор материалов для данного процесса.
ПК

Технология вакуумного литья в силиконовые формы
Материал ПК
Исходный цвет Белый/черный/полупрозрачный/пользовательский цвет
Термическая деформация 50-60°C
Твердость 80D
Состояние поверхности Небольшие следы инъекций и царапины
Размер печатной платформы 900*650*450 мм
Модуль упругости при изгибе 1700-1800 МПа.
Прочность на изгиб 80-90 МПа
Модуль упругости 1900-2000 МПа.
Предел прочности 35-40 МПа.
Удлинение при разрыве 5-6 %
Ударная вязкость с надрезом по Изоду 18 КДж/м²
Допуск. Локальная точность продукта составляет 0,3–0,5 мм~5 ‰, тогда как общую точность трудно контролировать.
Постпроцессная сборка, медные гайки от насекомых, физическая полировка, покраска, гальваника, шелкография, водная печать, покрытие
Толщина стенки должна быть выше 0,8 мм, крупные детали согласно 3D-чертежам.
Преимущества ПК для вакуумного литья в силиконовые формы:
1. Высокая ударопрочность: ПК является одним из наиболее ударопрочных термопластов, что делает его пригодным для применений, где детали должны выдерживать механические нагрузки и потенциальные удары.
2.Оптическая прозрачность: ПК обеспечивает превосходную оптическую четкость и прозрачность, что делает его идеальным для деталей, требующих прозрачности или светопроницаемости, таких как линзы, крышки и защитные экраны.
3. Стабильность размеров: детали, изготовленные с помощью ПК, сохраняют свою форму и размеры даже при колебаниях температуры, обеспечивая стабильную производительность.
4. Химическая стойкость: ПК обладает хорошей устойчивостью ко многим химическим веществам, что делает его пригодным для применений, где воздействие различных веществ является проблемой.
5.Малообъемное производство. Вакуумное литье в силиконовые формы хорошо подходит для производства малых и средних партий деталей ПК, особенно когда традиционные методы производства являются непомерно дорогостоящими для небольших объемов производства.
Недостатками ПК для вакуумного литья в силиконовые формы являются:
1. Время выполнения заказа. Производственный процесс, включая создание пресс-форм, отверждение и литье, может занять несколько дней. Это может не подойти для проектов с очень сжатыми сроками.
2. Износ пресс-формы. Силиконовые формы имеют ограниченный срок службы и могут со временем изнашиваться, особенно при использовании смол с высокими механическими свойствами, таких как ПК. При больших объемах производства может потребоваться частая замена пресс-формы.
3. Требуется постобработка: Детали из литого ПК могут потребовать последующей обработки, такой как обрезка, шлифование или полировка, для достижения желаемой чистоты поверхности и точности размеров.
4. Усадка материала: ПК-смола может испытывать некоторую усадку в процессе отверждения, что может потребовать корректировки конструкции формы для компенсации изменений размеров.
5. Ограниченная переработка материалов: Избыток или отходы материала, образующиеся во время вакуумного литья силиконовых форм с помощью ПК, обычно не подлежат вторичной переработке для использования в будущем.
6. Стоимость. Хотя этот процесс может быть экономически эффективным при мелкосерийном производстве деталей ПК, он может иметь более высокие затраты на единицу продукции по сравнению с традиционными методами производства, такими как литье под давлением, для более крупных производственных циклов.
ПП
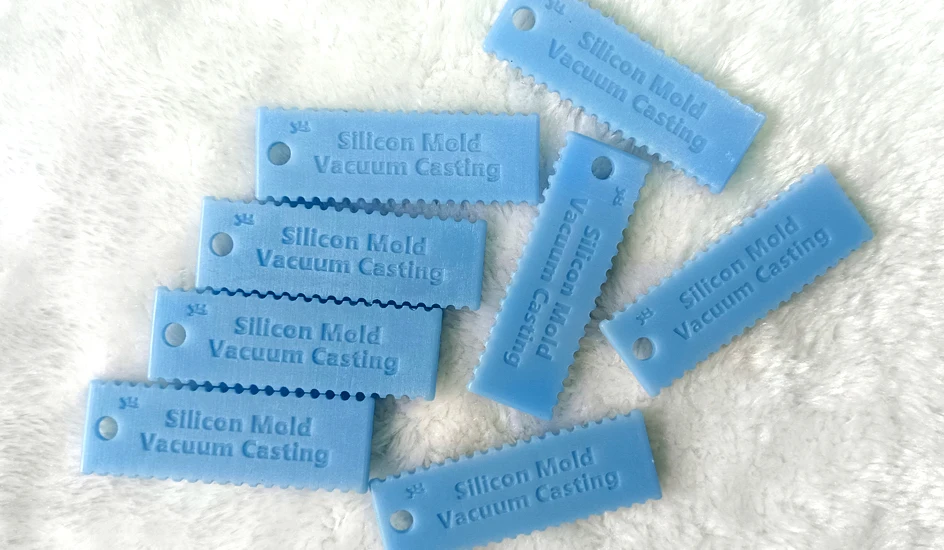
Технология вакуумного литья в силиконовые формы
Материал ПП
Исходный цвет Белый/черный/пользовательский цвет
Термическая деформация 50-60°C
Твердость 75-83D
Состояние поверхности Небольшие следы инъекций и царапины
Размер печатной платформы 900*650*450 мм
Модуль упругости при изгибе 600-1300 МПа
Прочность на изгиб 20-50 МПа
Предел прочности 25-35 МПа.
Удлинение при разрыве 5-6 %
Ударная вязкость с надрезом по Изоду 18 КДж/м²
Допуск. Локальная точность продукта составляет 0,3–0,5 мм~5 ‰, тогда как общую точность трудно контролировать.
Постпроцессная сборка, медные гайки от насекомых, физическая полировка, покраска, гальваника, шелкография, водная печать, покрытие
Толщина стенки должна быть выше 0,8 мм, крупные детали согласно 3D-чертежам.
Преимущества полипропилена для вакуумного литья в силиконовые формы:
1. Химическая стойкость: ПП обладает высокой устойчивостью ко многим химикатам, кислотам и основаниям, что делает его пригодным для применений, в которых детали подвергаются воздействию агрессивных веществ.
2. Низкая плотность: ПП имеет низкую плотность, что означает его легкий вес. Это выгодно для применений, где важно снижение веса, например, для автомобильных компонентов.
3. Хорошая электроизоляция: ПП является хорошим электроизолятором, что делает его пригодным для электрических и электронных устройств.
4. Гибкость и прочность: ПП имеет хороший баланс гибкости и прочности, что делает его устойчивым к ударам и усталости. Он выдерживает изгиб и многократное использование.
5. Низкое поглощение влаги: ПП обладает низкими влагопоглощающими свойствами, что является преимуществом в тех случаях, когда воздействие влаги или влажности является проблемой.
6.Малообъемное производство. Вакуумное литье в силиконовые формы хорошо подходит для производства малых и средних партий полипропиленовых деталей, особенно когда традиционные методы производства являются слишком дорогостоящими для небольших объемов производства.
Недостатками вакуумного литья ПП-полипропилена в силиконовые формы являются:
1. Время выполнения заказа. Производственный процесс, включая создание пресс-форм, отверждение и литье, может занять несколько дней. Это может не подойти для проектов с очень сжатыми сроками.
2. Износ пресс-формы. Силиконовые формы имеют ограниченный срок службы и могут со временем изнашиваться, особенно при использовании со смолами со специальными добавками или армирующими добавками, такими как ПП. При больших объемах производства может потребоваться частая замена пресс-формы.
3. Требуется постобработка: Детали из литого полипропилена могут потребовать последующей обработки, такой как обрезка, шлифовка или чистовая обработка поверхности, для достижения желаемого внешнего вида и точности размеров.
4. Усадка материала: ПП-смола может испытывать некоторую усадку в процессе отверждения, что может потребовать корректировки конструкции формы для компенсации изменений размеров.
5. Ограниченная переработка материалов: Излишки или отходы, образующиеся при вакуумном литье в силиконовые формы с полипропиленом, обычно не подлежат вторичной переработке для использования в будущем.
6. Ограниченная термостойкость: ПП имеет относительно низкую температуру теплового искажения, что означает, что он может деформироваться или терять структурную целостность при повышенных температурах. Он не подходит для применения при высоких температурах.
Таким образом, вакуумное литье в силиконовые формы с полипропиленом обеспечивает такие преимущества, как химическая стойкость, низкая плотность и гибкость. Однако у него есть ограничения, такие как время выполнения заказа, износ пресс-формы и необходимость последующей обработки. При выборе этого метода для проектов 3D-печати с использованием полипропилена необходимо тщательное рассмотрение требований проекта и материалов.
Нейлон
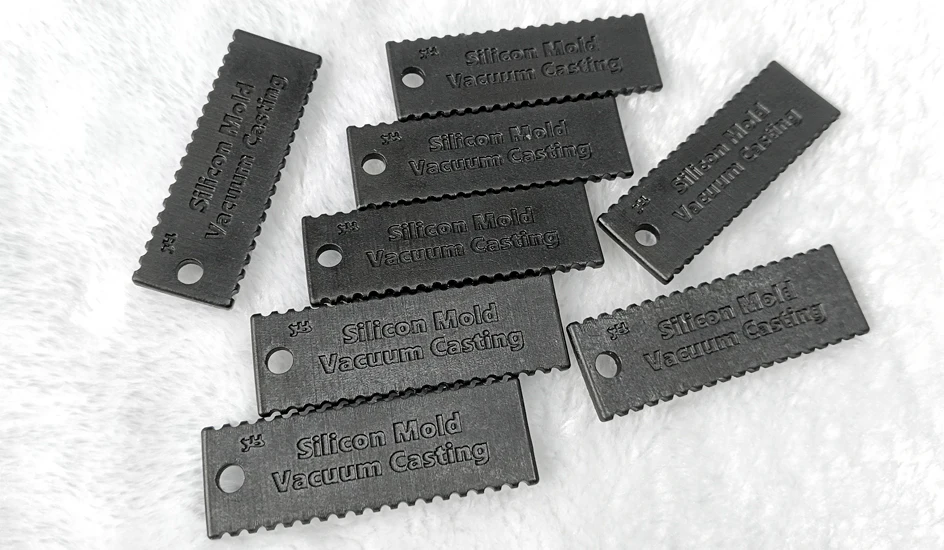
Технология вакуумного литья в силиконовые формы
Материал Нейлон
Исходный цвет Белый/черный/пользовательский цвет
Термическая деформация 100-120°C
Твердость 87D
Состояние поверхности Небольшие следы инъекций и царапины
Размер печатной платформы 900*650*450 мм
Модуль упругости при изгибе 1800-2000 МПа.
Прочность на изгиб 80-92 МПа
Предел прочности 50-60 МПа.
Удлинение при разрыве 10-12 %
Ударная вязкость с надрезом по Изоду 17 КДж/м²
Допуск. Локальная точность продукта составляет 0,3–0,5 мм~5 ‰, тогда как общую точность трудно контролировать.
Постпроцессная сборка, медные гайки от насекомых, физическая полировка, покраска, гальваника, шелкография, водная печать, покрытие
Толщина стенки должна быть выше 0,8 мм, крупные детали согласно 3D-чертежам.
Преимущества нейлона для вакуумного литья в силиконовые формы:
1. Высокая механическая прочность. Нейлоновые детали, изготовленные с помощью этого процесса, обладают превосходными механическими свойствами, включая высокую прочность на разрыв, ударную вязкость и ударопрочность. Это делает нейлон подходящим для требовательных применений.
2. Долговечность: Нейлон известен своей долговечностью и устойчивостью к износу, что делает его идеальным для компонентов, которые должны противостоять трению и истиранию.
3. Химическая стойкость: Нейлон обладает хорошей устойчивостью ко многим химикатам, маслам и растворителям, что делает его пригодным для применений, где воздействие различных веществ является проблемой.
4. Низкий коэффициент трения: нейлон имеет низкий коэффициент трения, что делает его идеальным для применений, связанных с движущимися частями или скользящими механизмами.
5. Гибкость: Нейлоновые детали могут проявлять определенную степень гибкости, в зависимости от конкретного типа используемого нейлона. Это делает его подходящим для применений, требующих баланса жесткости и гибкости.
6.Малообъемное производство. Вакуумное литье в силиконовые формы хорошо подходит для производства небольших и средних объемов нейлоновых деталей, особенно когда традиционные методы производства являются непомерно дорогостоящими для небольших объемов производства.
Недостатками вакуумного литья в силиконовые формы из стекловолокна и нейлона являются:
1. Время выполнения заказа. Производственный процесс, включая создание пресс-форм, отверждение и литье, может занять несколько дней. Это может не подойти для проектов с очень сжатыми сроками.
2. Износ пресс-формы. Силиконовые формы имеют ограниченный срок службы и могут со временем изнашиваться, особенно при использовании смол с высокими механическими свойствами, таких как нейлон. При больших объемах производства может потребоваться частая замена пресс-формы.
3. Требуется постобработка: детали из литого нейлона могут потребовать последующей обработки, такой как обрезка, шлифовка или чистовая обработка поверхности, для достижения желаемого внешнего вида и точности размеров.
4. Усадка материала. Нейлоновая смола может испытывать некоторую усадку в процессе отверждения, что может потребовать корректировки конструкции формы для компенсации изменений размеров.
5. Ограниченная переработка материалов: Излишки или отходы, образующиеся во время вакуумного литья в силиконовые формы с нейлоном, обычно не подлежат вторичной переработке для использования в будущем.
6.Гигроскопичность: Нейлон гигроскопичен, то есть со временем он может впитывать влагу из окружающей среды. Это может повлиять на его механические свойства при неправильном обращении и хранении.
ПОМ
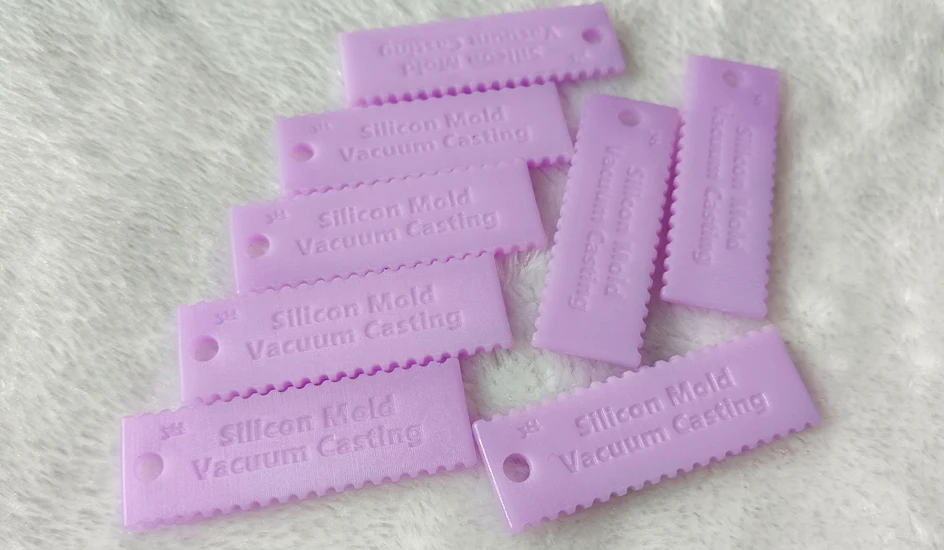
Технология вакуумного литья в силиконовые формы
Материал ПОМ
Исходный цвет Белый/черный/пользовательский цвет
Термическая деформация 70-80°C
Твердость 80D
Состояние поверхности Небольшие следы инъекций и царапины
Размер печатной платформы 900*650*450 мм
Модуль упругости при изгибе 2400-2500 МПа.
Прочность на изгиб 100-110 МПа
Предел прочности 60-70 МПа.
Удлинение при разрыве 10-12 %
Ударная вязкость с надрезом по Изоду 17 КДж/м²
Допуск. Локальная точность продукта составляет 0,3–0,5 мм~5 ‰, тогда как общую точность трудно контролировать.
Постпроцессная сборка, медные гайки от насекомых, физическая полировка, покраска, гальваника, шелкография, водная печать, покрытие
Толщина стенки должна быть выше 0,8 мм, крупные детали согласно 3D-чертежам.
Преимущества ПОМ для вакуумного литья в силиконовые формы:
1. Отличные механические свойства: ПОМ демонстрирует выдающиеся механические свойства, включая высокую прочность на разрыв, жесткость и ударопрочность. Он часто используется в приложениях, требующих надежных и долговечных компонентов.
2. Низкое трение: ПОМ имеет низкий коэффициент трения, что делает его идеальным для деталей, выполняющих скользящие или вращательные движения. Он обычно используется в шестернях, подшипниках и других компонентах, где снижение трения имеет решающее значение.
3. Стабильность размеров: ПОМ обладает превосходной стабильностью размеров, что означает, что детали, изготовленные из этого материала, сохраняют свою форму и размер даже при колебаниях температуры и механических нагрузках.
4. Химическая стойкость: ПОМ устойчив ко многим химическим веществам, включая растворители, масла и топливо, что делает его пригодным для применений, где воздействие различных веществ является проблемой.
5. Низкое поглощение влаги: ПОМ обладает низкими свойствами поглощения влаги, что является преимуществом в тех случаях, когда воздействие влаги или влажности может повлиять на производительность.
6.Малообъемное производство. Вакуумное литье в силиконовые формы хорошо подходит для производства небольших и средних партий деталей из ПОМ, особенно когда традиционные методы производства являются непомерно дорогостоящими для небольших объемов производства.
Недостатками ПОМ для вакуумного литья в силиконовые формы являются:
1. Время выполнения заказа. Производственный процесс, включая создание пресс-форм, отверждение и литье, может занять несколько дней. Это может не подойти для проектов с очень сжатыми сроками.
2. Износ пресс-формы. Силиконовые формы имеют ограниченный срок службы и могут со временем изнашиваться, особенно при использовании смол с высокими механическими свойствами, таких как ПОМ. При больших объемах производства может потребоваться частая замена пресс-формы.
3.Требуется постобработка: для достижения желаемого внешнего вида и точности размеров литым деталям из ПОМ может потребоваться постобработка, такая как обрезка, шлифовка или чистовая обработка поверхности.
4. Усадка материала: смола ПОМ может испытывать некоторую усадку в процессе отверждения, что может потребовать корректировки конструкции формы для компенсации изменений размеров.
5. Ограниченная переработка материала: Избыток или отходы материала, образующиеся во время вакуумного литья в силиконовые формы с использованием ПОМ, обычно не подлежат вторичной переработке для использования в будущем.
6. Стоимость: хотя этот процесс может быть экономически эффективным при мелкосерийном производстве деталей из ПОМ, он может иметь более высокие затраты на единицу продукции по сравнению с традиционными методами производства, такими как литье под давлением, для более крупных производственных циклов.
Таким образом, вакуумное литье в силиконовые формы с ПОМ предлагает преимущества превосходных механических свойств, низкого трения и химической стойкости. Однако у него есть ограничения, такие как время выполнения заказа, износ пресс-формы и необходимость последующей обработки. При выборе этого метода для проектов 3D-печати с использованием POM необходимо тщательное рассмотрение требований проекта и материалов.
Кремний


Технология вакуумного литья в силиконовые формы
Материал Кремний
Исходный цвет Белый/черный/пользовательский цвет
Термическая деформация 50-70°C
Состояние поверхности Небольшие следы инъекций и царапины
Размер печатной платформы 900*650*450 мм
Допуск. Локальная точность продукта составляет 0,3–0,5 мм~5 ‰, тогда как общую точность трудно контролировать.
Твердость: 30А, 40А, 50А, 60А, 70А, 80А, 90А по Шору.
Толщина стенки должна быть выше 0,8 мм, крупные детали согласно 3D-чертежам.
Преимущества кремния:
1. Эластомерные свойства: Силиконовый каучук обладает превосходными эластомерными свойствами, включая гибкость и упругость. Он идеально подходит для изготовления деталей, которые должны быть мягкими, податливыми и способными вернуться к исходной форме после деформации.
2. Химическая стойкость: силикон устойчив ко многим химикатам, маслам и растворителям, что делает его пригодным для применений, где воздействие различных веществ является проблемой.
3.Малообъемное производство. Вакуумное литье в силиконовые формы хорошо подходит для производства небольших и средних объемов гибких силиконовых деталей, особенно когда традиционные методы производства являются непомерно дорогостоящими для небольших объемов производства.
4. Настройка: силиконовые материалы можно тонировать, пигментировать или смешивать для достижения различных цветов или удовлетворения конкретных эстетических требований.
Недостатками кремния являются:
1. Время выполнения заказа. Производственный процесс, включая создание пресс-форм, отверждение и литье, может занять несколько дней. Это может не подойти для проектов с очень сжатыми сроками.
2. Износ пресс-формы. Силиконовые формы имеют ограниченный срок службы и могут со временем изнашиваться, особенно при использовании смол со специальными добавками или армирующими добавками. При больших объемах производства может потребоваться частая замена пресс-формы.
3. Требуется постобработка: литые силиконовые детали могут потребовать последующей обработки, такой как обрезка, шлифовка или чистовая обработка поверхности, для достижения желаемого внешнего вида и точности размеров.
4. Усадка материала: Силиконовая смола может испытывать некоторую усадку в процессе отверждения, что может потребовать корректировки конструкции формы для компенсации изменений размеров.
5. Стоимость: Хотя этот процесс может быть экономически эффективным при мелкосерийном производстве гибких силиконовых деталей, он может иметь более высокие затраты на единицу продукции по сравнению с традиционными методами производства, такими как литье под давлением, для более крупных производственных циклов.
Для аэрокосмической, автомобильной и мотоциклетной промышленности

Для фигуристов, мода, носимые предметы
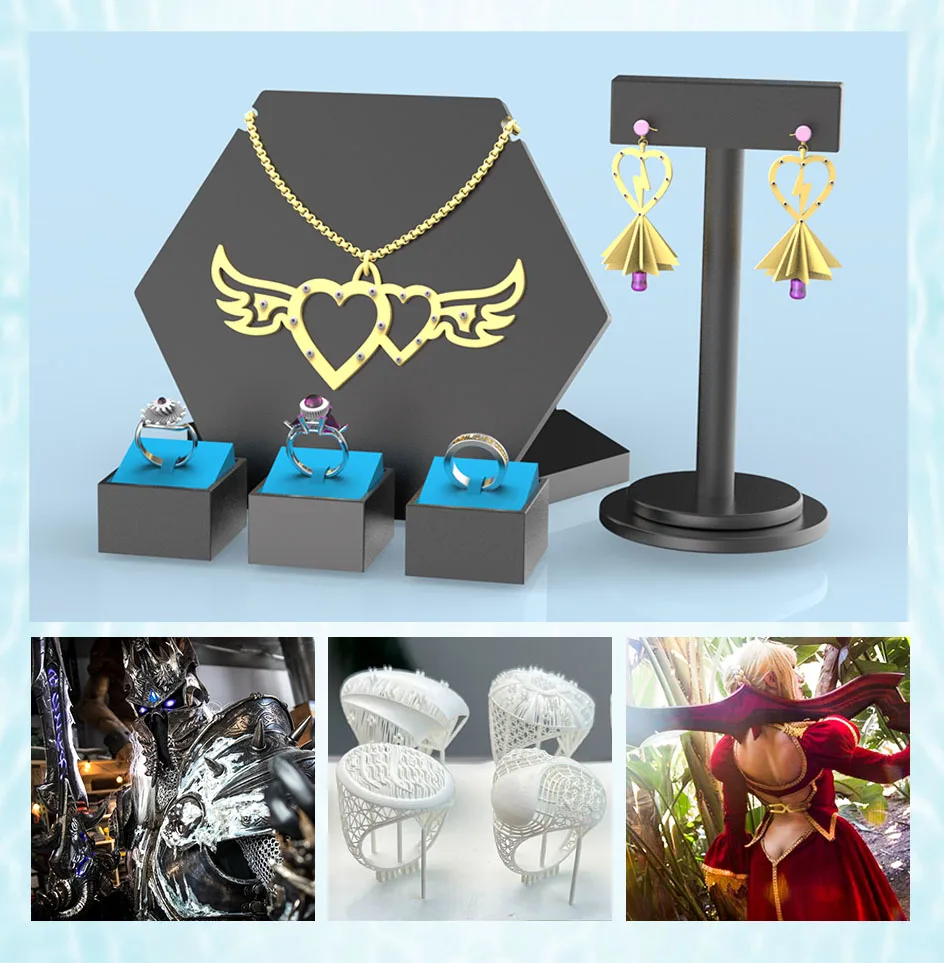
Для фигуристов, мода, носимые предметы
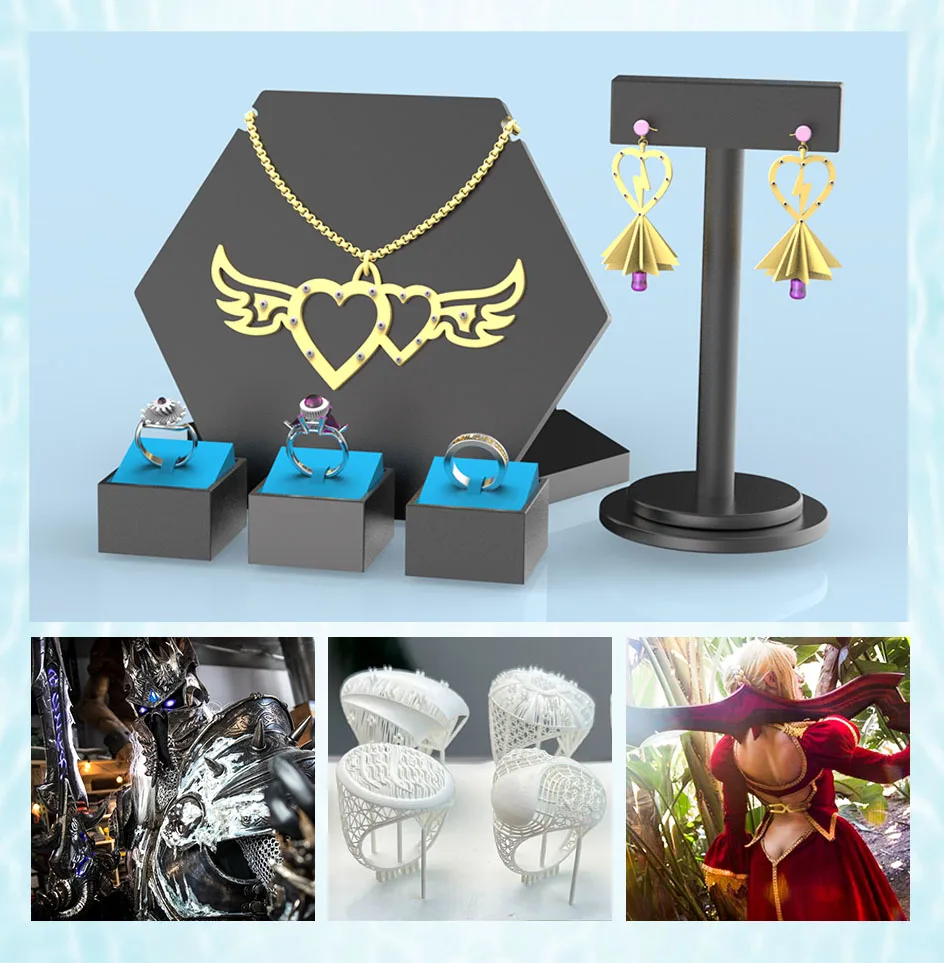
Часто задаваемые вопросы по индивидуальной 3D-печати
Вопрос: Могу ли я напечатать нестандартные или персонализированные объекты с помощью 3D-принтера?
О: Да, 3D-печать отлично подходит для создания индивидуальных или персонализированных объектов: от прототипов до уникальных подарков.
Вопрос: Какой формат файла необходим для 3D-печати?
О: Наиболее распространенным форматом файлов является STL, но службы могут принимать и другие форматы, например: STP, obj.
Вопрос: Как я могу отправить вам файлы?
О: вы можете отправить нам свои требования через чат Aliexpress или по электронной почте на адрес jh-aliexpress@hotmail dot com.
Вопрос: Какие технологии вы предоставляете?
О: Мы предоставляем мультитехнологии: технологии SLA, SLS, SLM, MJF и DLP, вакуумное литье кремниевых форм и обработку на станках с ЧПУ, услуги лазерной резки.
В: Какие материалы вы можете предоставить?
О: Мы поставляем различные материалы: смолу, нейлон, нейлон + стекловолокно, красный воск, алюминий, нержавеющую сталь, титановый сплав, латунь, АБС, ПП, ПК, ПОМ, акрил, ПВХ...
Вопрос: Сколько времени занимает 3D-печать объекта?
О: Время печати зависит от размера, сложности и выбранной скорости печати. Небольшие объекты могут занять несколько часов, а большие и сложные — несколько дней.
Вопрос: Требуется ли постобработка деталей, напечатанных на 3D-принтере?
О: Это зависит от желаемой отделки. В некоторых случаях может потребоваться последующая обработка, такая как шлифовка, покраска или сборка.
Вопрос: Существуют ли ограничения по размеру услуг 3D-печати?
О: Да, каждый 3D-принтер имеет определенный объем печати, поэтому могут быть ограничения на размер объектов, которые можно напечатать.
Вопрос: Есть ли какие-либо соображения по поводу дизайна 3D-печати?
Ответ: Да, при проектировании для 3D-печати необходимо учитывать такие факторы, как опорные конструкции, ориентация слоев и толщина стенок, чтобы обеспечить успешную печать.
Вопрос: В каких отраслях используются услуги 3D-печати?
Ответ: 3D-печать используется в широком спектре отраслей, включая аэрокосмическую, здравоохранение, автомобилестроение, архитектуру и производство потребительских товаров.

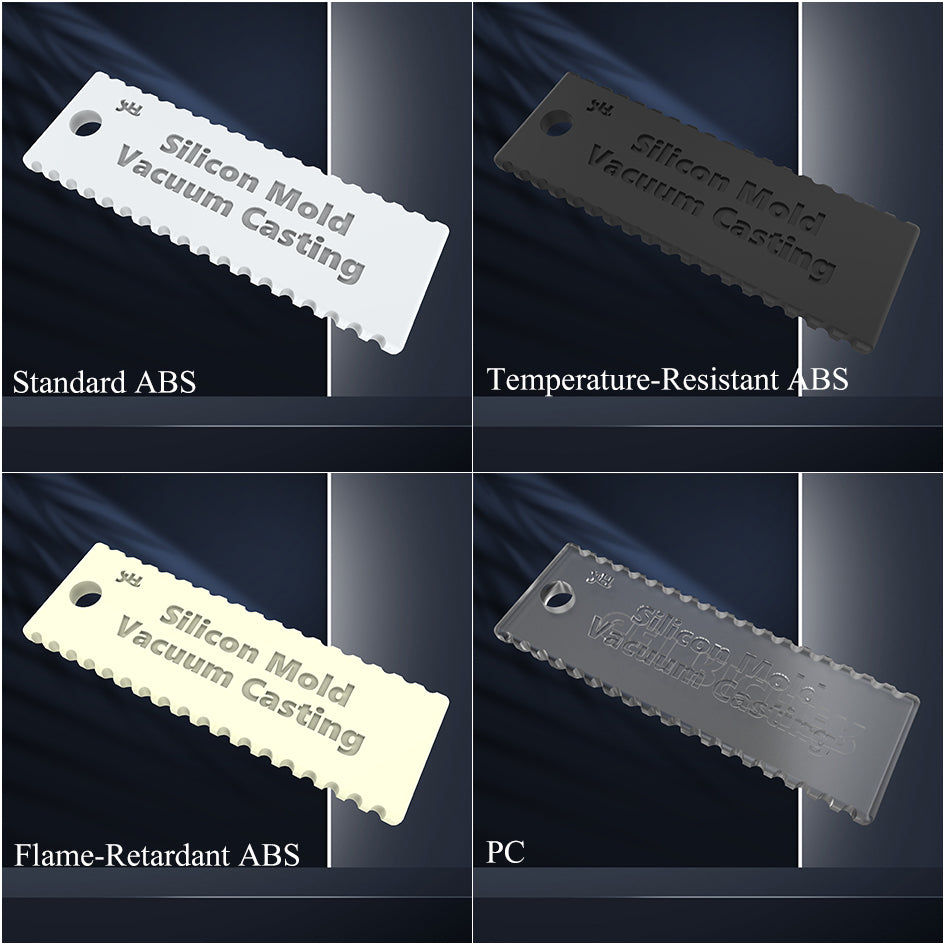
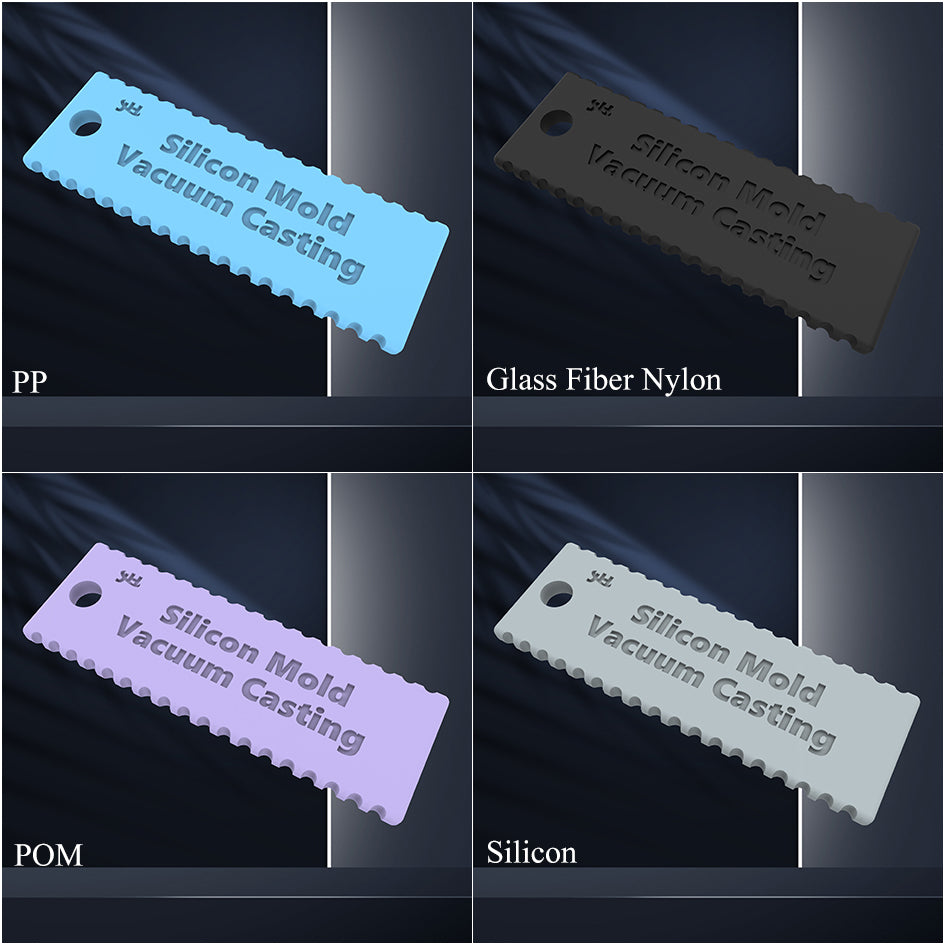
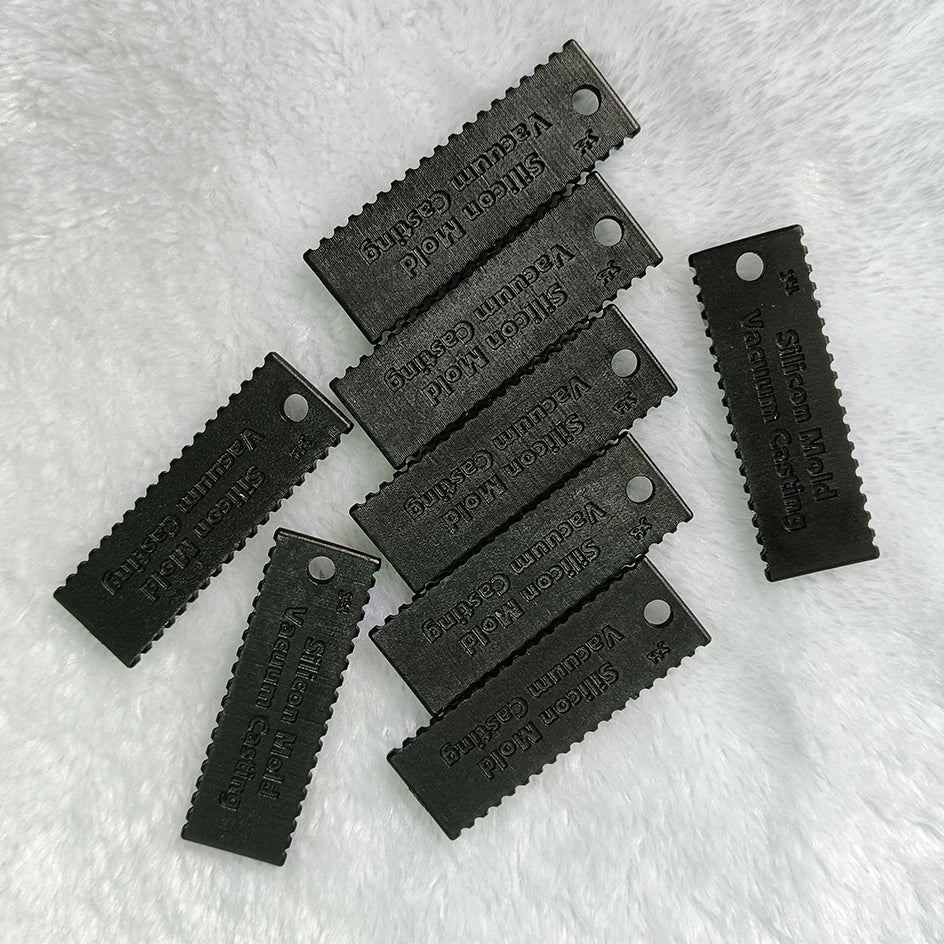
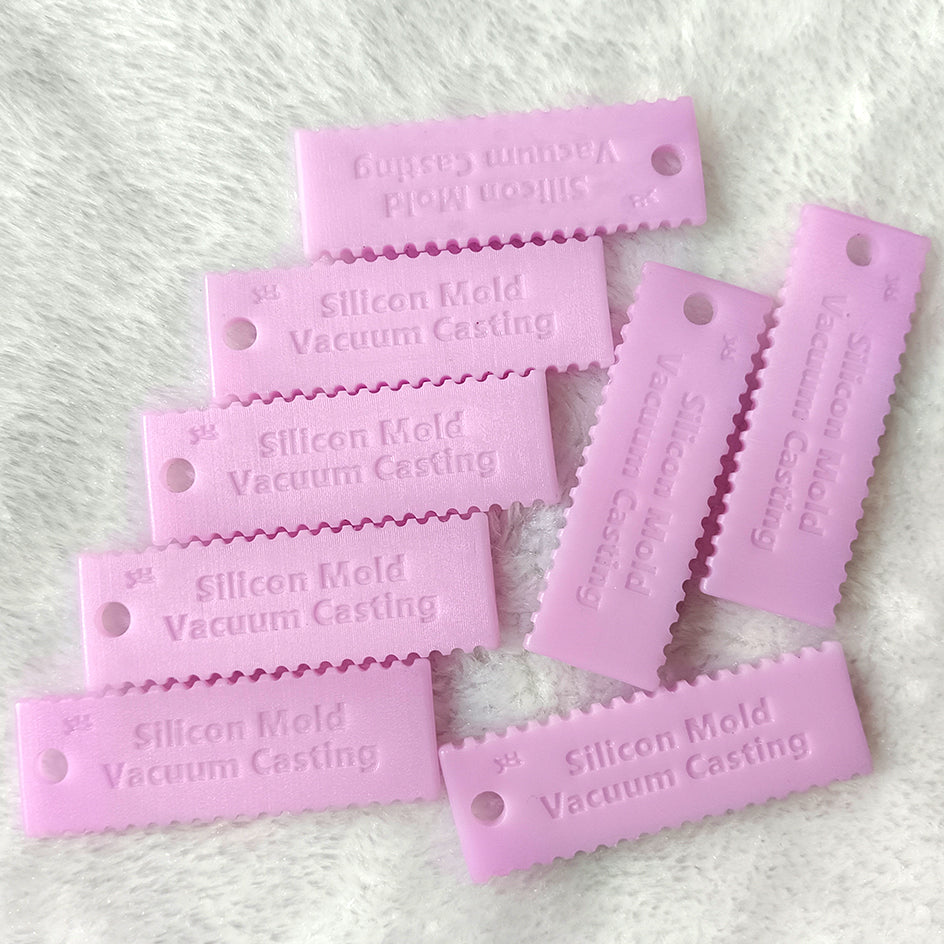
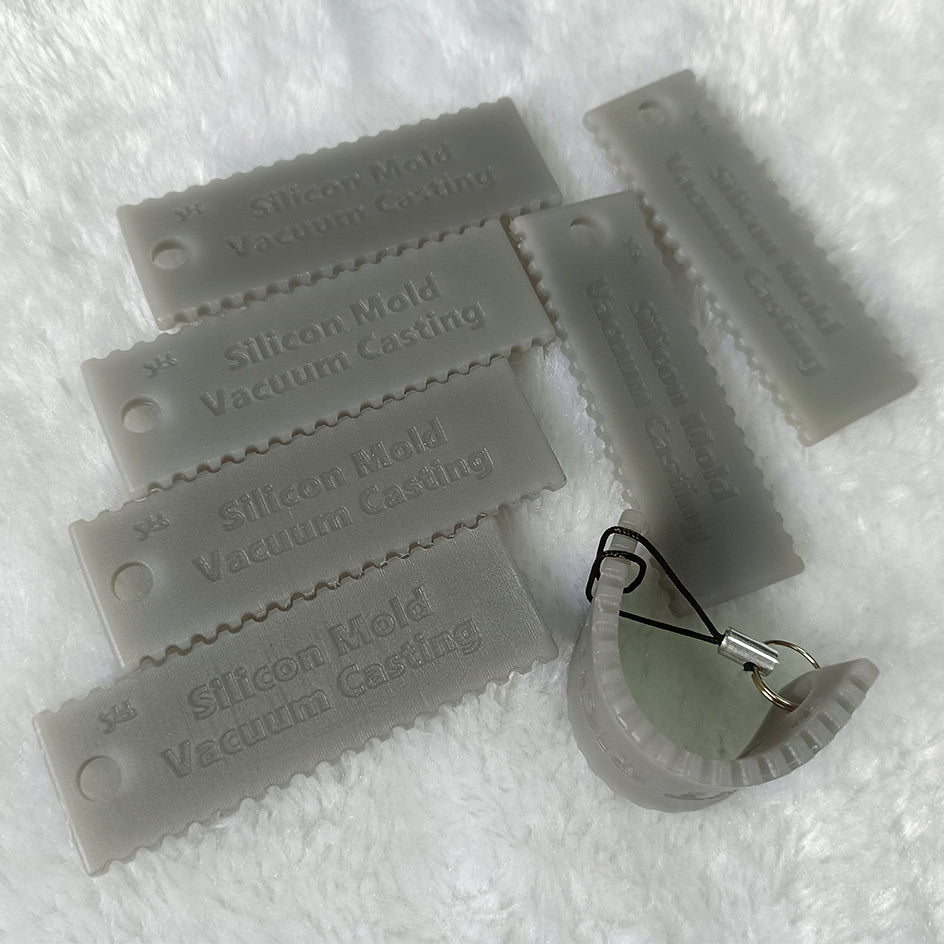