JH-3D
Custom 3D Printing Service Precision Print Prototype SLA Resin SLS TPU MJF Nylon SLM Metal Aluminum Stainless Titanium ABS Model
Custom 3D Printing Service Precision Print Prototype SLA Resin SLS TPU MJF Nylon SLM Metal Aluminum Stainless Titanium ABS Model
Couldn't load pickup availability
Note
This is a link just to show our 3D printing technologies and materials, please do not order directly.
If you have any requirements for 3D printing, please kindly contact us by Aliexpress or Email.
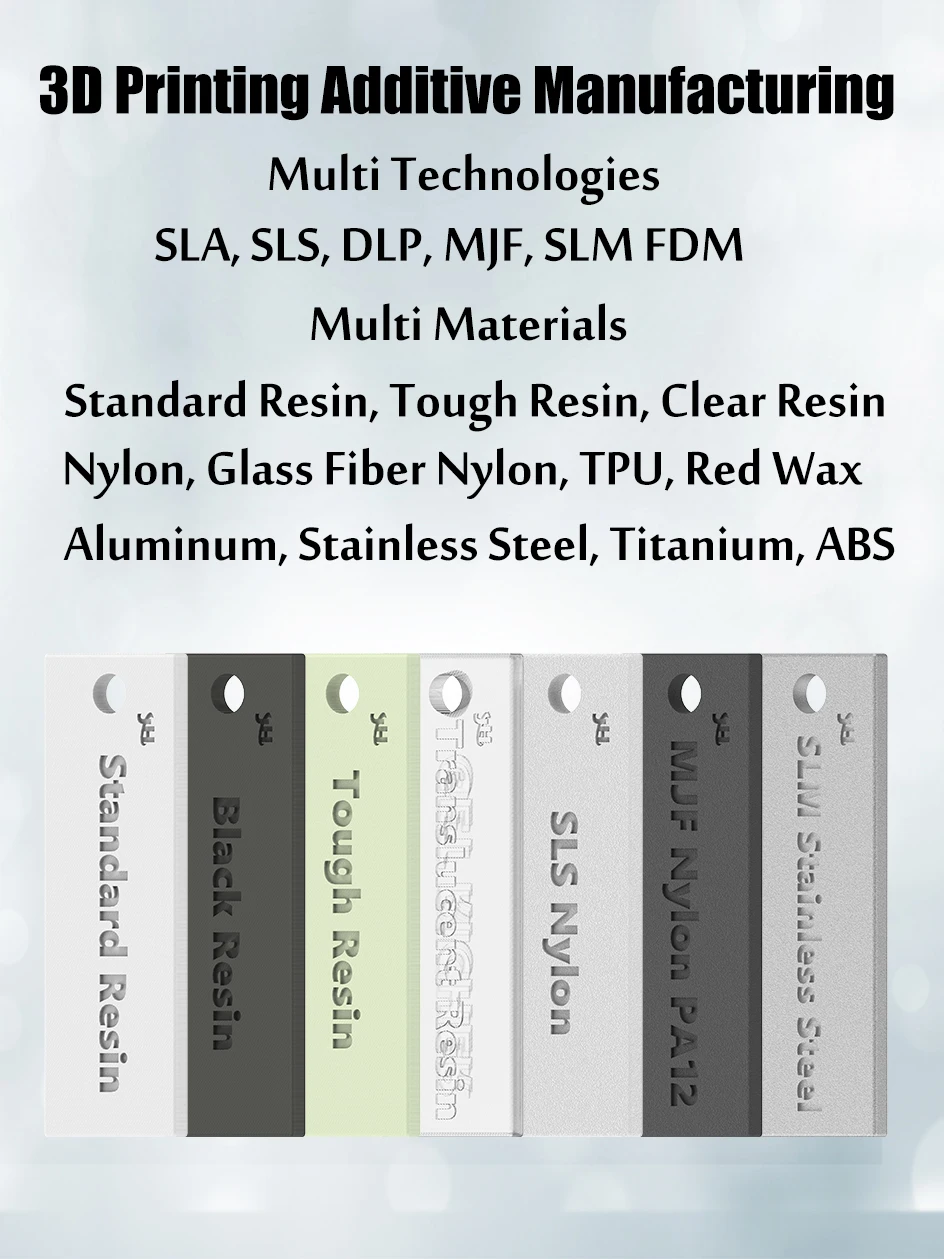
Customize 3D Print Services
Multi-Technologies
Multi-Materials
SLA Standard White Resin
SLA Standard Black Resin
SLA Tough Resin
SLA High-Temperature Resin
SLA Translucent Resin
SLA Clear Resin
SLS Nylon
SLS Glass Filber Nylon
SLS TPU
MJF Nylon PA12 (Gray/Black)
DLP Red Wax
SLM Aluminum
SLM Stainless Steel
SLM Titanium Alloy
FDM ABS
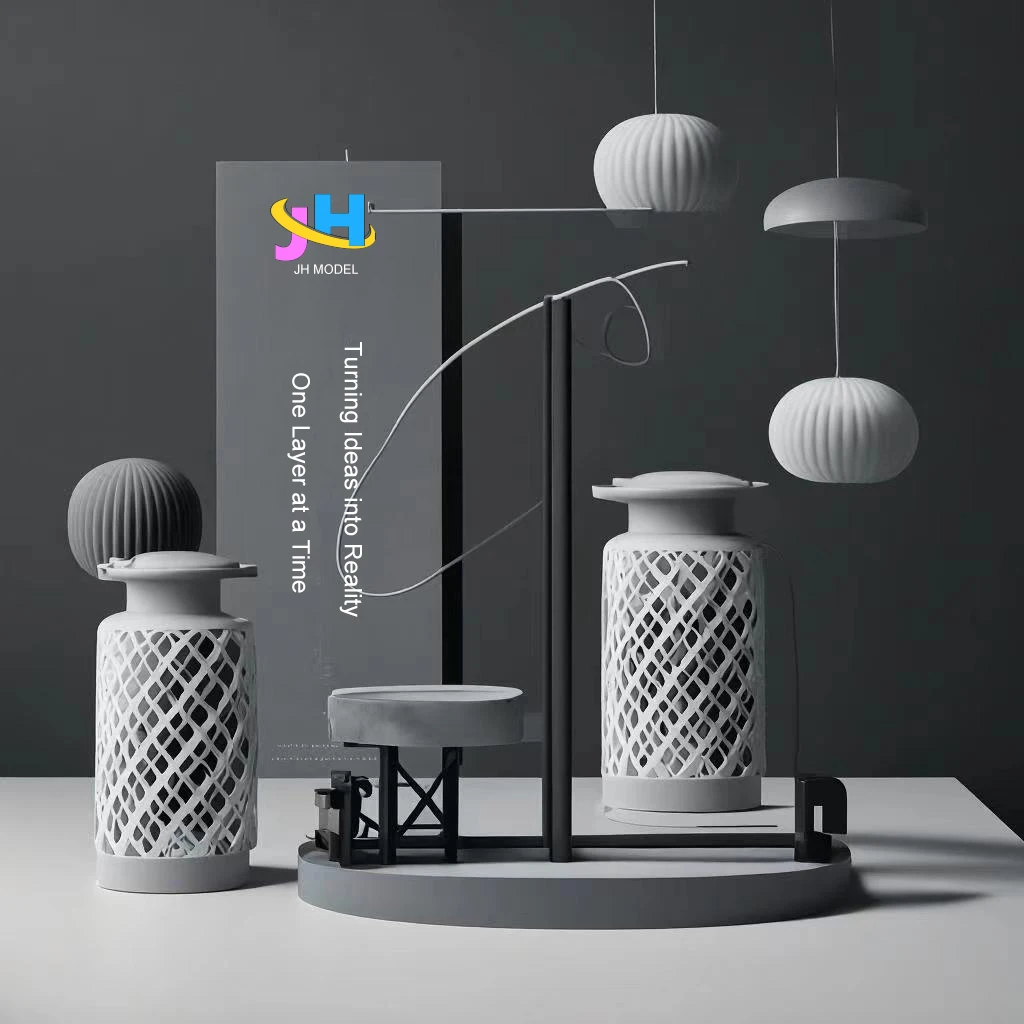
About 3D Printing
What is 3D Printing?
3D printing, also known as additive manufacturing, is a manufacturing process that creates three-dimensional objects by adding material layer by layer. Unlike traditional subtractive manufacturing methods, which involve cutting or shaping material from a solid block, 3D printing builds objects layer by layer from the bottom up. This technology enables the creation of complex and intricate shapes that would be challenging or impossible to produce using traditional manufacturing techniques.

How to order
1, Send us your requirement
2, Quotation offer
3, Place order
4, Start Production
5, Check Quanlity
6, Ship and Delivery

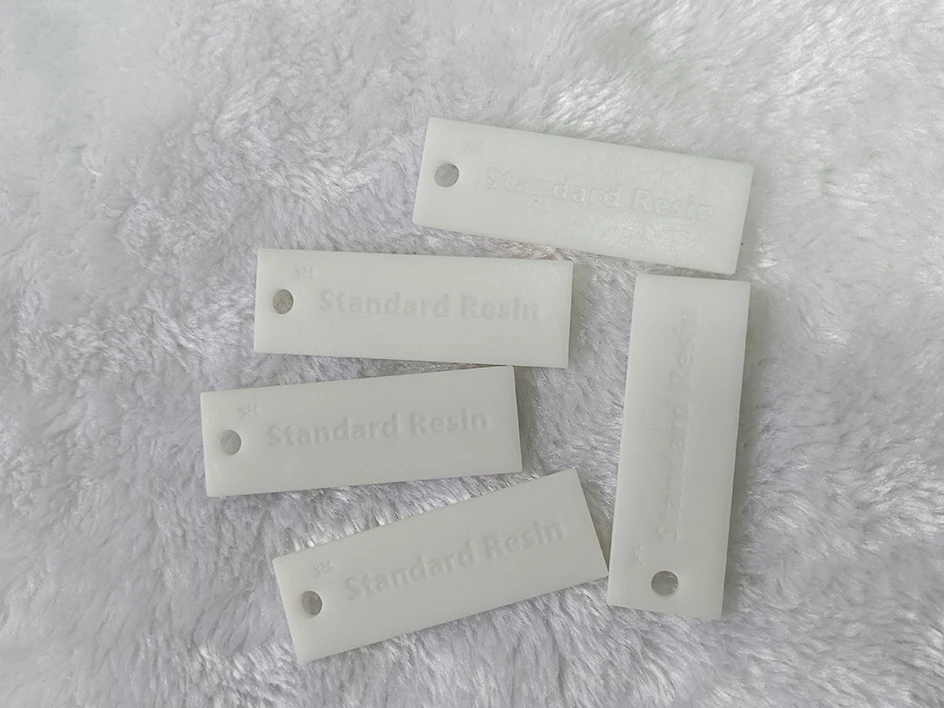
Standard White Resin
SLA standard white resin is a type of 3D printing material designed for use in SLA 3D printers. Its primary and simple feature is its color – it is white. This resin is characterized by its ability to produce high-resolution 3D prints with a smooth and uniform white surface finish. Its neutral white color provides a blank canvas that can be easily painted or finished to achieve specific colors or appearances, making it versatile for various applications, including prototyping, modeling, and artistic creations.
Feture:
Technology SLA
Material Standard Resin
Original Color White
Thermal Deformation 40-50°C
Hardness 84D (ASTM D 2240)
Surface Situation Slight Layer Lines And Scratches
Printing Platform Size 600*600*400mm, 800*800*550mm, 1400*700*500mm
Flexural modulus 2600-2700 Mpa (ASTM D 790)
Flexural strength 72-78 Mpa (ASTM D 790)
Tensile modulus 2200-2500 MPa (ASTM D 638)
Tensile strength 75-85 MPa (ASTM D 638)
Elongation at break 11-16 % (ASTM D 638)
Impact strength notched Izod 55-70 j/m (ASTM D 256)
Tolerance The local accuracy of the product is between 0.2-0.3mm~3.5 ‰, while overall accuracy is hard to control
Post Process Assembly,Insect copper nuts, Physical polishing,Painting, Electroplating, Silkscreen, Water transfer printing, Coating
Wall thickness required 0.8mm above, big parts according to 3D drawings
The advantages of SLA standard resin are:
1, Smooth Finish: SLA white resin produces parts with a smooth surface finish, requiring minimal post-processing for an attractive appearance.
2, High Detail: Allows for intricate and detailed designs, making it ideal for projects requiring precision and fine features.
3, Versatile Post-Processing: Easy to paint, dye, or coat for customization, providing flexibility in achieving desired aesthetics.
4, Design Validation: Excellent for prototyping and design validation due to its ability to showcase intricate designs accurately.
5, Rapid Photopolymerization: Rapid curing during the printing process, ensuring efficient and timely production of parts.
The disadvantages of SLA standard resin are:
1, Brittleness: Standard SLA resin can be relatively brittle, making it less suitable for parts that require high-impact resistance.
2, Limited Durability: It may not withstand prolonged exposure to outdoor or harsh environments, affecting long-term durability.
3, Material Properties: The properties of standard SLA resin can vary, and it may lack specific properties needed for certain applications.
4, UV Sensitivity: SLA resin can be sensitive to UV light, potentially causing degradation or color changes over time when exposed to sunlight.
5, Post-Curing Requirements: Additional curing steps are often needed after printing to achieve optimal material properties, adding time and effort to the printing process.
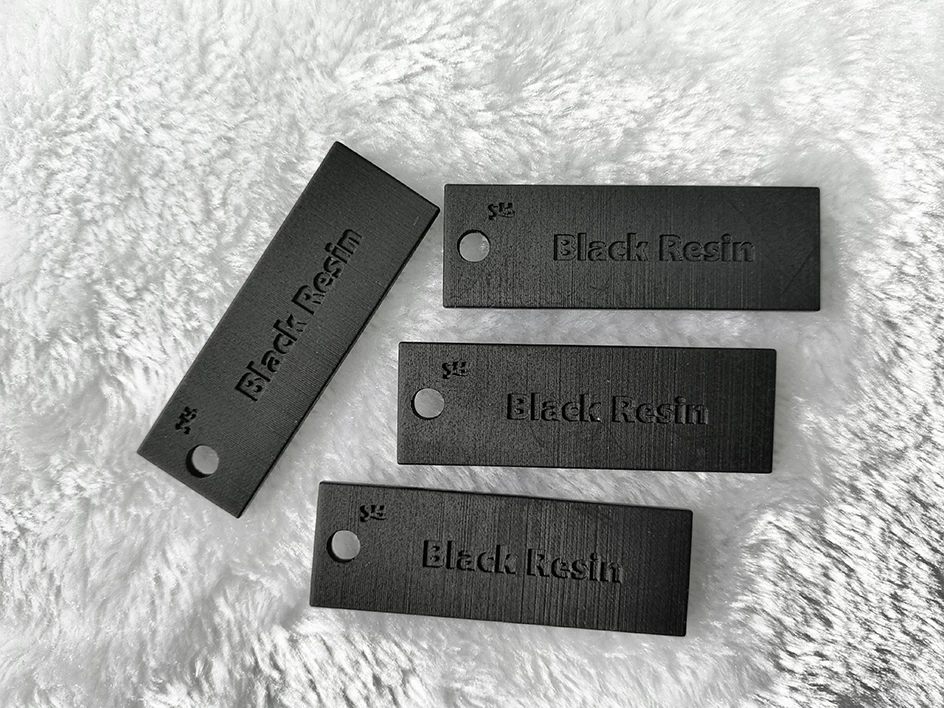
Standard Black Resin
SLA standard black resin is a type of 3D printing material designed for use in SLA 3D printers. Its simple feature is its color – it is black. This resin is characterized by its ability to produce high-resolution 3D prints with a smooth and uniform black surface finish. Its black color provides an attractive and visually appealing appearance, making it suitable for applications where a dark or black finish is desired, such as for functional prototypes, consumer products, and creative projects.
Feature
Technology SLA
Material Standard Resin
Original Color Black
Thermal Deformation 40-50°C
Hardness 83-84D (ASTM D2240)
Surface Situation Slight layer lines and scratches
Printing Platform Size 600*600*400mm
Flexural modulus 1700-2100 Mpa (ASTM D790)
Flexural strength 62-75 Mpa (ASTM D790)
Tensile modulus 2200-2300 MPa (ASTM D638)
Tensile strength 45-50MPa (ASTM D638)
Elongation at break 17-24% (ASTM D638)
Impact strength notched Izod 35-48 j/m (ASTM D256)
Tolerance The local accuracy of the product is between 0.2-0.3mm~3.5 ‰, while overall accuracy is hard to control
Post Process Assembly,Insect copper nuts, Physical polishing,Painting, Electroplating, Silkscreen, Water transfer printing, Coating
Wall thickness required 0.8mm above, big parts according to 3D drawings
The advantages of SLA standard resin are:
1, Smooth Finish: SLA black resin produces parts with a smooth surface finish, requiring minimal post-processing for an attractive appearance.
2, High Detail: Allows for intricate and detailed designs, making it ideal for projects requiring precision and fine features.
3, Versatile Post-Processing: Easy to paint, dye, or coat for customization, providing flexibility in achieving desired aesthetics.
4, Design Validation: Excellent for prototyping and design validation due to its ability to showcase intricate designs accurately.
5, Rapid Photopolymerization: Rapid curing during the printing process, ensuring efficient and timely production of parts.
The disadvantages of SLA standard resin are:
1, Brittleness: Standard SLA resin can be relatively brittle, making it less suitable for parts that require high-impact resistance.
2, Limited Durability: It may not withstand prolonged exposure to outdoor or harsh environments, affecting long-term durability.
3, Material Properties: The properties of standard SLA resin can vary, and it may lack specific properties needed for certain applications.
4, UV Sensitivity: SLA resin can be sensitive to UV light, potentially causing degradation or color changes over time when exposed to sunlight.
5, Post-Curing Requirements: Additional curing steps are often needed after printing to achieve optimal material properties, adding time and effort to the printing process.
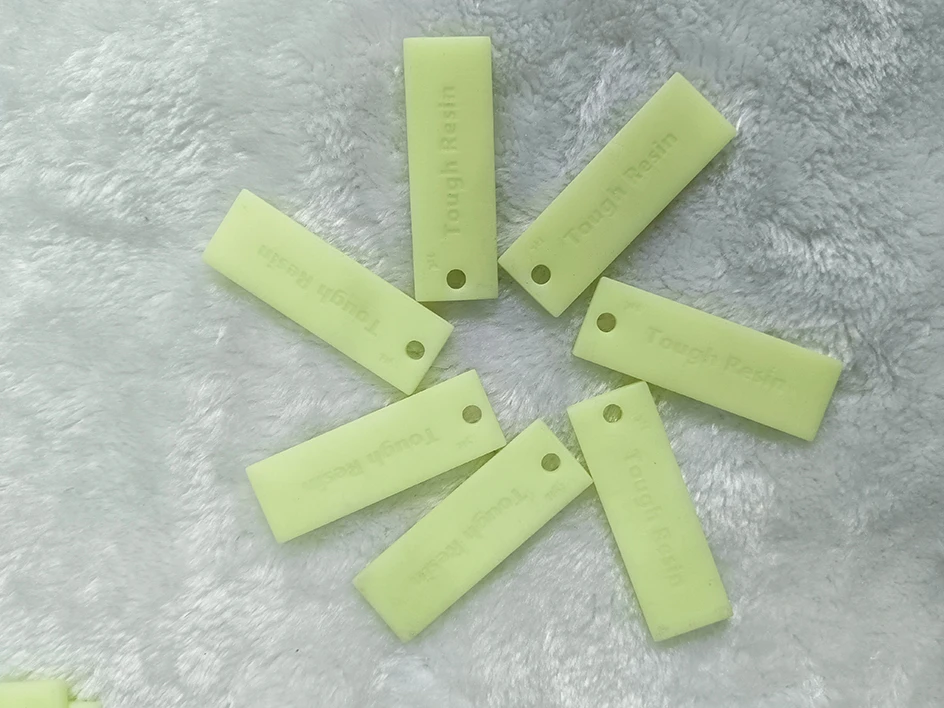
Tough Resin
SLA tough resin is a type of 3D printing material designed for use in SLA 3D printers. Its simple feature is its enhanced mechanical properties, primarily toughness. Here's a brief description of the key features of SLA tough resin:
Enhanced Mechanical Strength: SLA tough resin is formulated to have improved mechanical properties, especially in terms of toughness and impact resistance. This means that 3D prints made with this resin are less likely to break or shatter when subjected to mechanical stress or impacts, making them suitable for functional and load-bearing parts.
In essence, the primary feature of SLA tough resin is its ability to produce 3D prints with better durability and resistance to mechanical forces, making it a preferred choice for applications where strength and toughness are critical.
Features:
Technology SLA
Material Tough Resin
Original Color Green
Thermal Deformation 40-50°C
Hardness 86D (ASTM D2241)
Surface Situation Slight layer lines and scratches
Printing Platform Size 800*800*550mm, 600*600*400mm
Flexural modulus 2100-2400 Mpa (ASTM D790)
Flexural strength 88-93 Mpa (ASTM D790)
Tensile modulus 2100-2300 MPa (ASTM D638)
Tensile strength 38-56MPa (ASTM D638)
Elongation at break 16% (ASTM D638)
Impact strength notched Izod 25-30 j/m (ASTM D256)
Tolerance The local accuracy of the product is between 0.2-0.3mm~3.5 ‰, while overall accuracy is hard to control
Post Process Assembly,Insect copper nuts, Physical polishing,Painting, Electroplating, Silkscreen, Water transfer printing, Coating
Wall thickness required 0.8mm above, big parts according to 3D drawings
The advantages of SLA tough resin are:
1.Enhanced Durability: SLA tough resin offers improved strength and toughness, making it ideal for functional parts requiring resistance to impact and wear.
2.High Impact Resistance: This resin variant can withstand greater impact forces without breaking or deforming, making it suitable for demanding applications.
3.Versatile Applications: Due to its durability, SLA tough resin is versatile and can be used across various industries, including engineering, automotive, and consumer products.
4.Functional Prototyping: Well-suited for prototyping functional parts that need to endure stress and mechanical forces, providing accurate representations for testing and validation.
5.Smooth Surface Finish: Despite its enhanced durability, it maintains a relatively smooth surface finish, requiring minimal post-processing for a polished look.
6.Material Stability: SLA tough resin retains its properties and structural integrity over time, ensuring the longevity and reliability of the printed parts.
The disadvantages of SLA tough resin are:
1.Material Cost: SLA tough resin tends to be more expensive compared to standard resin options, affecting the overall cost of the 3D-printed parts.
2.Post-Curing Requirement: Similar to other SLA resins, tough resin often requires additional curing steps after printing, adding to the time and effort needed in the printing process.
3.Limited Color Options: Depending on the brand and type of tough resin, color options may be more limited compared to standard resins, potentially limiting aesthetic choices for the final product.
4.Not Completely Indestructible: While it offers enhanced durability, it's important to note that SLA tough resin is not indestructible and may still experience damage under extreme stress or harsh conditions.
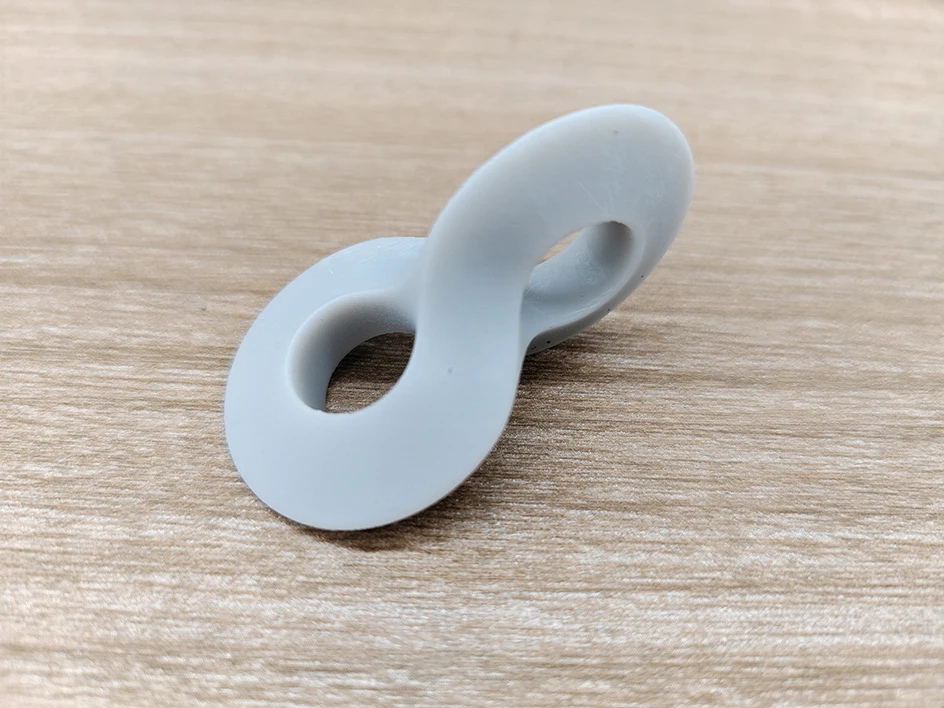
High-Temperature Resin
Temperature resin’s simple feature is its gray color, and it is formulated with enhanced heat resistance.
Gray Color with High Heat Resistance: SLA Gray High-Temperature Resin is gray in color and is characterized by its ability to withstand high temperatures without deforming or losing its structural integrity. This material is ideal for creating 3D prints with a gray finish while ensuring they can endure elevated temperatures without damage.
In summary, the primary feature of SLA Gray High-Temperature Resin is its gray color and its capacity to maintain its physical properties and structural integrity even when exposed to elevated temperatures, making it suitable for applications where heat resistance and a gray appearance are essential.
Features:
Technology SLA
Material Heat Resistant Resin
Original Color Gray
Thermal Deformation 80-90°C
Hardness 85D (ASTM D2240)
Surface Situation Slight layer lines and scratches
Printing Platform Size 600*600*400mm
Flexural modulus 2900-3220 Mpa (ASTM D790)
Flexural strength 64-69 Mpa (ASTM D790)
Tensile modulus 1900-2090 MPa (ASTM D638)
Tensile strength 40-44 MPa (ASTM D638)
Elongation at break 13-20% (ASTM D638)
Impact strength notched Izod 34.4 j/m (ASTM D256)
Tolerance The local accuracy of the product is between 0.2-0.3mm~3.5 ‰, while overall accuracy is hard to control
Post Process Assembly,Insect copper nuts, Physical polishing,Painting, Electroplating, Silkscreen, Water transfer printing, Coating
Wall thickness required 0.8mm above, big parts according to 3D drawings
The advantages of SLA heat-resistant resin are:
1.High Heat Tolerance: Heat-resistant resin can withstand elevated temperatures without deforming, making it suitable for applications in high-temperature environments.
2.Functional Prototyping: Ideal for creating functional prototypes of parts that will be exposed to heat or require good thermal stability.
3.Diverse Applications: Widely used in industries such as automotive, aerospace, and engineering where components may encounter high-temperature conditions during operation.
4.Mechanical Integrity: Retains its structural and mechanical properties even under prolonged exposure to heat, ensuring durability and performance in demanding conditions.
5.Versatility: Provides the versatility of SLA technology while addressing the need for heat resistance, allowing for complex, heat-resistant designs and components to be 3D printed.
The disadvantages of SLA heat-resistant resin are:
1.Limited Heat Threshold: Despite being heat-resistant, the resin may have a maximum temperature threshold beyond which it may start to lose its heat-resistant properties or deform.
2.Potentially Brittle: Heat-resistant resins may lean towards being more brittle compared to standard resins, impacting their ability to absorb mechanical stress or impact at high temperatures.
3.Post-Curing Required: Achieving optimal heat resistance often necessitates post-curing steps, adding to the overall production time and complexity.
4.Cost: Heat-resistant resins are typically more expensive compared to standard resins, affecting the overall cost of 3D printing heat-resistant components.
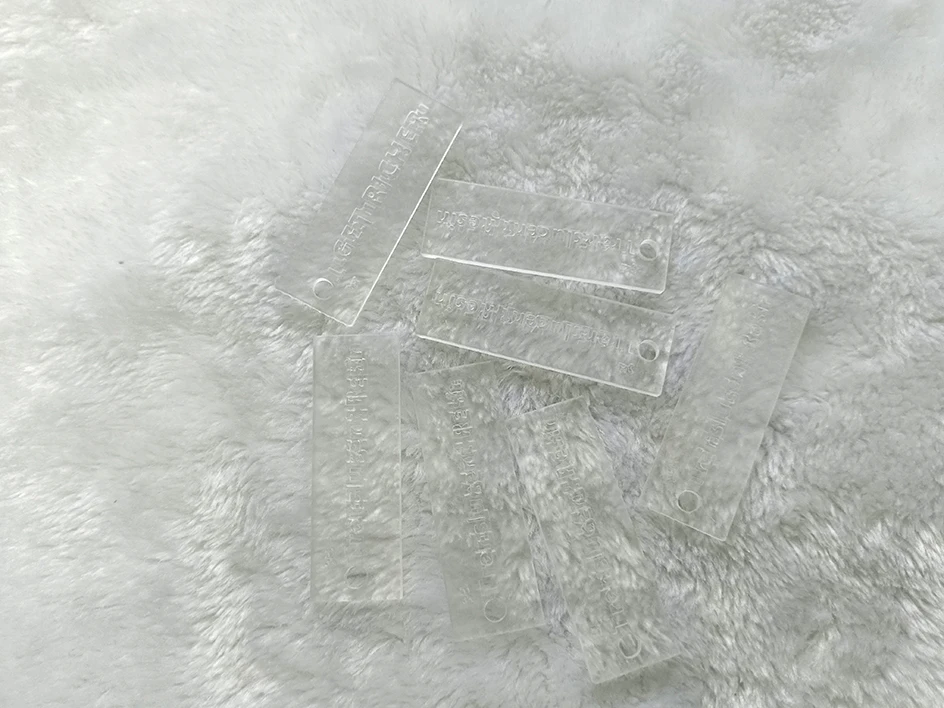
Translucent Resin
Simple feature is its translucency, which means that it allows light to pass through to some extent, creating a semi-transparent or see-through appearance.
Translucent Appearance: SLA Translucent Resin is characterized by its ability to create 3D prints with a semi-transparent or translucent appearance. This material allows light to pass through it, resulting in a visual effect where objects printed with it may be partially see-through or exhibit a diffused light transmission quality.
In essence, the primary feature of SLA Translucent Resin is its capacity to produce 3D prints with a semi-transparent or translucent finish, which is often used for various aesthetic and functional purposes in applications such as product design, lighting, and art.
Features:
Technology SLA
Material Translucent Resin
Original Color Translucent
Thermal Deformation 40-50°C
Hardness 86D (ASTM D2240)
Surface Situation Slight layer lines and scratches
Printing Platform Size 600*600*400mm, 450*450*350mm
Flexural modulus 2100-2400 Mpa (ASTM D790)
Flexural strength 85-90 Mpa (ASTM D790)
Tensile modulus 2100-2300 MPa (ASTM D638)
Tensile strength 38-56MPa (ASTM D638)
Elongation at break 12% (ASTM D638)
Impact strength notched Izod 25-30 j/m (ASTM D256)
Tolerance The local accuracy of the product is between 0.2-0.3mm~3.5 ‰, while overall accuracy is hard to control
Post Process Assembly,Insect copper nuts, Physical polishing,Painting, Electroplating, Silkscreen, Water transfer printing, Coating
Wall thickness required 0.8mm above, big parts according to 3D drawings
The advantages of SLA translucent resin are:
1.Light Transmission: Translucent resin allows light to pass through, making it ideal for applications requiring light diffusion or a soft glow effect.
2.Aesthetic Appeal: Provides a visually appealing, semi-transparent appearance, suitable for creating visually appealing prototypes, designs, or artistic pieces.
3.Versatile Design Options: Enables the creation of parts with varying levels of translucency, allowing for customization based on the desired amount of light transmission and opacity.
4.Prototyping for Lighting: Perfect for prototyping lighting components, light fixtures, or designs where controlled light diffusion is essential.
5.Durable and Functional: While achieving translucency, the resin still maintains a level of strength and durability, making it suitable for both aesthetic and functional purposes.
The disadvantages of SLA translucent resin are:
1.Limited Strength: Translucent resin may have lower mechanical strength compared to opaque resins, making it less suitable for parts requiring high durability or load-bearing capabilities.
2.Print Layer Visibility: Due to its translucent nature, the layer lines from the 3D printing process may be more visible, affecting the overall surface finish and aesthetic appearance.
3.Potential Yellowing: Over time or with exposure to UV light, the translucent resin may yellow or change in appearance, affecting its original clarity and translucency.
4.Post-Processing Challenges: Achieving a consistent and desired level of translucency may require additional post-processing steps, which can be time-consuming and add complexity to the finishing process.
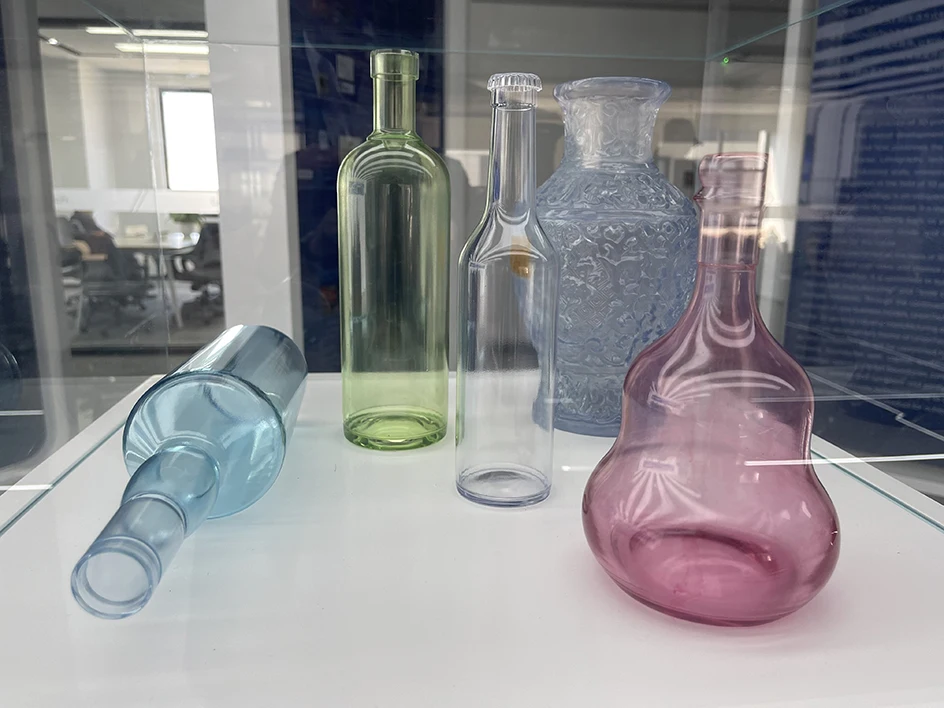
Clear Resin
Clear resin’s simple feature is its transparency, meaning that it has the ability to produce 3D prints with a clear and see-through appearance. Transparency: SLA Clear Resin is characterized by its ability to create 3D prints with a high degree of transparency, resulting in a clear and see-through appearance. This transparency allows light to pass through the printed objects, creating a visually appealing effect.
In essence, the primary feature of SLA Clear Resin is its capacity to produce 3D prints that are transparent, making it suitable for applications where clarity and see-through properties are essential, such as for optical components, lenses, or display prototypes.
Feature:
Technology SLA
Material Clear resin
Original Color Walter Clear
Thermal Deformation 40-50°C
Hardness 86D (ASTM D2240)
Surface Situation Smooth
Printing Platform Size 600*600*400mm, 450*450*350mm
Flexural modulus 2100-2400 Mpa (ASTM D790)
Flexural strength 85-90 Mpa (ASTM D790)
Tensile modulus 2100-2300 MPa (ASTM D638)
Tensile strength 38-56MPa (ASTM D638)
Elongation at break 12% (ASTM D638)
Impact strength notched Izod 25-30 j/m (ASTM D256)
Tolerance The local accuracy of the product is between 0.2-0.3mm~3.5 ‰, while overall accuracy is hard to control
Post Process Insect copper nuts, Assembly, Painting, Electroplating, Silkscreen, Water transfer printing, Laser carving, Coating
Wall thickness required 0.8mm above, big parts according to 3D drawings
The advantages of SLA clear resin are:
1.High Clarity: SLA clear resin offers exceptional transparency, allowing for parts with a glass-like appearance, making it ideal for applications requiring optical clarity.
2.Detailed Visualization: This enables clear and detailed visualization of internal features and structures within the part, making it suitable for prototypes, lenses, and light-guiding components.
3.Smooth Surface Finish: Typically results in a smooth surface finish right off the printer, minimizing the need for extensive post-processing for a polished look.
4.Light Transmission: Excellent light transmission properties, making it suitable for optical and lighting applications where light needs to pass through the part effectively.
5.Visual Prototyping: Perfect for prototyping transparent or translucent products, allowing designers and engineers to visualize and test designs accurately.
The disadvantages of SLA clear resin are:
1.Brittleness: Clear resin can be more brittle compared to other materials, limiting its use in applications that require high-impact resistance or durability.
2.Yellowing Over Time: Clear resin may experience yellowing or discoloration over time, especially when exposed to UV light, affecting its initial clarity and transparency.
3.Post-Processing Challenges: Achieving optimal clarity and removing any visible layer lines may require additional post-processing steps, adding time and effort to the finishing process.
4.Material Cost: SLA clear resin is often more expensive compared to standard opaque resins, impacting the overall cost of the 3D-printed parts.

SLS Nylon
SLS nylon refers to the use of nylon, a thermoplastic material, as a powder material in the SLS process.
Nylon is a popular choice for SLS 3D printing due to its desirable properties, including strength, flexibility, and durability. SLS nylon is commonly used to produce functional prototypes, end-use parts and assemblies with complex geometries. The SLS process creates complex and detailed objects without the need for support structures, as the surrounding powder acts as a temporary support during the printing process.
SLS nylon 3D printing is widely used in a variety of industries that require strong and high-performance plastic parts, including aerospace, automotive, healthcare, and consumer products.
Feature:
Technology SLS
Material Nylon
Original Color White/Dye Black
Thermal Deformation 100-120 °C
Hardness 75D
Surface Situation Rough Granular
Printing Platform Size 700*600*400mm, 600*360*360mm
Flexural modulus 1400 Mpa (ISO 178)
Flexural strength 48-53 Mpa (ISO 178)
Tensile modulus 1600 MPa (ISO 527)
Tensile strength 45-50 MPa (ISO 527)
Elongation at break 18% (ISO 527)
Impact strength notched Izod 35-40 j/m (ISO 179)
Tolerance The local accuracy of the product is between 0.2-0.3mm~3.5 ‰, while overall accuracy is hard to control
Post Process Assembly, Insect copper nuts, Tap thread, Physical polishing, vapor smoothing, Painting, Electroplating, Silkscreen, Water transfer printing, Coating
1 mm above, big parts according to 3D drawings
The advantages of SLS Nylon are:
1.Excellent Mechanical Properties: SLS Nylon offers high tensile strength, durability, and impact resistance, making it suitable for functional prototypes and end-use parts that require mechanical integrity.
2.Versatile Material: It is a versatile material used across various industries due to its ability to simulate a wide range of engineering plastics, making it adaptable for multiple applications.
3.Good Chemical Resistance: SLS Nylon has good resistance to chemicals, oils, and greases, enhancing its suitability for parts exposed to various industrial environments.
4.Heat Resistance: This material can withstand moderate temperatures, making it suitable for applications where heat resistance is required.
5.Lightweight: SLS Nylon is lightweight yet strong, making it ideal for applications where reducing weight is important without compromising on strength.
6.Easy Post-Processing: SLS Nylon parts are easy to post-process, enabling smoothing, dyeing, painting, or coating to achieve the desired finish and appearance.
7.Powder Reusability: Unused powder from the SLS process can be recycled and reused in subsequent prints, reducing material wastage and cost.
8.Complex Geometries: SLS technology allows for the creation of intricate and complex geometries without the need for support structures, providing design flexibility and reducing post-processing effort.
The disadvantages of SLS Nylon are:
1.Surface Roughness: SLS Nylon parts can have a rough surface finish compared to other 3D printing technologies, requiring additional post-processing to achieve a smoother surface if needed.
2.Hygroscopic Nature: Nylon is hygroscopic, meaning it readily absorbs moisture from the environment, which can affect its properties and dimensional accuracy. Proper storage and handling are essential.
3.Limited Color Options: The color choices for SLS Nylon may be limited compared to some other 3D printing materials, potentially restricting design options.
4.Material Cost: SLS Nylon can be relatively expensive compared to other 3D printing materials, affecting the overall cost of the printed parts.
5.High Processing Temperature: SLS requires high operating temperatures during the printing process, making it energy-intensive and necessitating specialized equipment.
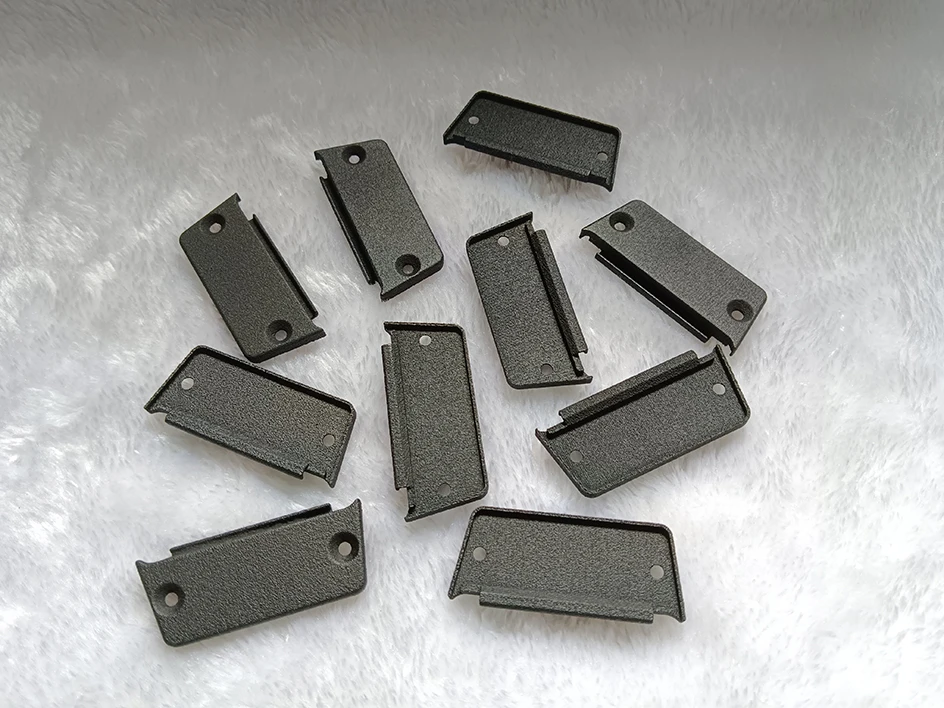
Glass Fiber Nylon
Glass Fiber SLS Nylon is a specific type of 3D printing material that combines nylon with glass fibers. Its simple feature is its composition, which includes both nylon and glass fibers. Here's a brief description of the key features of Glass Fiber SLS Nylon:
Nylon with Glass Fibers: Glass Fiber SLS Nylon is a 3D printing material that blends nylon with glass fibers. This combination imparts additional strength and stiffness to the material, making it ideal for applications where increased mechanical properties are required.
In essence, the primary feature of Glass Fiber SLS Nylon is its composition, which includes the reinforcement of nylon with glass fibers, resulting in a material that offers enhanced mechanical performance. This makes it suitable for a wide range of industrial and engineering applications.
Feature:
Technology SLS
Material 30% Glass Fiber+ Nylon
Original Color White/Dye Black
Thermal Deformation 120-150°C
Hardness 75D
Surface Situation Rough Granular
Printing Platform Size 600*360*360mm
Flexural modulus 2600 Mpa (ISO 178)
Flexural strength 68-70 Mpa (ISO 178)
Tensile modulus 3000 MPa (ISO 527)
Tensile strength 45-50 MPa (ISO 527)
Elongation at break 8 % (ISO 527)
Impact strength notched Izod 35-40 j/m (ISO 179)
Tolerance The local accuracy of the product is between 0.2-0.3mm~3.5 ‰, while overall accuracy is hard to control
Post Process Assembly, Insect copper nuts, Tap thread, Physical polishing, vapor smoothing, Painting, Electroplating, Silkscreen, Water transfer printing, Coating
Wall thickness required 1 mm above, big parts according to 3D drawings
The advantages of SLS Glass-Filled Nylon are:
1.Enhanced Strength and Stiffness: Glass-filled nylon combines the strength and stiffness of nylon with the reinforcing properties of glass fibers, resulting in a material with improved mechanical properties, making it suitable for structurally demanding applications.
2.Excellent Impact Resistance: The addition of glass fibers enhances the impact resistance of nylon, providing durability and toughness to withstand various forces and sudden impacts.
3.Lightweight: Despite its enhanced strength, glass-filled nylon remains lightweight, making it an excellent choice for applications where reducing weight is important without compromising on mechanical performance.
4.Chemical Resistance: Glass-filled nylon is resistant to various chemicals, oils, and solvents, allowing for use in environments where exposure to different substances is a concern.
5.Dimensional Stability: The addition of glass fibers helps reduce the tendency of nylon to warp or deform under high temperatures or loads, ensuring better dimensional stability over time.
6.Good Heat Resistance: Glass-filled nylon exhibits improved heat resistance compared to standard nylon, allowing for use in applications where exposure to elevated temperatures is expected.
7.Low Thermal Expansion: The addition of glass fibers reduces thermal expansion, providing more predictable and stable dimensions across varying temperature conditions.
8.Reduced Wear and Abrasion: The glass fibers enhance the wear resistance of the material, extending its lifespan and making it suitable for applications subject to friction and abrasion.
The disadvantages of SLS Glass-Filled Nylon are:
1.Cost: Glass-filled nylon can be more expensive compared to standard nylon or other 3D printing materials due to the cost of incorporating glass fibers into the material.
2.Surface Finish: SLS Glass-Filled Nylon may have a rougher surface finish compared to non-filled nylon, requiring additional post-processing for a smoother surface if needed.
3.Increased Friction During Processing: The presence of glass fibers can increase friction during the printing process, potentially affecting print quality and necessitating modifications to printing parameters.
4.Material Sensitivity: Glass-filled nylon is more sensitive to changes in processing conditions, such as temperature and humidity, which can affect print quality and mechanical properties.
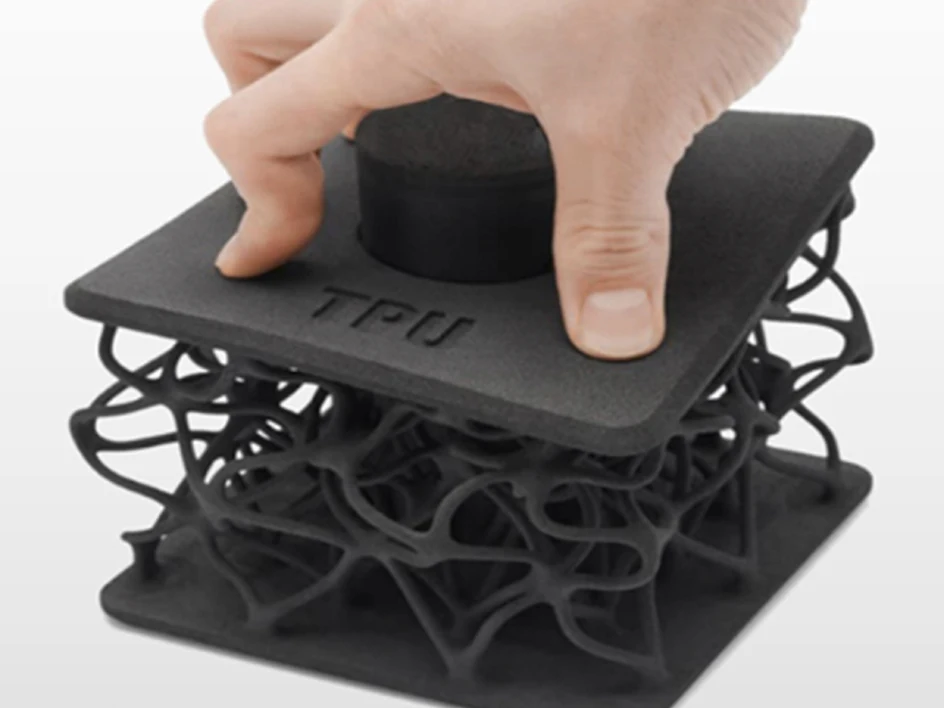
SLS TPU
SLS TPU, is a 3D printing material that is created using selective laser sintering (SLS) technology.
SLS TPU is a flexible and elastic 3D printing material made from thermoplastic polyurethane. It's known for its excellent flexibility, durability, and resistance to abrasion. SLS technology uses a laser to fuse fine TPU powder into solid layers, making it suitable for creating complex and flexible parts. SLS TPU is commonly used for producing items such as gaskets, seals, soft-touch grips, shoe soles, and other applications where a combination of flexibility and strength is required.
Feature
Technology SLS
Material TPU
Original Color White
Thermal Deformation 80-120°C (ISO 11357)
Hardness 85-90A (ISO 11357)
Surface Situation Rough Granular
Printing Platform Size 198*108*200mm
Flexural modulus 70-85 Mpa(DIN EN ISO 178 )
Flexural strength 6.2 Mpa(DIN EN ISO 178 )
Tensile modulus 60-80 MPa (ISO 527)
Tensile strength 18 MPa (ISO 527)
Elongation at break 150-280 % (DIN 53504)
Tolerance The local accuracy of the product is between 0.2-0.3mm~3.5 ‰, while overall accuracy is hard to control
Post Process Silkscreen
Wall thickness required 1 mm above, big parts according to 3D drawings
The advantages of SLS TPU are:
1.Flexibility and Elasticity: TPU is known for its flexibility, elasticity, and rubber-like properties, allowing for the creation of parts that can bend, stretch, and return to their original shape, making it ideal for applications requiring durability and resilience.
2.High Impact Resistance: TPU exhibits excellent impact resistance, making it suitable for producing parts that need to withstand mechanical stress and sudden impacts.
3.Chemical Resistance: TPU has good resistance to various chemicals, oils, and solvents, enhancing its durability in different environments.
4.Good Temperature Resistance: TPU can withstand a wide range of temperatures, making it suitable for applications where exposure to varying temperature conditions is expected.
5.Lightweight: TPU is a lightweight material, providing the advantage of reduced weight in applications where weight is a critical factor.
6.Versatile Applications: Due to its flexibility and durability, SLS TPU is versatile and finds applications in areas such as footwear, automotive components, sporting goods, medical devices, and more.
7.Complex Geometries: SLS technology allows for the creation of intricate and complex geometries with TPU, making it suitable for producing parts with detailed designs.
The disadvantages of SLS TPU are:
1.Limited Strength: TPU, while flexible and elastic, may have lower mechanical strength compared to some other 3D printing materials, making it less suitable for parts requiring high structural integrity.
2.Surface Finish: SLS-printed TPU parts may have a slightly rough or grainy surface finish compared to injection-molded TPU, impacting the overall aesthetic quality.
3.Material Cost: TPU can be relatively more expensive compared to other 3D printing materials, affecting the overall cost of 3D-printed parts.
4.Layer Bonding Issues: Achieving strong layer-to-layer bonding in SLS TPU parts can be challenging, affecting the overall strength and durability of the printed object.
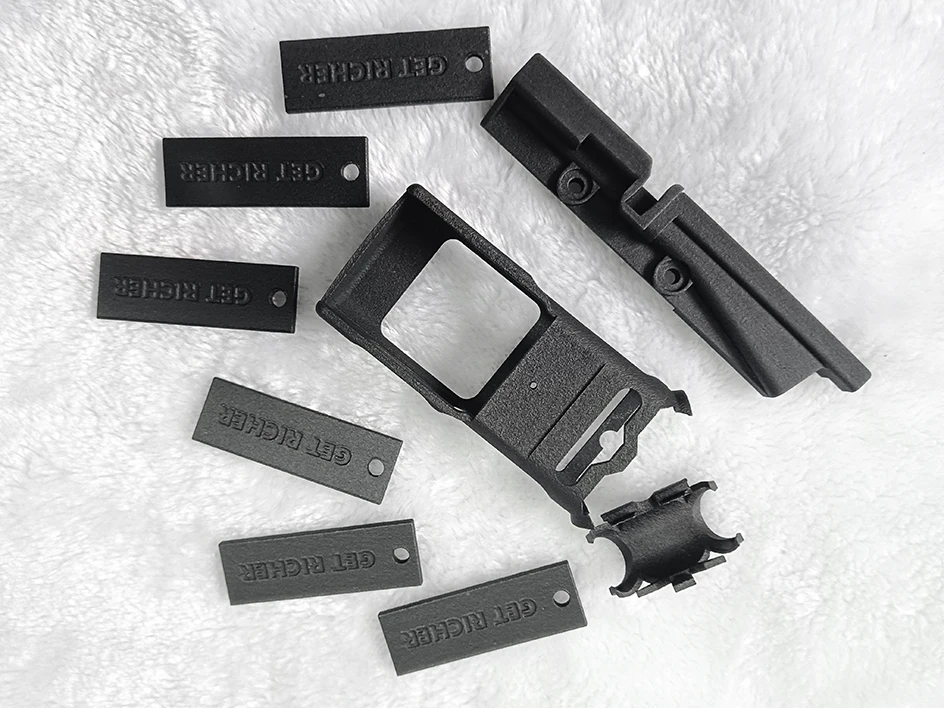
MJF Nylon PA12
MJF works by using a series of inkjet printheads to selectively apply flux and refiners to a bed of powdered material (usually nylon). Infrared energy is then used to fuse the material layer by layer. MJF is known for its high print speeds, making it suitable for rapid prototyping and production applications. The inkjet printhead in the MJF accurately deposits flux and detail agents, resulting in accurate and detailed prints. Nylon PA12 provides the parts with the required mechanical properties such as strength, toughness and flexibility. It is suitable for producing functional prototypes and end-use parts across a variety of industries, including automotive, aerospace, consumer goods, and more.
Feature:
Technology MJF
Material Nylon PA12
Original Color Gray/Paint Black
Thermal Deformation 95-120 °C (ASTM D648)
Hardness 75-85D
Surface Situation Rough Granular
Printing Platform Size 380*380*280mm
Flexural modulus 1800-2400 Mpa (ASTM D790)
Flexural strength 75-85 Mpa (ASTM D790)
Tensile modulus 1700-2200 MPa (ASTM D648)
Tensile strength 45-50 MPa (ASTM D648)
Elongation at break 15-20 % (ASTM D648)
Tolerance The local accuracy of the product is between 0.2-0.3mm~3.5 ‰, while overall accuracy is hard to control
Post Process Assembly, Insect copper nuts, Tap thread, Physical polishing, vapor smoothing, Painting, Electroplating, Silkscreen, Water transfer printing, Coating
Wall thickness required 1 mm above
The advantages of MJF Nylon PA12 are:
1.High Strength and Durability: MJF Nylon PA12 offers excellent mechanical properties, including high tensile strength and durability, making it suitable for functional and structural parts.
2.Lightweight: It is a lightweight material, making it ideal for applications where reducing weight is important without compromising on strength and performance.
3.Precise and Detailed Printing: MJF technology allows for precise and detailed 3D printing, producing intricate parts with smooth surface finishes and fine features.
4.Rapid Printing Speed: MJF is known for its relatively fast printing speed compared to other 3D printing technologies, enabling quick production of parts.
5.Excellent Chemical Resistance: Nylon PA12 has good resistance to chemicals, oils, and solvents, enhancing its suitability for a wide range of industrial applications.
6.Cost-Effectiveness: MJF Nylon PA12 offers a good balance between material cost and performance, providing a cost-effective solution for various prototyping and production needs.
7.Reduced Warping and Shrinkage: MJF Nylon PA12 has minimal warping and shrinkage during the printing process, resulting in accurate and dimensionally stable parts.
The disadvantages of MJF Nylon PA12 are:
1.Limited Material Options: MJF technology primarily uses Nylon PA12, limiting the variety of materials available compared to other 3D printing technologies.
2.Layered Appearance: MJF-printed parts may exhibit a slightly layered or grainy appearance, impacting the aesthetic quality compared to some other 3D printing methods.
3.Material Cost: While Nylon PA12 offers a good balance between cost and performance, the overall cost of MJF Nylon PA12 can still be higher compared to certain other 3D printing materials.
4.Post-Processing Challenges: Achieving a smooth surface finish may require additional post-processing steps, which can add time and effort to the production process.
5.Heat Sensitivity: Nylon PA12 can be sensitive to heat during post-processing or storage, potentially affecting the part's properties if exposed to high temperature

DLP Red Wax
DLP Red Wax 3D printing is a 3D printing process that utilizes a digital light projector to selectively cure layers of a red-colored wax-like photopolymer resin. The resin is exposed to UV light in a layer-by-layer fashion, solidifying it to create a three-dimensional object. The "red wax" appearance refers to the color of the photopolymer resin, which mimics the look of traditional wax used in jewelry casting and modeling.
This technology is commonly used in jewelry design and manufacturing because it allows for the creation of intricate and highly detailed wax patterns for casting jewelry pieces. The red color helps in visualizing the final wax model and is often chosen for its contrast against the white or clear casting materials used in the jewelry industry. DLP Red Wax 3D printing is valued for its precision and ability to produce complex and delicate jewelry designs efficiently.
Feature
Technology DLP
Material Red Wax
Original Color Yellow Red
Thermal Deformation 52-70°C
Hardness 70D
Surface Situation Smooth
Printing Platform Size 198*108*200mm
Flexural modulus 442 Mpa
Flexural strength 12.6 Mpa
Elongation at break 10-13%
Impact strength notched Izod 15.6 j/m
Tolerance The local accuracy of the product is between 0.1-0.15mm~2 ‰, while overall accuracy is hard to control
Post Process Physical polishing, Painting, Electroplating, Silkscreen, Water transfer printing, Coating
Wall thickness required 0.5mm above
The advantages of DLP red wax are:
1.Realistic Appearance: DLP red wax replicates the visual characteristics of wax, making it ideal for jewelry, figure design, and casting applications where a traditional wax aesthetic is desired.
2.Smooth Surface Finish: Red wax can produce intricate and detailed parts with a smooth surface finish, achieving fine details and complex geometries accurately.
3.Easy Casting: Red wax is designed for investment casting processes, allowing for precise, high-quality casting with minimal residue and ash after burnout.
4.High Precision: DLP technology enables high precision and accuracy, ensuring that the wax models closely match the intended design, critical for jewelry and dental applications.
5.No Carving Needed: Unlike traditional wax carving, DLP red wax eliminates the need for manual sculpting, saving time and effort in the design and production process.
6.Cost-Efficient: DLP red wax can be a cost-effective solution for creating intricate wax patterns for investment casting, particularly for small-scale production or custom jewelry designs.
7.Consistency and Reproducibility: DLP technology allows for consistent and reproducible results, ensuring uniform quality and accuracy across multiple wax models.
The disadvantages of DLP red wax are:
1.Material Limitation: DLP red wax is specialized for certain applications, primarily in jewelry, electronic components, figures, and other parts with higher details.
2.Brittleness: Red wax can be relatively brittle, making it vulnerable to breakage or damage during handling or shipping, requiring careful handling.
3.Sensitivity to Heat: Red wax may soften or deform at elevated temperatures, restricting its use in applications that involve exposure to heat or direct sunlight.
4.Limited Color Options: As the name suggests, red wax typically offers a specific color, which may not be suitable for all design or artistic preferences.
5.Material Cost: DLP red wax may be more expensive compared to standard printing materials, affecting the overall cost of 3D printing projects using this material.
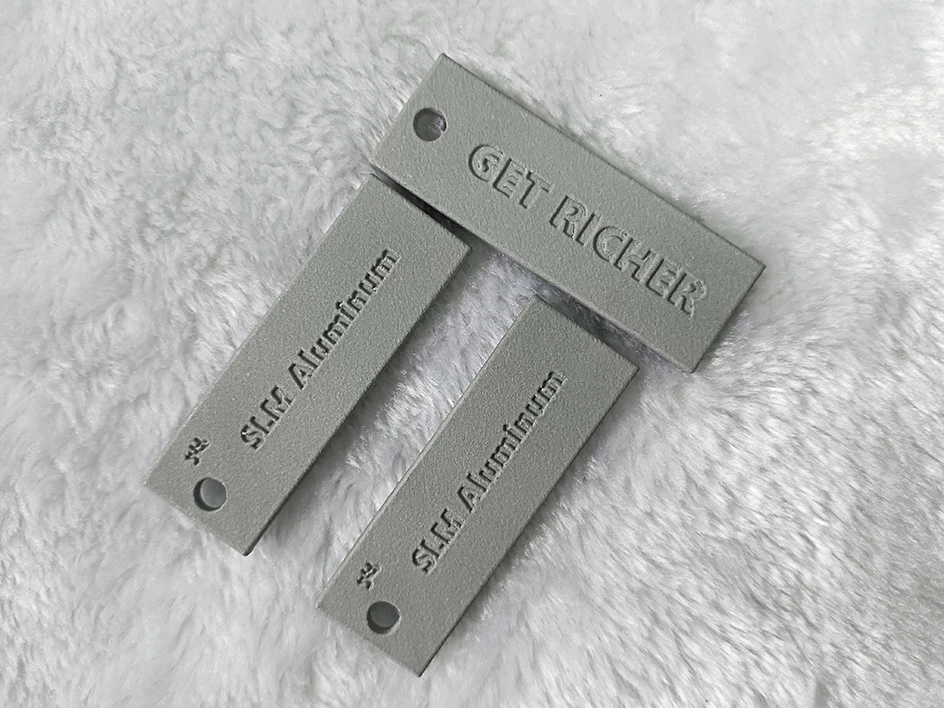
SLM Aluminum
SLM Aluminum is known for its excellent combination of strength, lightweight properties, and good corrosion resistance. The SLM process involves using a high-powered laser to selectively melt and fuse layers of powdered Aluminum metal, building up a 3D object layer by layer.
This material is commonly used in aerospace, automotive, and engineering applications for producing lightweight and strong components, such as brackets, heat sinks, housings, and prototypes. It offers high precision and the ability to create complex geometries that would be challenging to manufacture using traditional methods. SLM Aluminum is valued for its mechanical performance, durability, and suitability for demanding engineering applications
Feature
Technology SLM
Material Aluminum
Original Color Gray
Thermal Deformation 150-180 °C
Hardness 110-120 HBW
Surface Situation Rough Granular
Printing Platform Size 400*300*400mm
Module of elasticity 60-75 Gpa
Yield strength 170-220 Mpa
Tensile strength 300-400 MPa
Elongation at break 6-12%
Tolerance The local accuracy of the product is between 0.2-0.3mm~3.5 ‰, while overall accuracy is hard to control
Post Process Physical polishing, Cnc machining, Heat treating, Painting, Taping Thread, Electroplating, Silkscreen, Coating
Wall thickness required 1 mm above
The advantages of SLM Aluminum are:
1.High Strength-to-Weight Ratio: SLM Aluminum AiSi10Mg offers excellent strength and durability while remaining lightweight, making it ideal for applications where weight reduction is critical without compromising structural integrity.
2.Complex Geometries: SLM technology allows for the production of intricate and complex geometries with precision, enabling the design of highly customized and optimized parts for specific applications.
3.Material Performance: The alloy's composition provides good mechanical properties, including high tensile strength, toughness, and resistance to wear, enhancing its usability in demanding engineering applications.
4.Enhanced Heat Conductivity: Aluminum is known for its excellent thermal conductivity, and SLM Aluminum AiSi10Mg inherits this property, making it suitable for parts exposed to thermal stress or requiring efficient heat dissipation.
5.Rapid Prototyping and Production: SLM offers fast prototyping and production cycles, enabling quicker product development and shorter lead times, making it efficient for both prototyping and low-to-medium volume manufacturing.
6.Material Efficiency: SLM utilizes aluminum powder efficiently during the printing process, minimizing material waste and contributing to cost-effectiveness in the long run.
The disadvantages of SLM Aluminum are:
1.Surface Roughness: SLM-printed aluminum parts may have a rougher surface finish compared to traditional machining methods, requiring additional post-processing to achieve a smoother surface.
2.Anisotropic Properties: SLM-produced aluminum parts can exhibit anisotropic mechanical properties, meaning they may have different strengths and characteristics in different directions due to the layer-by-layer printing process.
3.Material Homogeneity: Achieving uniform material properties throughout the entire printed part can be challenging, impacting its mechanical integrity and consistency.
4.Residual Stresses: The SLM process can introduce residual stresses within the printed aluminum part, affecting its structural stability and potentially leading to warping or deformation.
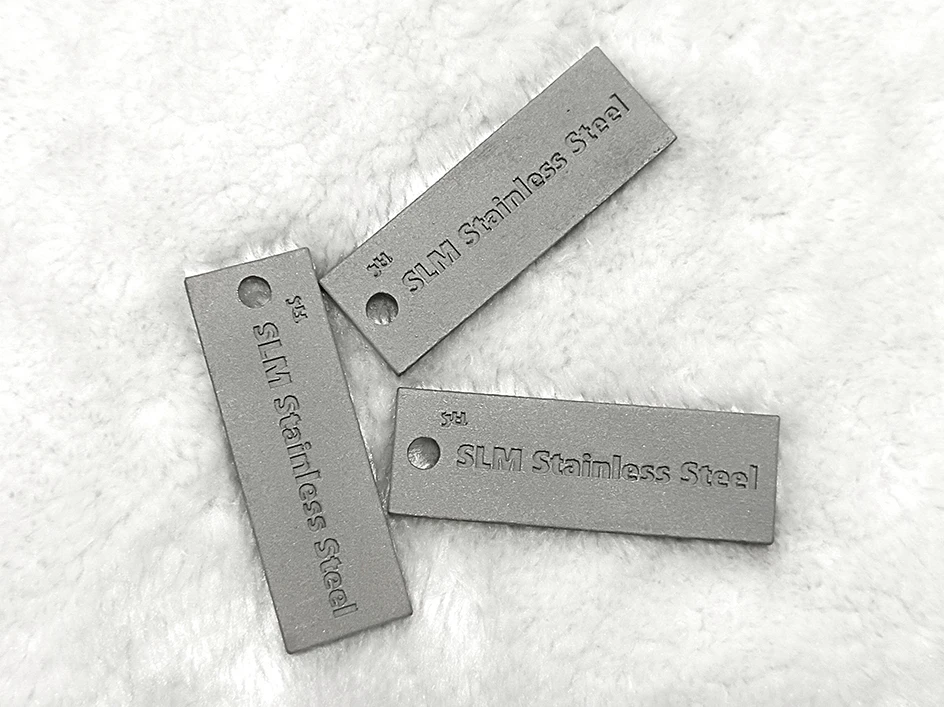
SLM Stainless Steel
SLM Stainless Steel is a metal alloy primarily composed of iron (Fe), chromium (Cr), nickel (Ni), and molybdenum (Mo). It is known for its exceptional corrosion resistance, strength, and durability. The SLM process involves using a high-powered laser to selectively melt and fuse layers of powdered Stainless Steel, building up a 3D object layer by layer.
This material is commonly used in various industries, including aerospace, healthcare, and engineering, for producing strong, corrosion-resistant components like brackets, dental implants, custom surgical instruments, and prototypes. SLM Stainless Steel is valued for its mechanical performance, biocompatibility (in some grades), and suitability for applications where resistance to corrosion and high temperatures is essential.
Feature
Technology SLM
Material Stainless Steel
Original Color Gray
Thermal Deformation 450-500 °C
Hardness 25-30 HRC
Surface Situation Rough Granular
Printing Platform Size 250*250*320mm
Module of elasticity 170-180 Gpa
Yield strength 350-400 Mpa
Tensile strength 580-650 MPa
Elongation at break 25-30 %
Tolerance The local accuracy of the product is between 0.2-0.3mm~3.5 ‰, while overall accuracy is hard to control
Post Process Physical polishing, Cnc machining, Heat treating, Painting, Taping Thread,Electroplating, Silkscreen, Coating
Wall thickness required 1 mm above
The advantages of SLM Stainless Steel are:
1.Excellent Corrosion Resistance: Stainless Steel , when processed using SLM, maintains its excellent resistance to corrosion, making it suitable for applications in aggressive environments, including marine and chemical industries.
2.High Strength and Durability: SLM-produced Stainless Steel offers strong mechanical properties, making it durable and capable of withstanding high stress and load conditions, ensuring longevity and reliability.
3.Biocompatibility: Stainless Steel is often used in biomedical applications due to its biocompatibility, making it suitable for surgical implants and other medical devices.
4.Wide Range of Applications: SLM Stainless Steel finds application in various industries, including aerospace, automotive, healthcare, and manufacturing, owing to its versatile properties and ability to meet diverse requirements.
5.Complex Geometries: SLM enables the production of intricate and complex geometries, allowing for design freedom and the creation of optimized parts for improved performance.
6.Reduced Material Waste: The SLM process is material-efficient, minimizing waste by utilizing only the necessary amount of stainless steel powder for each part, making it a cost-effective and environmentally friendly option.
The disadvantages of SLM Stainless Steel are:
1.Cost: SLM Stainless Steel can be relatively expensive compared to other manufacturing methods or lower-grade stainless steel alloys, impacting the overall cost of the printed parts.
2.Surface Finish: SLM-produced stainless steel parts may have a rougher surface finish compared to traditionally machined parts, necessitating additional post-processing for a smoother surface if required.
3.Anisotropic Properties: SLM can result in anisotropic mechanical properties, meaning the material's properties can vary in different directions, which can be a challenge in applications requiring uniform strength in all directions.
4.Printed Porosity: The SLM process can sometimes introduce microscopic pores or voids in the printed parts, potentially affecting the material's density and mechanical properties.
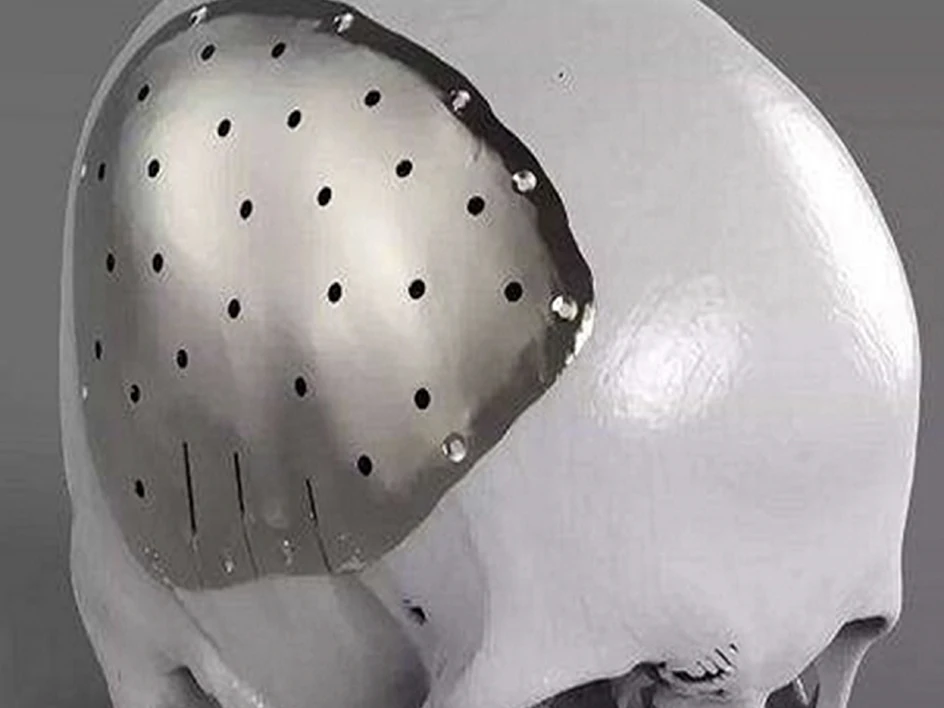
SLM Titanium Alloy
SLM Titanium Alloy is a metal material primarily composed of titanium (Ti) with the addition of other elements such as aluminum (Al) and vanadium (V) to enhance its mechanical properties. It is known for its excellent combination of strength, lightweight properties, and biocompatibility. The SLM process involves using a high-powered laser to selectively melt and fuse layers of powdered Titanium Alloy, building up a 3D object layer by layer.
This material is commonly used in aerospace, medical, and engineering industries for producing lightweight yet strong components, such as aircraft parts, medical implants, custom prosthetics, and automotive components. SLM Titanium Alloy is valued for its mechanical performance, corrosion resistance, and suitability for applications where a balance of strength and biocompatibility is crucial.
Feature
Technology SLM
Material Titanium alloy
Original Color Gray
Thermal Deformation 150-200 °C
Hardness 32-36 HRC
Surface Situation Rough Granular
Printing Platform Size 400*300*400mm
Module of elasticity 110-120 Gpa
Yield strength 900-950 Mpa
Tensile strength 1000-1050 MPa
Elongation at break 6-12%
Tolerance The local accuracy of the product is between 0.2-0.3mm~3.5 ‰, while overall accuracy is hard to control
Post Process Physical polishing, Cnc machining, Heat treating, Painting, Electroplating, Silkscreen, Coating
Wall thickness required 1 mm above
The advantages of SLM Titanium Alloy in a simple description are:
1.High Strength-to-Weight Ratio: Titanium is a titanium alloy known for its exceptional strength while being relatively lightweight, making it ideal for applications where both strength and weight are critical factors.
2.Excellent Corrosion Resistance: Titanium alloys, possess outstanding corrosion resistance, making them suitable for applications in aggressive environments such as marine, aerospace, and chemical industries.
3.Biocompatibility: Titanium alloys are biocompatible, making them widely used in medical implants and devices where they can interact safely with the human body.
4.High-Temperature Resistance: Titaniumcan withstand elevated temperatures, retaining its strength and structural integrity even at high operating temperatures, making it suitable for applications exposed to heat.
5.Outstanding Material Properties: Titanium offers good mechanical properties, including high tensile strength, fatigue strength, and fracture toughness, allowing for the production of durable and reliable parts.
The disadvantages of SLM Titanium Alloy are:
1.Cost: SLM Titanium Alloy can be expensive compared to other materials and manufacturing processes due to the cost of titanium and the advanced SLM technology required for processing.
2.Material Sensitivity: Titanium is sensitive to oxygen and nitrogen exposure during the printing process, which can affect the material properties, making precise control of the printing environment crucial.
3.Surface Finish: SLM-produced titanium parts may have a rougher surface finish compared to traditionally machined parts, necessitating additional post-processing for a smoother surface if required.
4.High Melting Temperature: Titanium has a high melting point, requiring specialized and high-energy laser sources for effective fusion during the SLM process, which can increase the overall energy consumption and operational costs.
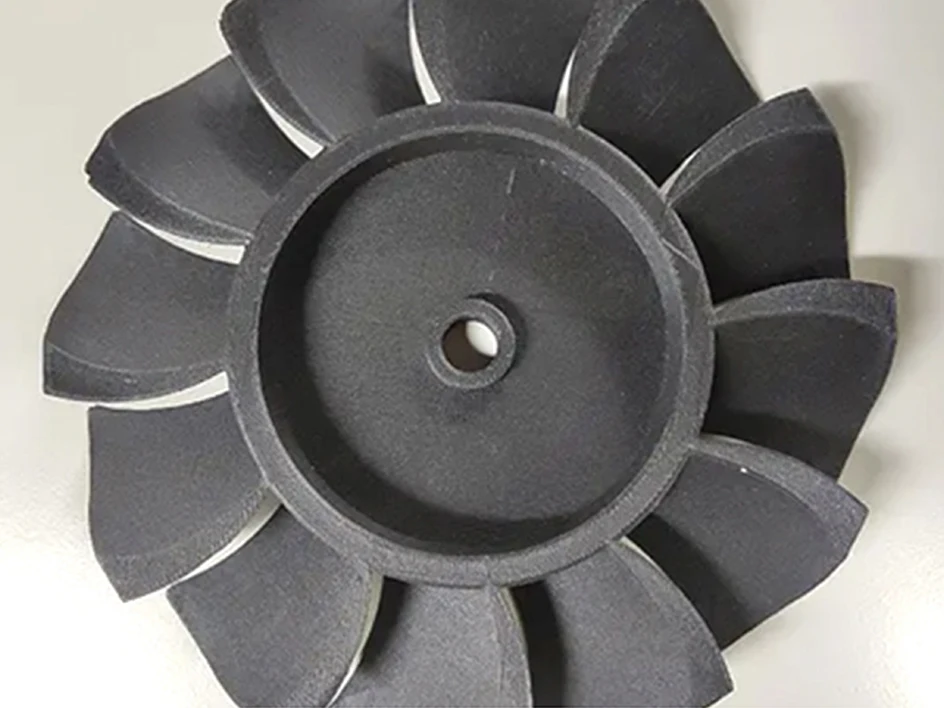
FDM ABS
FDM ABS refers to the use of ABS material in the FDM 3D printing process. FDM is a popular 3D printing technology where a thermoplastic filament, such as ABS, is melted and extruded layer by layer to create a three-dimensional object.
ABS is a common thermoplastic known for its strength, durability, and resistance to heat and impact. In 3D printing, ABS is often used for creating functional prototypes, mechanical parts, and end-use products. The FDM process with ABS involves heating the filament to its melting point, extruding it through a nozzle, and building up the object layer by layer. ABS is appreciated for its versatility, making it suitable for a wide range of applications in 3D printing.
Feature
Technology FDM
Material ABS
Original Color Black/White
Thermal Deformation 70-90°C (ASTM D648)
Hardness 84D (ASTM D 2240)
Surface Situation Clear Layer Lines And Scratches
Printing Platform Size 1000*610*610 mm
Flexural modulus 1.7-2 Gpa (ASTM D 790)
Flexural strength 50-60 Mpa (ASTM D 790)
Tensile modulus 2-2.2 GPa (ASTM D 638)
Tensile strength 30-35 MPa (ASTM D 638)
Elongation at break 1.8-5.9 % (ASTM D 638)
Impact strength notched Izod 30-70 j/m (ASTM D 256)
Tolerance The local accuracy of the product is between 0.3-0.35mm~4 ‰, while overall accuracy is hard to control
Post Process Insect copper nuts, Assembly, Physical polishing, Painting, Electroplating, Silkscreen, Water transfer printing, Coating
Wall thickness required 0.8mm above, big parts according to 3D drawings
Advantages:
Strength and Durability: ABS is known for its good strength, toughness, and impact resistance, making it suitable for functional prototypes and end-use parts.
Versatility: ABS can be used in a wide range of applications due to its balanced properties, making it suitable for various industries including automotive, electronics, consumer goods, and more.
Ease of Printing: ABS is relatively easy to print using FDM technology, with good adhesion between layers, making it a popular choice for 3D printing.
Post-Processing: ABS is receptive to post-processing techniques like sanding, painting, and acetone vapor smoothing, allowing for improved surface finish and aesthetics.
Temperature Resistance: ABS can withstand a broad temperature range, making it suitable for applications exposed to different environmental conditions.
Chemical Resistance: ABS shows good resistance to many chemicals, making it suitable for applications where exposure to chemicals is expected.
Cost-Effective: ABS filament is typically affordable and widely available, making it a cost-effective choice for 3D printing.
Disadvantages:
Prone to Warping: ABS has a tendency to warp, especially during cooling, leading to potential issues with print bed adhesion and warping of the printed part corners.
Requires Controlled Printing Environment: ABS is sensitive to temperature fluctuations during printing. It often requires a heated build platform and an enclosed printing chamber to minimize warping and improve print quality.
Brittleness: While ABS is tough and impact-resistant, it can be relatively brittle compared to other materials like nylon or polycarbonate.
Layer Adhesion Issues: In some cases, ABS can experience challenges with layer adhesion, resulting in weaker parts.
Not Food-Safe in Raw Form: ABS is not considered food-safe in its raw form, making it less suitable for applications involving direct food contact without appropriate post-processing or coatings.
3D Printing Application
For Aerospace, Automotive and Motorcycle Industry

For Rapid Prototyping:

For Figurer, Fashion, Wearables and Cosplay
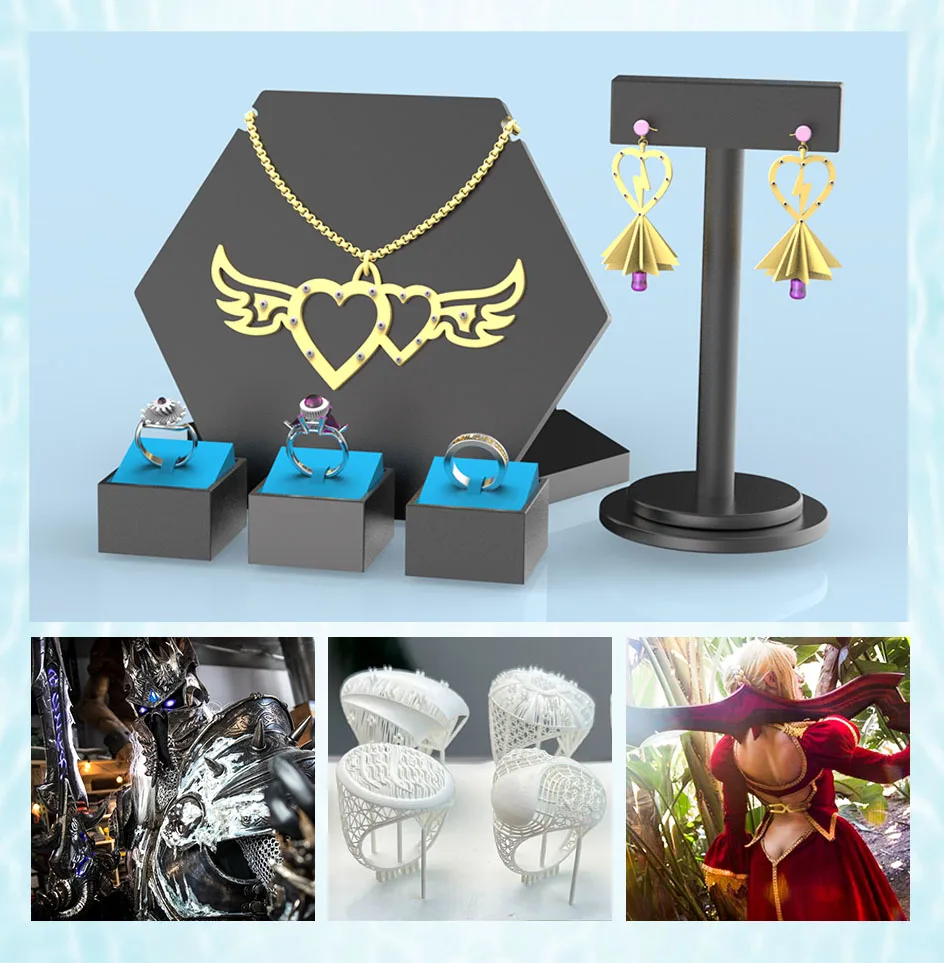
For Architecture and Construction
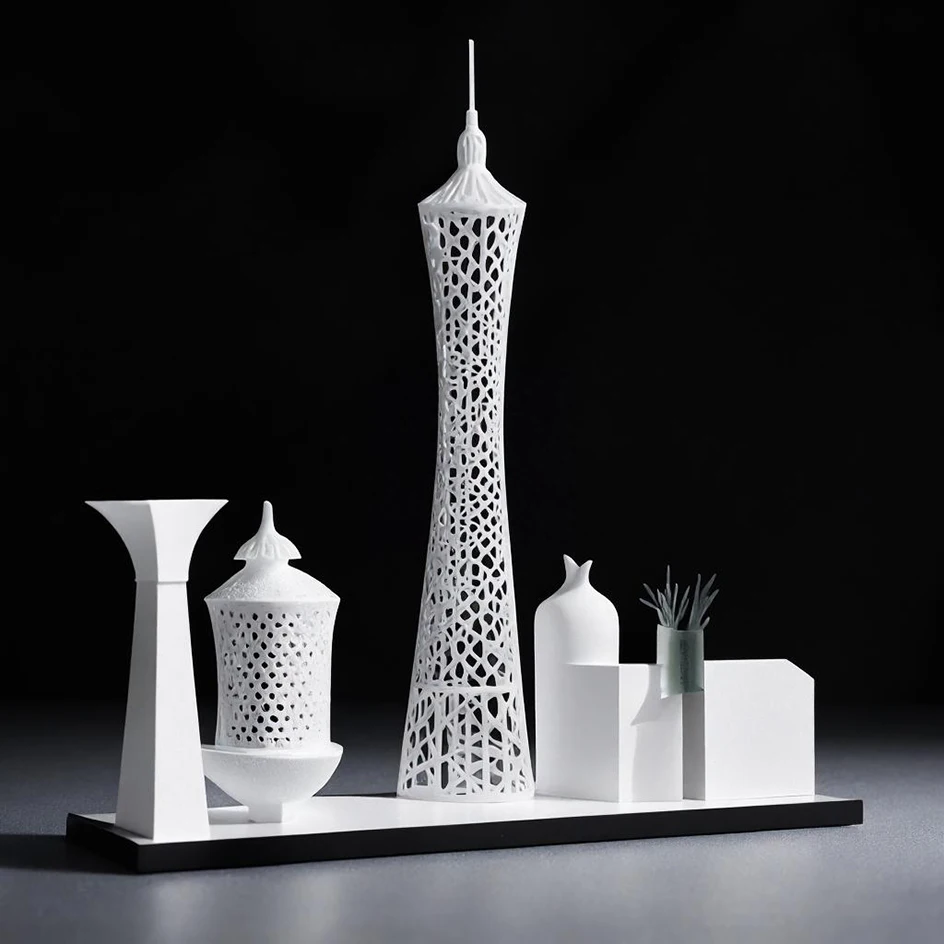
FAQ of custom 3d printing
Q: Can I 3D print custom or personalized objects?
A: Yes, 3D printing is great for creating custom or personalized objects, from prototypes to unique gifts.
Q: What file format is required for 3D printing?
A: The most common file format is STL (Stereolithography), but services might accept other formats as well, eg: STP, 3 DM, obj
Q: How Can I send you the files?
A: You can send us your requirements by Aliexpress chat or mail to jh-aliexpress@hotmail dot com.
Q: What technology do you provide?
A: We provide multi-technologies: SLA, SLS, SLM, MJF, and DLP technologies, Silicon Mold Vacuuming Casting, and CNC machining
Q: What materials can you provide?
A: We supply multi-materials: Resin, Nylon, Nylon+glass fiber, Red Wax, Aluminum, Stainless Steel, Titanium alloy, Brass, ABS, PP, PC, POM, and Acrylic...
Q: How long does it take to 3D print an object?
A: Print time depends on the size, complexity, and the chosen printing speed. Small objects might take a few hours, while large and complex ones can take several days.
Q: Is post-processing required for 3D printed parts?
A: It depends on the desired finish. Post-processing, such as sanding, painting, or assembly, might be necessary for some applications.
Q: Are there size limitations in 3D printing services?
A: Yes, each 3D printer has a specific build volume, so there can be limitations on the size of objects that can be printed.
Q: Are there any design considerations for 3D printing?
A: Yes, designing for 3D printing involves considerations like support structures, layer orientation, and wall thickness to ensure successful printing.
Q: What industries use 3D printing services?
A: 3D printing is used in a wide range of industries, including aerospace, healthcare, automotive, architecture, and consumer goods.
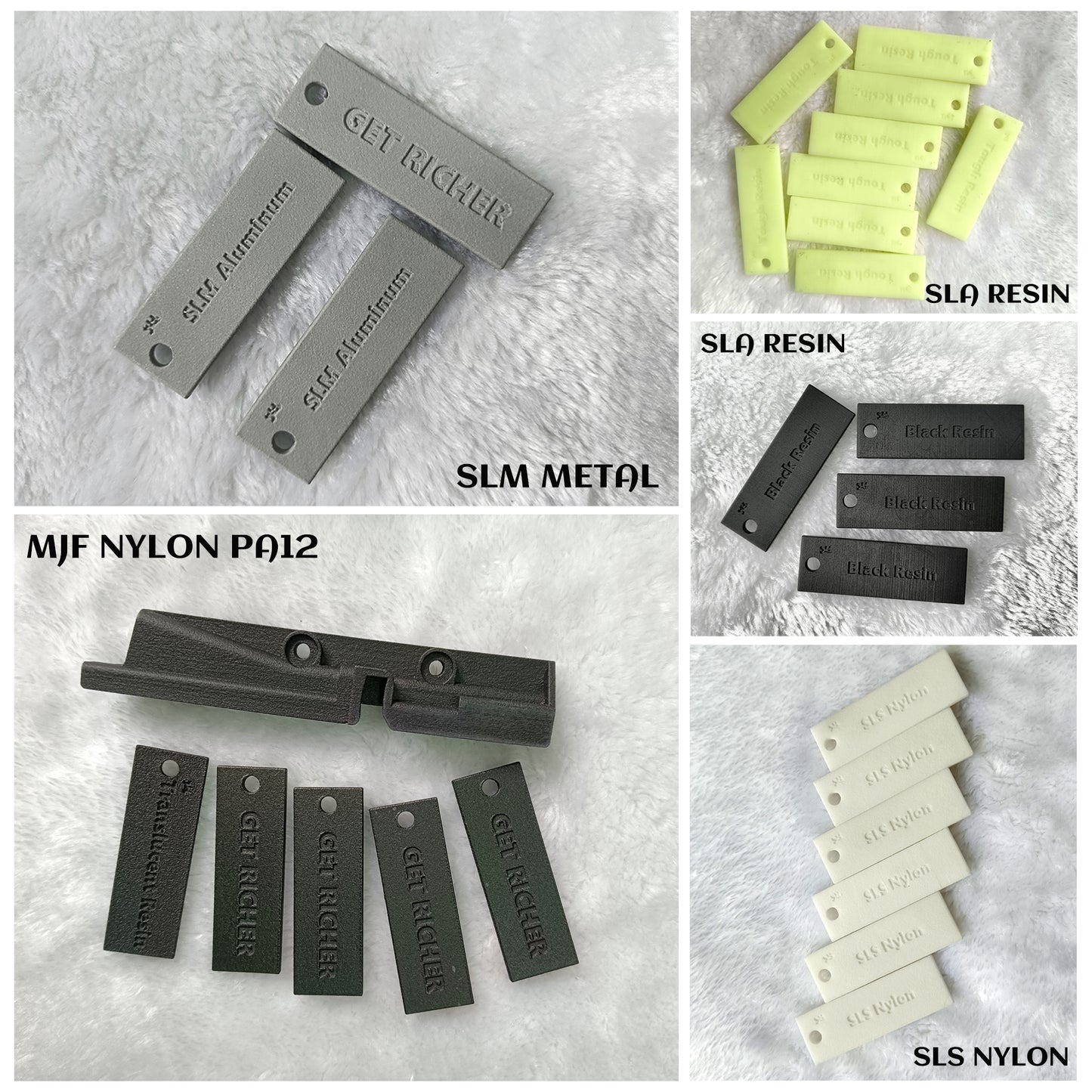
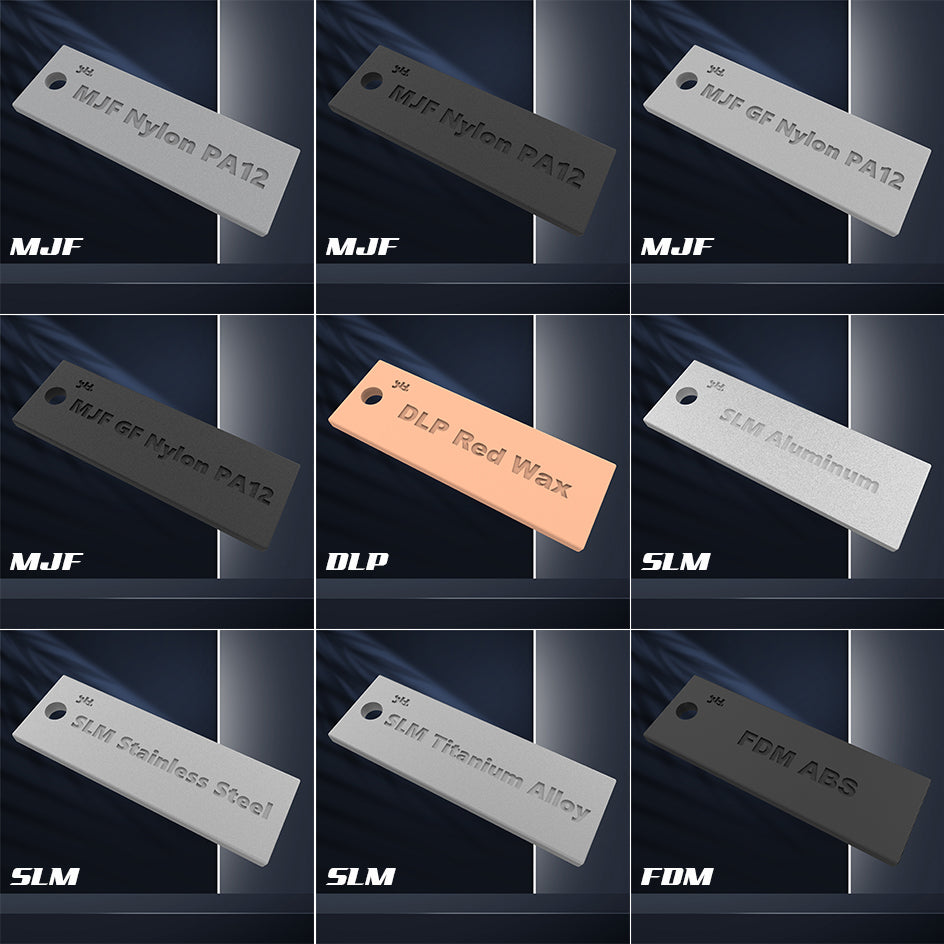
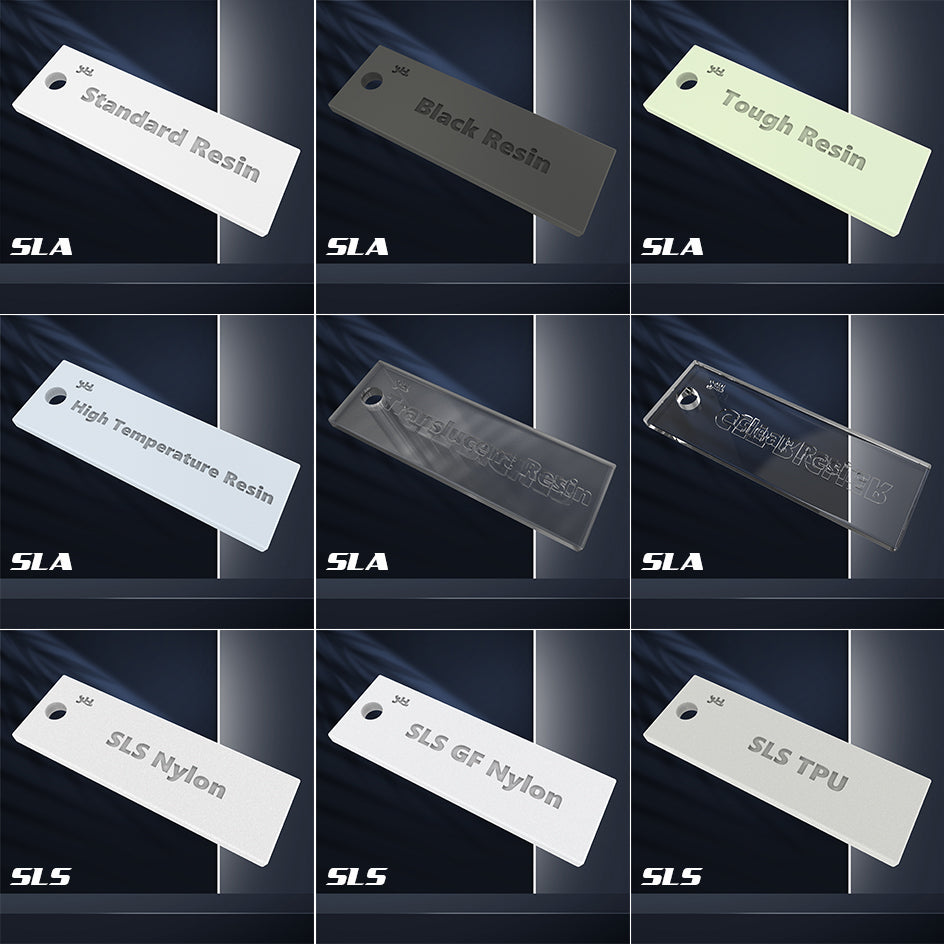
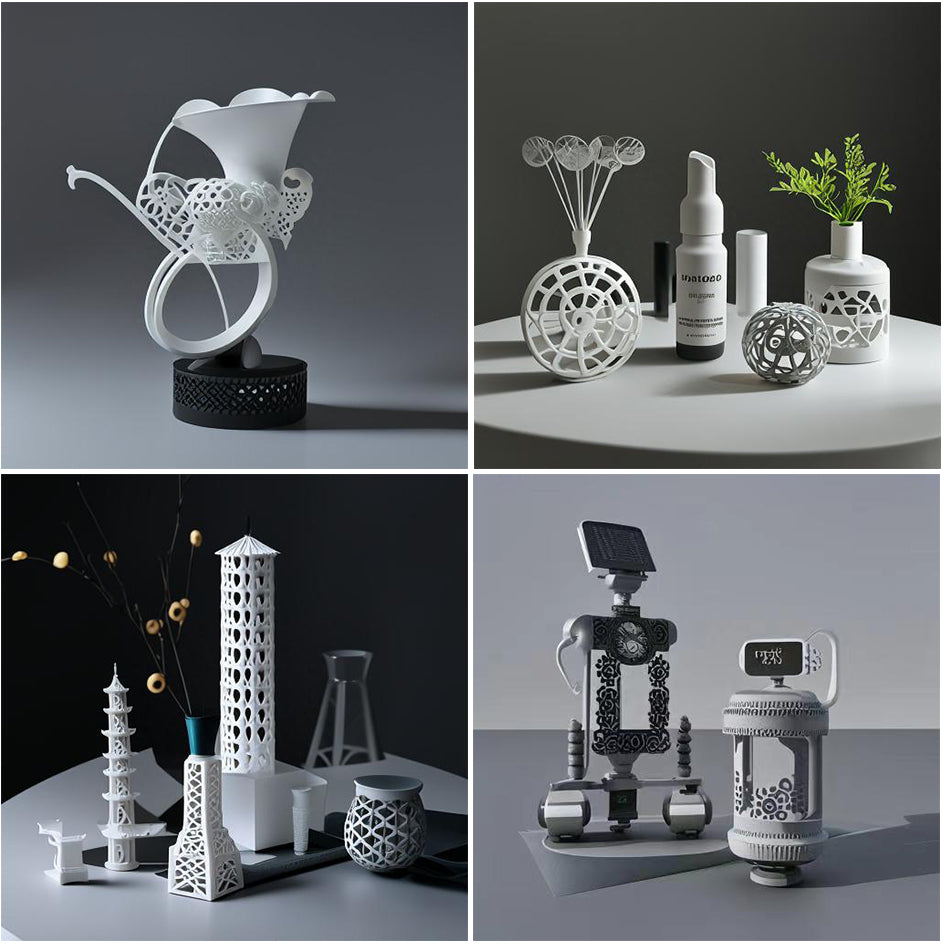
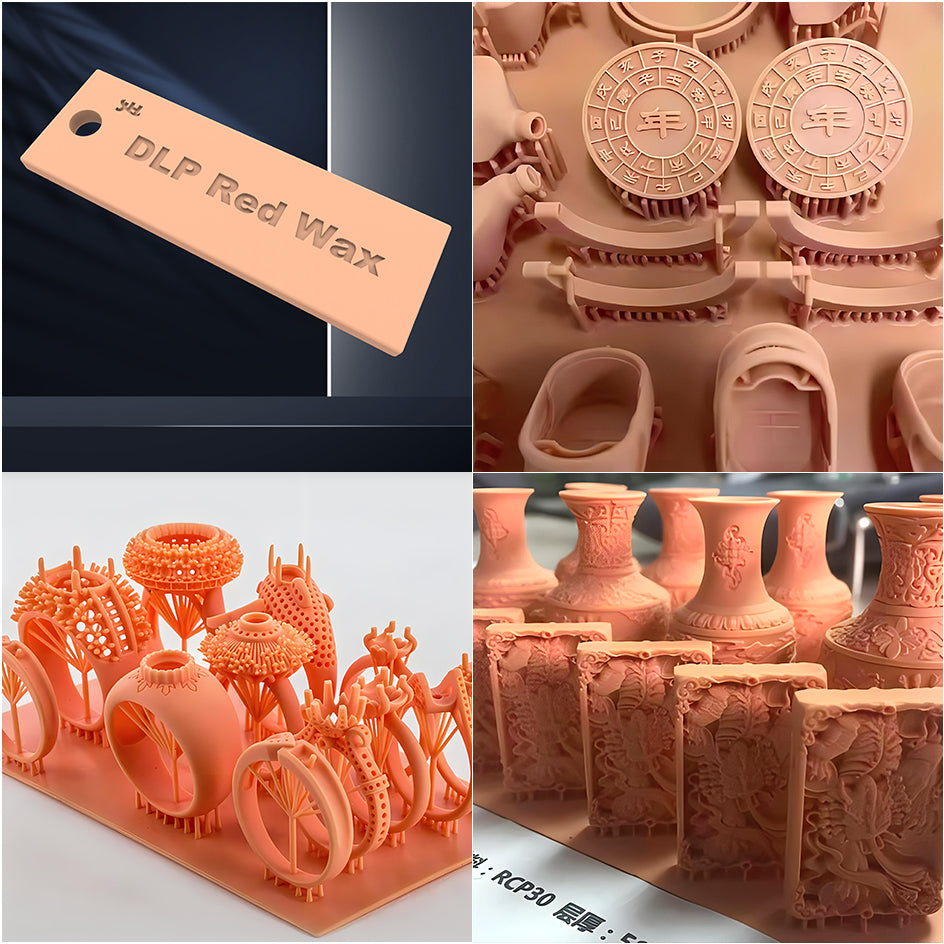
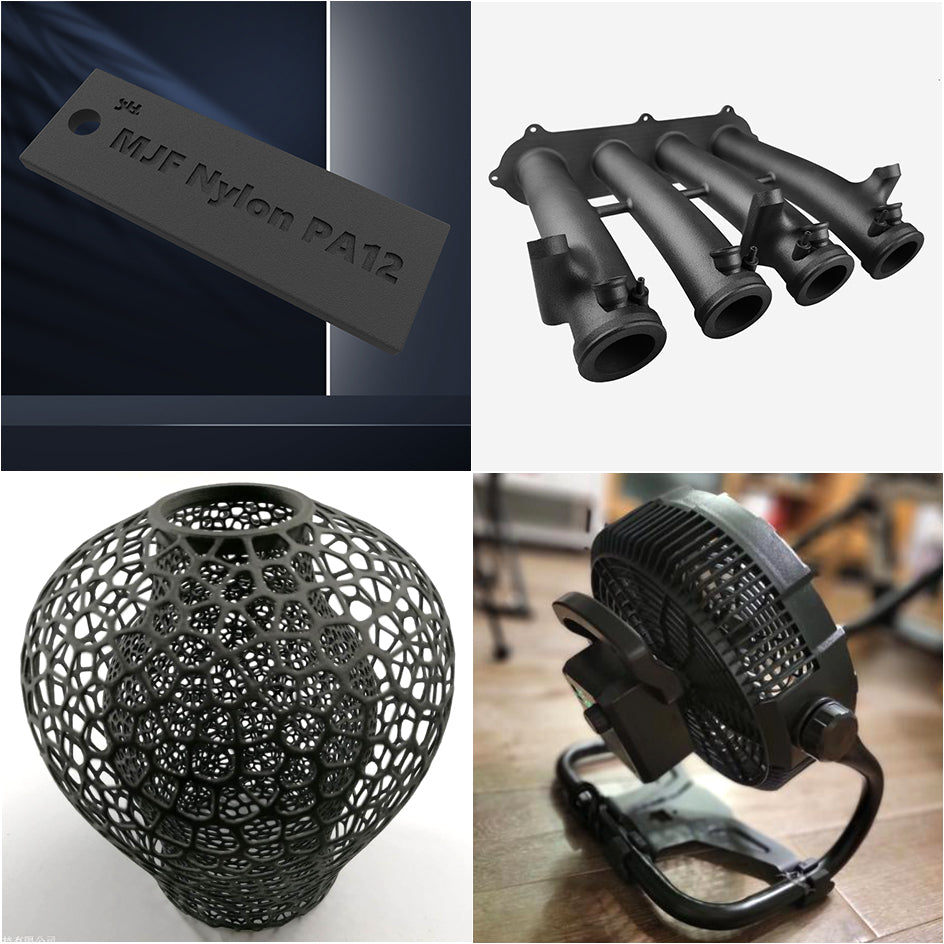
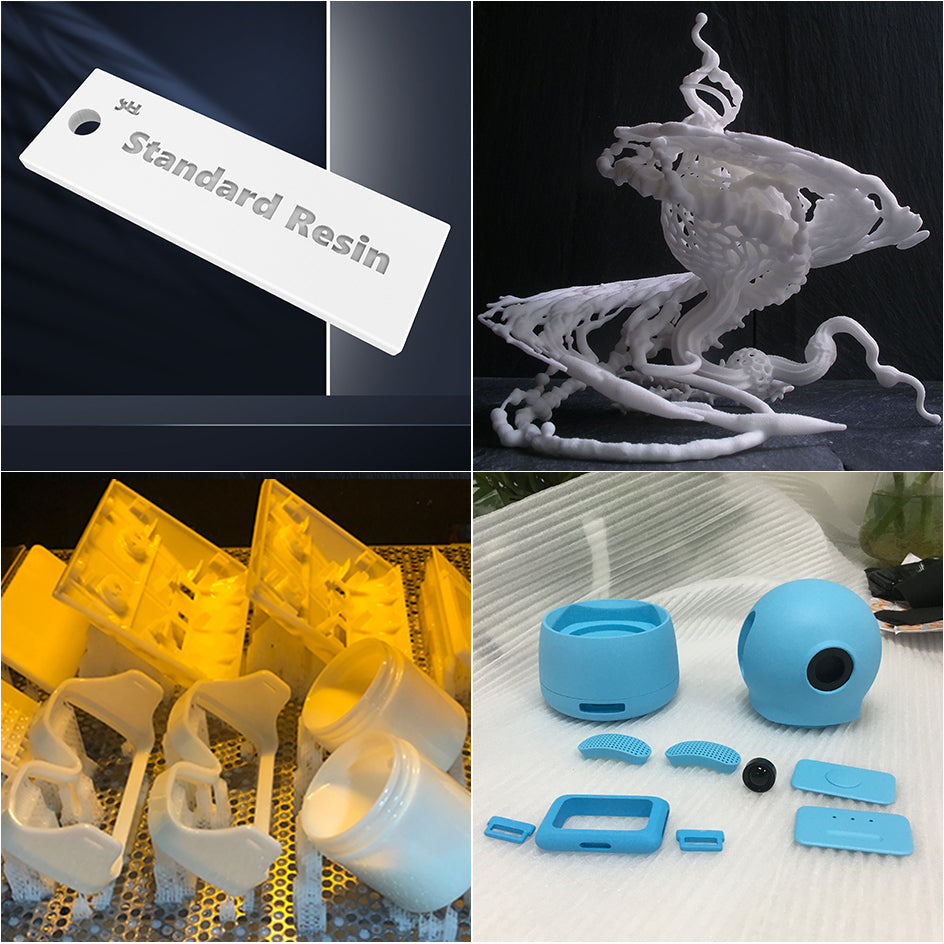
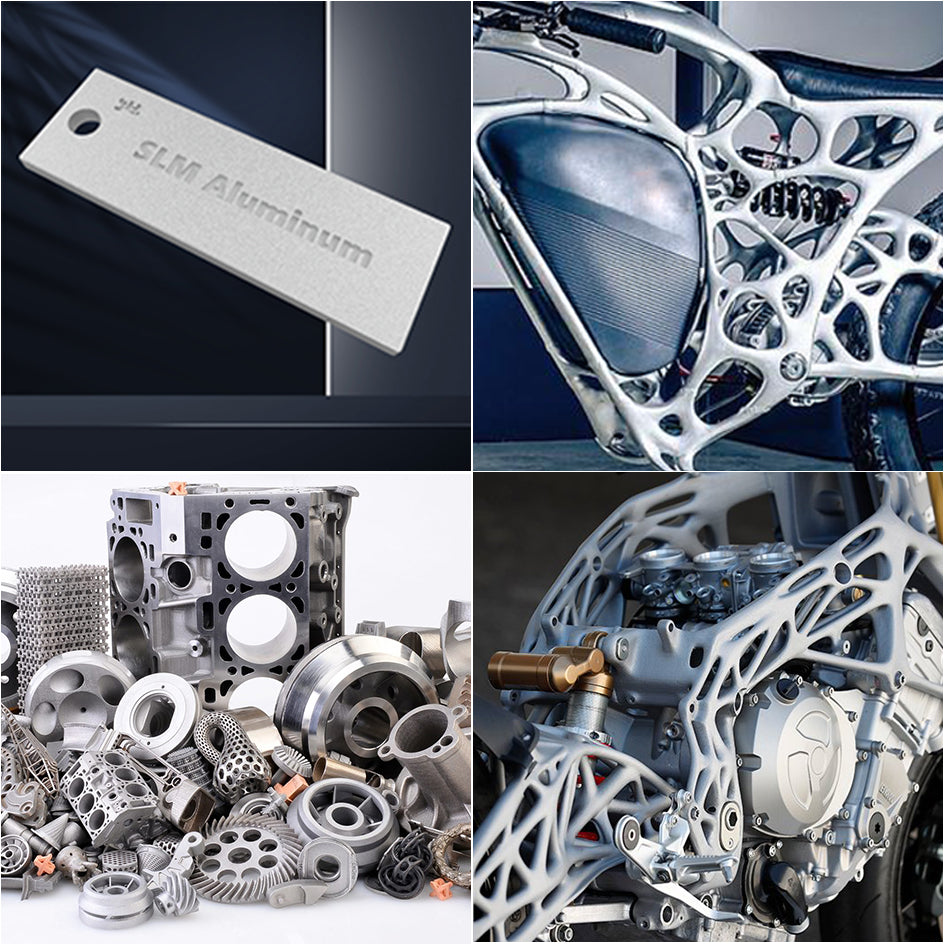