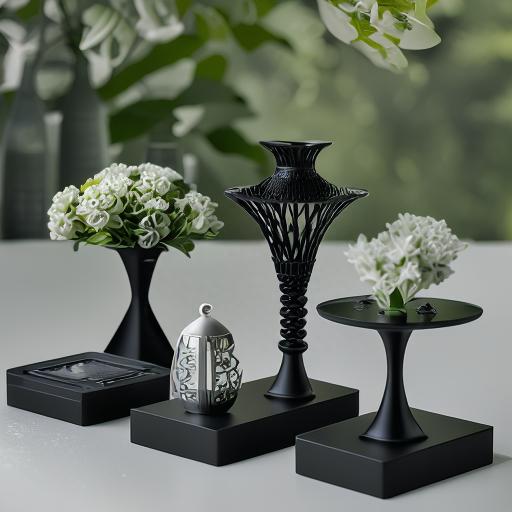
3D Printing Services
Print Your Imagination with Precision and Perfection
3D printing, also known as additive manufacturing, is a manufacturing process that creates three-dimensional objects by adding material layer by layer. Unlike traditional subtractive manufacturing methods, which involve cutting or shaping material from a solid block, 3D printing builds objects layer by layer from the bottom up. This technology enables the creation of complex and intricate shapes that would be challenging or impossible to produce using traditional manufacturing techniques.
How 3D printing works
- Design: The process begins with the creation of a 3D digital model using computer-aided design (CAD) software. This digital model serves as a blueprint for the physical object.
- Slicing: Specialized software called slicers is used to divide the digital model into thin horizontal layers or slices. Each layer represents a cross-section of the final object.
- Printing: The 3D printer interprets these sliced layers and starts building the object layer by layer. It does this by depositing or solidifying material (such as plastic, metal, resin, or even biological material) in accordance with the design. The specific technology and materials used vary depending on the type of 3D printer being used.
- Layering and Bonding: As each layer is added, the material fuses or adheres to the layer beneath it, gradually forming the final object. This process continues until the entire object is completed.
- Post-Processing: After 3D printing is complete, some objects may require additional post-processing steps like cleaning, sanding, painting, or assembly to achieve the desired finish or functionality.
3D printing is used in various industries, including aerospace, automotive, healthcare, architecture, fashion, and consumer goods. Its versatility makes it valuable for rapid prototyping, custom manufacturing, and the creation of complex and customized parts. It has also contributed to advancements in fields like medicine and biotechnology, where it's used for producing prosthetics, dental implants, and tissue scaffolds, among other applications.
Technologies
-
SLA
SLA 3D printing, or Stereolithography, is a technology that uses a liquid resin cured by light to create 3D objects layer by layer. A laser or light source solidifies the liquid resin, shaping the object from the bottom up. It's great for making detailed and precise prototypes or small-scale objects with smooth surfaces.
-
SLS
SLS 3D printing, or Selective Laser Sintering, builds objects by selectively fusing powdered material layer by layer using a laser. The laser melts or sinters the powder to create a solid 3D structure. It's known for making strong, functional prototypes and end-use parts in various materials like plastics, metals, or ceramics.
-
MJF
MJF, or Multi Jet Fusion, is a 3D printing technology that uses a liquid binding agent and a fusing agent applied by an array of inkjet nozzles to build up a part layer by layer. The process is known for its speed and ability to create detailed, strong, and functional parts with good surface quality.
-
SLM
SLM, or Selective Laser Melting, is a 3D printing process that uses a high-powered laser to selectively melt and fuse metal powder layer by layer, creating solid metal objects. It's commonly used for manufacturing complex and durable metal parts in various industries.
-
DLP
DLP, or Digital Light Processing, is a 3D printing technology that uses a digital light projector to cure layers of liquid resin to build a 3D object. The projector displays each layer's cross-section, and the resin hardens when exposed to light. DLP is known for its speed and ability to produce detailed prints with a smooth surface finish.
-
FDM
FDM, or Fused Deposition Modeling, is a 3D printing technology that builds objects layer by layer using melted plastic filament. The filament is extruded through a nozzle, and the printer deposits the material in precise patterns to create the final 3D shape. FDM is widely used for its simplicity, cost-effectiveness, and versatility.
SLA - Stereolithography
-
Standard White Resin
-
Tough Resin
-
Standard Black Resin
-
Translucent Resin
-
Clear Resin
SLS - Selective Laser Sintering
-
Nylon
-
Glass Fiber Nylon
-
TPU
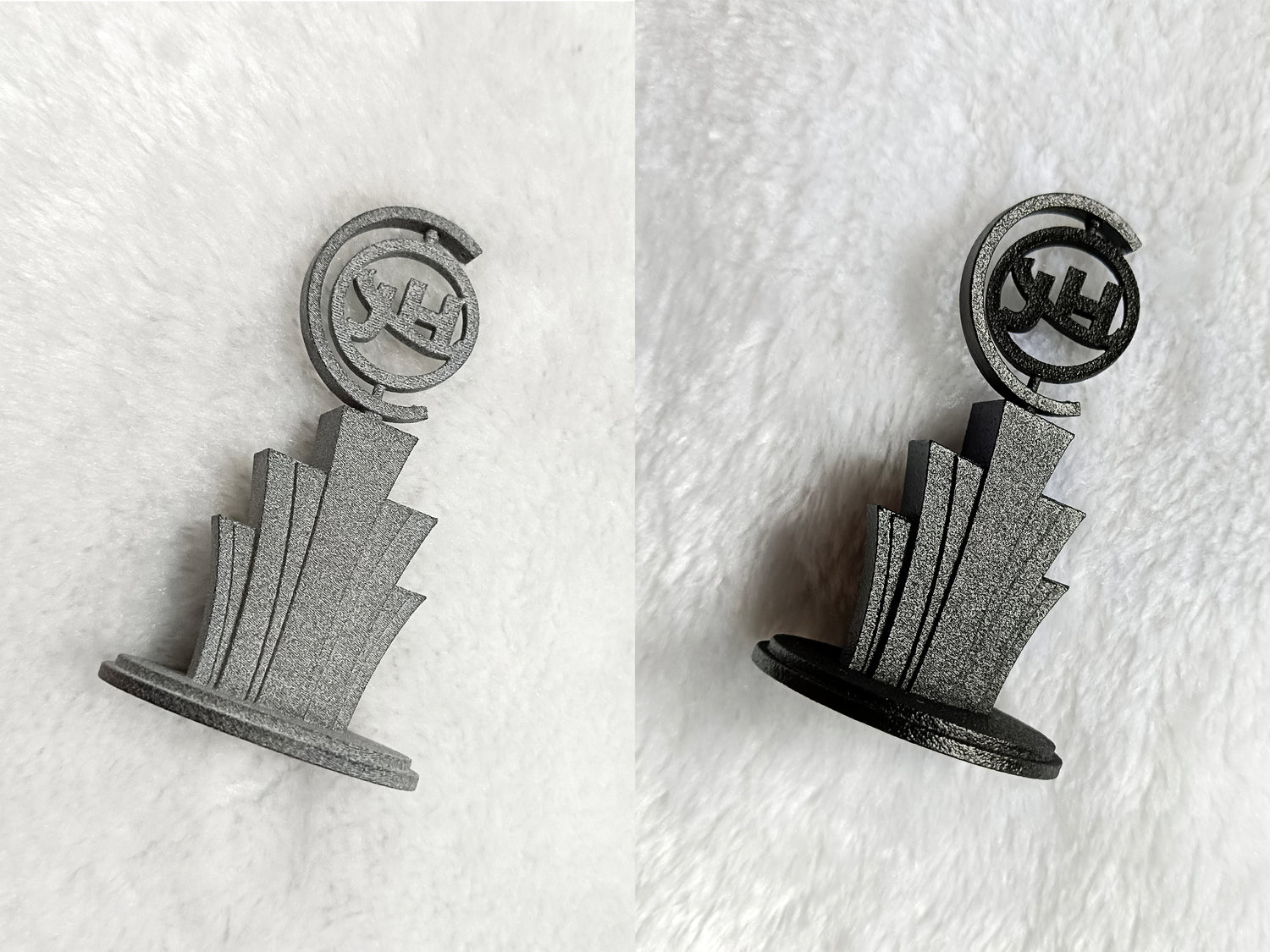
MJF - Multi Jet Fusion
Nylon PA12, Glass Fiber Nylon
SLM - Elective Laser Melting
-
Aluminum
-
Stainless Steel
-
Titanium Alloy
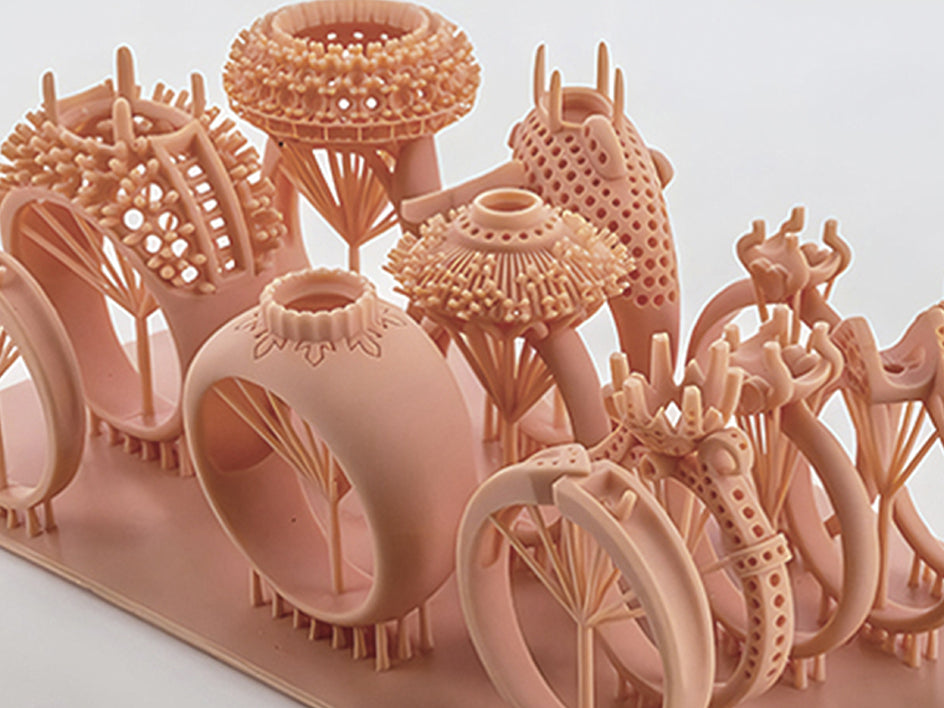
DLP - Digital Light Processing
Red Wax
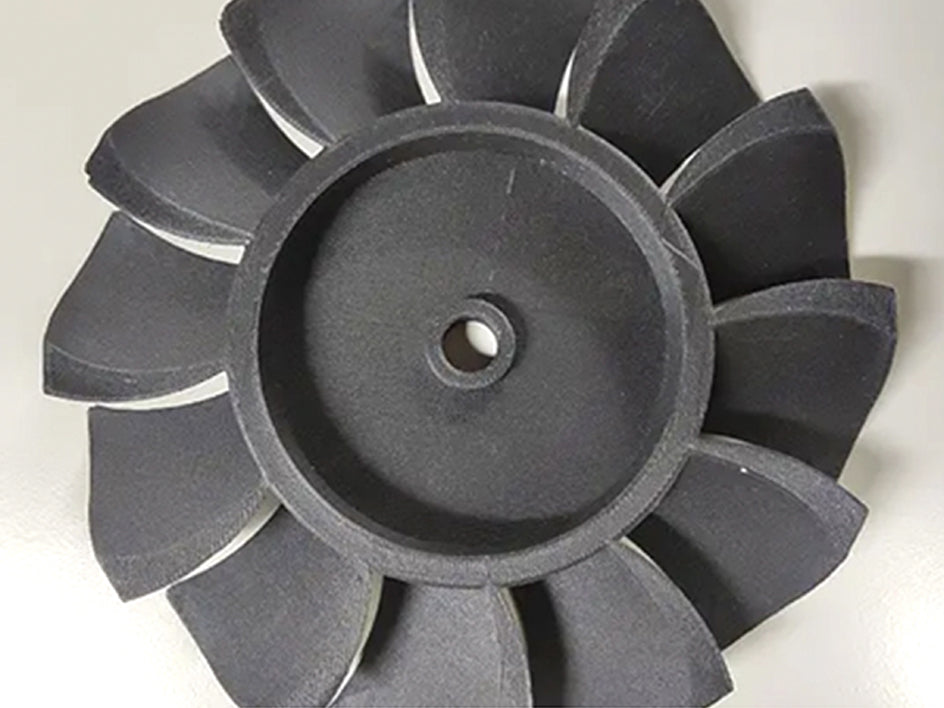
FDM - Fused Deposition Modeling
ABS
What are the advantages of 3D printing?
3D printing offers several advantages across various industries and applications, making it a transformative technology. Some of the key advantages of 3D printing include:
- Design Flexibility: 3D printing allows for the creation of complex and intricate geometries that are difficult or impossible to achieve with traditional manufacturing methods. Designers have more freedom to experiment and optimize designs.
- Rapid Prototyping: 3D printing is widely used for rapid prototyping, enabling engineers and designers to quickly iterate and test their designs, reducing development time and costs.
- Customization: It is well-suited for producing customized or personalized products, such as custom medical implants, orthodontic devices, and consumer goods tailored to individual preferences.
- Cost-Efficiency: For low-volume or one-off production runs, 3D printing can be cost-effective compared to traditional manufacturing processes because it eliminates the need for costly molds and tooling.
- Reduced Material Waste: Traditional manufacturing often generates significant material waste through subtractive processes like milling and cutting. 3D printing, in contrast, is an additive process that generates minimal waste, as material is used only where it is needed.
- Speed to Market: 3D printing can significantly accelerate the product development and manufacturing cycle, allowing companies to bring products to market faster.
- Complex Assemblies: It enables the creation of complex assemblies as a single printed piece, reducing the need for assembly of multiple components.
- Low Minimum Order Quantities: With traditional manufacturing, manufacturers often require large minimum order quantities. 3D printing allows for small-batch production economically, making it more accessible for startups and niche markets.
- Reduced Inventory: On-demand 3D printing can help reduce inventory storage costs by producing items as needed, reducing the need for stockpiling large quantities of goods.
- Material Variety: 3D printing can work with a wide range of materials, including plastics, metals, ceramics, and even biological materials like living cells and tissue.
- Complex Internal Structures: It can create objects with intricate internal structures, such as lattices and honeycombs, which can reduce weight while maintaining strength in aerospace and automotive applications.
- Prototyping in End-Use Materials: Some advanced 3D printing technologies allow for prototyping in the same materials used for the final product, ensuring a more accurate representation of performance.
- Geographic Independence: Digital design files can be easily transmitted electronically, allowing for distributed manufacturing and reducing the need for centralized production facilities.
While 3D printing has numerous advantages, it also has limitations and challenges, such as material limitations, speed constraints for large-scale production, and post-processing requirements. The choice to use 3D printing should consider these factors alongside its benefits.
What are the disadvantages of 3D printing?
Despite its many advantages, 3D printing also has some disadvantages and limitations that should be taken into consideration when deciding whether to use this technology for a particular application. Here are some of the disadvantages of 3D printing:
- Limited Material Selection: While the range of printable materials has expanded over the years, 3D printing still has limitations compared to traditional manufacturing methods. Some materials used in traditional manufacturing, especially in heavy industry, are not easily compatible with 3D printing.
- Surface Finish and Resolution: The surface finish of 3D-printed objects can be rough, especially with certain 3D printing technologies like Fused Deposition Modeling (FDM). Post-processing may be required to achieve a smoother finish.
- Layer Lines: Most 3D-printed objects have visible layer lines, which can affect the aesthetics and functionality of the final product. Post-processing or additional steps may be needed to hide or minimize these lines.
- Speed: 3D printing can be relatively slow, especially when producing large or intricate objects. Mass production using traditional manufacturing methods is generally faster.
- Size Constraints: The build volume of 3D printers can limit the size of objects that can be produced. Larger items may need to be printed in multiple parts and assembled afterward.
- Material Costs: Some 3D printing materials, especially high-performance ones like certain metals and resins, can be expensive. Material costs can become a significant factor in production.
- Post-Processing: Depending on the 3D printing technology and the desired finish, post-processing steps like sanding, painting, or assembly may be required, adding to production time and costs.
- Support Structures: Complex or overhanging geometries may require support structures during printing. These supports must be removed after printing, which can be time-consuming and may leave behind surface imperfections.
- Precision and Tolerance: Achieving tight tolerances and high precision can be challenging with 3D printing, particularly in consumer-grade printers. This can limit its suitability for certain applications.
- Environmental Concerns: Some 3D printing materials emit fumes or odors during the printing process, and the disposal of waste materials can be an environmental concern. Additionally, the energy consumption of some 3D printers can be relatively high.
- Limited Production Speed: 3D printing is not well-suited for high-volume mass production. Traditional manufacturing methods like injection molding and casting are more efficient for large quantities.
It's essential to carefully evaluate the specific requirements of a project and the advantages and disadvantages of 3D printing technology to determine whether it's the right choice for a particular application. In many cases, 3D printing can complement traditional manufacturing methods rather than replacing them entirely.