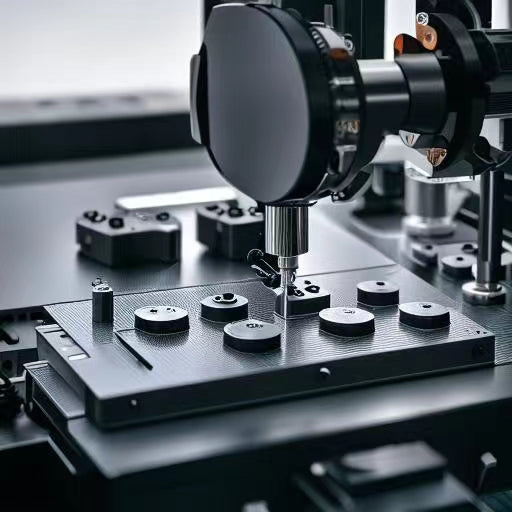
CNC Machining
Where Precision Meets Performance – CNC Mastery.
CNC machining, which stands for Computer Numerical Control machining, is a manufacturing process that utilizes computer-controlled machines to create precise and complex parts and components from various materials such as metal, plastic, wood, and composites. It is a subtractive manufacturing method, meaning it removes material from a workpiece to achieve the desired shape and dimensions.
How Does CNC machining work?
- Design: First, a detailed 3D model or a 2D CAD (Computer-Aided Design) drawing of the part is created using specialized software. This design serves as the blueprint for the CNC machine to follow.
- Programming: The CAD design is translated into a CNC program using CAM (Computer-Aided Manufacturing) software. This program contains instructions that dictate the tool paths, cutting speeds, and other machining parameters.
- Setup: The material to be machined, often in the form of a solid block or sheet, is securely clamped to the CNC machine's worktable. The machine is also equipped with the necessary cutting tools and fixtures.
- Machining: The CNC machine's computer control system reads the CNC program and guides the cutting tools precisely along the programmed toolpaths. This process involves rotating and moving the cutting tools in multiple directions to remove material according to the design specifications.
- Quality Control: Throughout the machining process, operators may perform quality checks to ensure the part's dimensions and tolerances are within the specified limits.
- Finishing: After the primary machining operations are complete, secondary processes like deburring, polishing, or coating may be applied to achieve the desired surface finish and final appearance.
CNC machining is known for its high accuracy, repeatability, and ability to produce complex shapes and intricate details. It is widely used in various industries, including aerospace, automotive, medical, electronics, and more, to manufacture parts and components for a wide range of applications. CNC machines come in various types, such as milling machines, lathes, routers, and multi-axis machining centers, each specialized for specific tasks and materials.
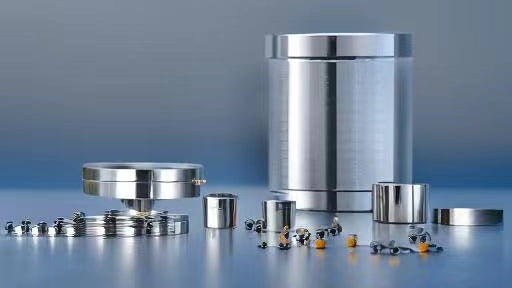
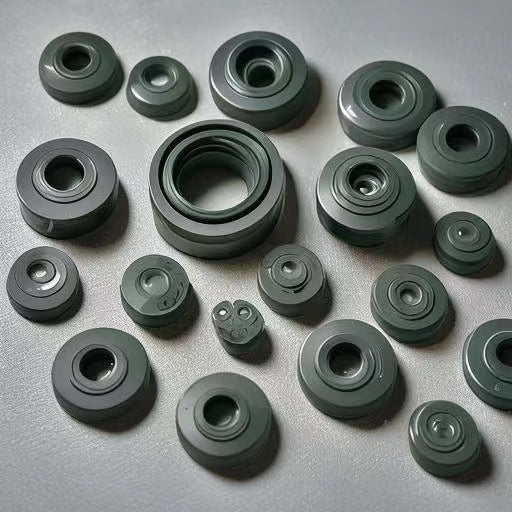
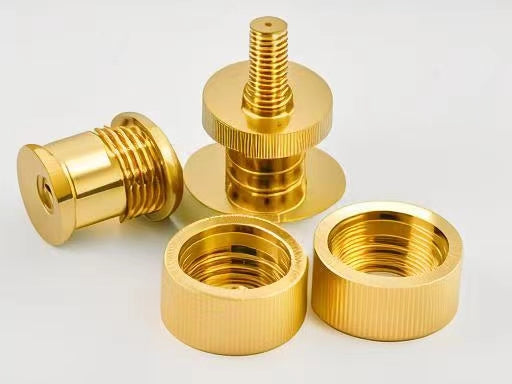
What are the advantages of CNC machining?
- Precision and Accuracy: CNC machines are capable of extremely high levels of precision and accuracy. They can consistently produce parts with tight tolerances, ensuring that each component meets the required specifications.
- Complex Geometries: CNC machining can create parts with intricate shapes and complex geometries that may be difficult or impossible to achieve with other manufacturing methods. This flexibility is especially valuable in industries like aerospace and medical device manufacturing.
- RepeatabilityEnvironmental Benefits: CNC machining produces less waste compared to some other manufacturing processes, as it primarily involves material removal rather than material deformation or casting.: Once a CNC program is created, it can be reused to manufacture identical parts with high repeatability. This is crucial for maintaining consistency in mass production.
- Efficiency: CNC machines can operate continuously, 24/7, without the need for breaks or shifts. This leads to increased productivity and reduced labor costs over time.
- Reduced Human Error: Automation in CNC machining minimizes the risk of human errors that can occur in manual machining. This helps maintain product quality and reduces the likelihood of defects.
- Wide Range of Materials: CNC machining can be used with various materials, including metals, plastics, composites, and wood. This versatility allows manufacturers to choose the best material for the intended application.
- Quick Prototyping: CNC machining can be used for rapid prototyping, allowing designers and engineers to test and iterate their designs quickly before committing to mass production.
- Short Lead Times: CNC machining offers shorter lead times compared to some traditional manufacturing methods. This is particularly important when responding to changing market demands.
- Minimal Tooling Costs: While initial setup and programming costs may be involved, CNC machining often requires less tooling than other manufacturing processes like injection molding or die casting.
- Customization: CNC machining allows for easy customization of parts and components, making it suitable for producing one-off or small-batch orders efficiently.
- Integration with CAD/CAM: CNC machines can directly use CAD/CAM data, streamlining the transition from design to production and reducing the risk of errors during this phase.
- Quality ControlEnvironmental Benefits: CNC machining produces less waste compared to some other manufacturing processes, as it primarily involves material removal rather than material deformation or casting.: CNC machines can be equipped with sensors and measurement tools for in-process quality control, ensuring that parts meet quality standards throughout production.
- Environmental Benefits: CNC machining produces less waste compared to some other manufacturing processes, as it primarily involves material removal rather than material deformation or casting.
Overall, CNC machining offers a combination of precision, efficiency, and versatility that makes it a crucial technology in modern manufacturing, enabling the production of high-quality, complex components for a wide range of industries.
What are the disadvantages of CNC machining?
- High Initial Costs: Setting up a CNC machining operation can be expensive. It requires significant capital investment in CNC machines, tooling, software, and skilled operators. Small businesses and startups may find the upfront costs prohibitive.
- Complex Programming: Creating CNC programs can be complex and time-consuming, especially for intricate or 3D parts. Skilled programmers are needed to generate efficient tool paths and optimize machining processes.
- Material Limitations: While CNC machining can work with a wide range of materials, certain materials, such as some ceramics and very hard alloys, may be challenging or expensive to machine due to tool wear and breakage.
- Tool Wear and Maintenance: Cutting tools in CNC machining wear out over time and require frequent replacement, which adds to operational costs. Routine machine maintenance is also essential to ensure consistent performance.
- Production Speed: Although CNC machines are highly efficient, they may not be as fast as other manufacturing methods for large-scale production. Mass production processes like stamping or injection molding can be quicker for certain types of parts.
- Limited Accessibility: CNC machines have physical size limitations. Extremely large or heavy parts may be difficult or impossible to machine on standard equipment.
- Setup Time: Changing from one job to another (setup time) can be time-consuming. This can be a drawback when there is a need to switch between different parts frequently.
- Lack of Flexibility: Once a CNC program is set up, making design changes can be challenging and time-consuming. This makes CNC machining less suitable for projects that require rapid design iterations.
- Energy Consumption: CNC machines can consume a significant amount of electricity, especially when running continuously. Energy costs can be a concern for some manufacturers.
- Noise and Vibration: CNC machines can produce noise and vibration, which may require noise control measures and can lead to operator fatigue if not properly managed.
- Waste Generation: While CNC machining generates less waste than some other processes, there is still some material waste created during the machining process, especially when roughing out parts.
- Risk of Computer Failures: Since CNC machines are computer-controlled, they are susceptible to computer-related issues such as software glitches, crashes, or hardware failures that can disrupt production.