材質 - 標準 ABS
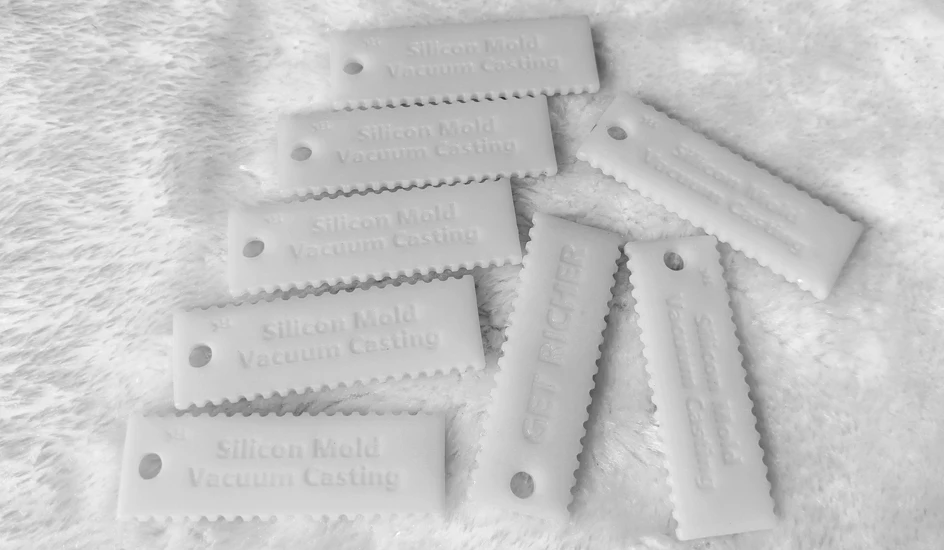
テクノロジー シリコンモールド 真空注型
素材 標準 ABS
オリジナルカラー ホワイト/ブラック/カスタムカラー
熱変形 70-100°C
硬度 83D
表面状況 わずかな射出痕および傷
印刷プラットフォームサイズ 900*650*450mm
曲げ弾性率 2000-2200 Mpa
曲げ強度 80- 100 Mpa
引張強さ 75 ~ 85 MPa
破断点伸び 8 ~ 16 %
ノッチ付き衝撃強度 Izod 12 KJ/m²
公差 製品の局所精度は 0.3 ~ 0.5 mm ~ 5 パーセントですが、全体の精度を制御するのは困難です
ポストプロセス組み立て、銅ナットはめ込み、物理研磨、塗装、電気めっき、シルクスクリーン、水転写印刷、コーティング
肉厚は0.8mm以上必要、大きな部品は3D図面による
シリコンモールド真空鋳造標準ABSの利点は次のとおりです。
1.正確な複製:正確に再現します。 ABS パーツの特性と詳細。
滑らかな仕上げ: 研磨された射出成形のような表面を持つ部品が得られます。
コスト効率: 射出成形などの大量生産方法よりも手頃な価格です。
迅速な生産: 小規模から中規模の生産に迅速に対応します。
5. デザインの多様性: 最終部品の複雑なデザインやアンダーカットが可能です。
優れたプロトタイピング: 量産前のプロトタイピングおよび機能テストに最適です。
7. 少量生産の柔軟性: 少量生産のニーズに適しています。
シリコンモールド真空鋳造標準 ABS の欠点は次のとおりです。
1.限られた材料特性: 最終 ABS 部品の特性は、高級射出成形 ABS の特性と完全には一致しない可能性があります。
2. 大量生産には最適ではありません: 低から中程度の生産量に最適です。大規模な生産ではコスト効率が良くない可能性があります。
3. 型の磨耗: このプロセスで使用されるシリコン型は時間の経過とともに劣化し、鋳造品の品質と寿命に影響を与える可能性があります。
リードタイム: 金型の作成と硬化のリードタイムが含まれ、プロジェクトのタイムラインに影響を与える可能性があります。
耐熱ABS
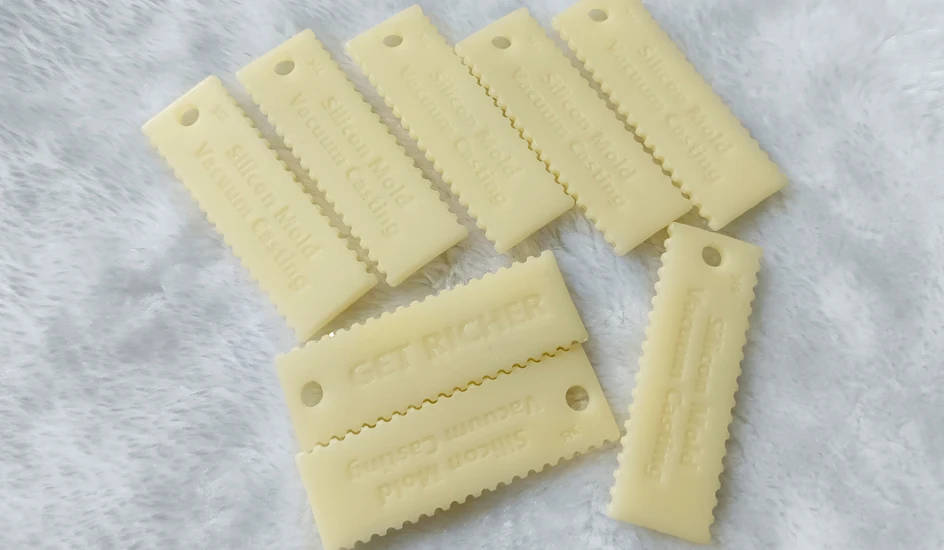
テクノロジー シリコンモールド 真空注型
材料 耐熱性 ABS
オリジナルカラー ホワイト/ブラック/カスタムカラー
熱変形 100-150°C
硬度 80D
表面状態 わずかな射出痕および傷
印刷プラットフォームサイズ 900*650*450mm
曲げ弾性率 2000-2200 Mpa
曲げ強度90-115 MPa
引張強さ 55-60 MPa
破断点伸び 8-16 %
ノッチ付き衝撃強度 Izod 35 KJ/m²
公差 製品の局所精度は 0.3-0.5mm ~ 5 ‰ ですが、全体の精度を制御するのは困難です
。プロセス組立、銅ナットはめ込み、物理研磨、塗装、電気めっき、シルクスクリーン、水転写印刷、コーティング
肉厚は0.8mm以上必要、大きな部品は3D図面による
シリコンモールド真空鋳造耐熱ABSの利点は次のとおりです
。耐熱性: 耐熱 ABS は標準 ABS と比較して高温に耐えることができるため、熱にさらされる環境での用途が拡大します。
耐久性と頑丈さ: 耐熱性 ABS で作られた部品は、高温でも構造の完全性と特性を維持し、耐久性を保証します。
幅広い応用範囲:自動車、航空宇宙、エレクトロニクスなど、熱にさらされることが多いさまざまな業界で必要とされる部品に最適です。
4. 良好な耐薬品性: 耐熱性 ABS は通常、耐薬品性に優れており、さまざまな産業環境への適合性が向上します。
シリコンモールド真空注型耐熱 ABS の欠点は次のとおりです。
1.耐熱性の限界: 耐熱 ABS は標準 ABS よりも高い温度に耐えることができますが、それでも温度限界があり、非常に高い温度では変形したり特性が失われる可能性があります。
材料コスト: 耐熱 ABS は標準 ABS より高価になる可能性があり、真空鋳造プロセスの全体コストが増加します。
複雑な成形プロセス: ABS で耐熱性を実現するには、より複雑な成形プロセスが必要になる場合があり、シリコン型の作成がより難しくなり、より時間がかかります。
4. 金型の磨耗: 高温によりシリコン型の磨耗が加速され、寿命が短くなり、鋳造品の品質に影響を与える可能性があります。
難燃性ABS
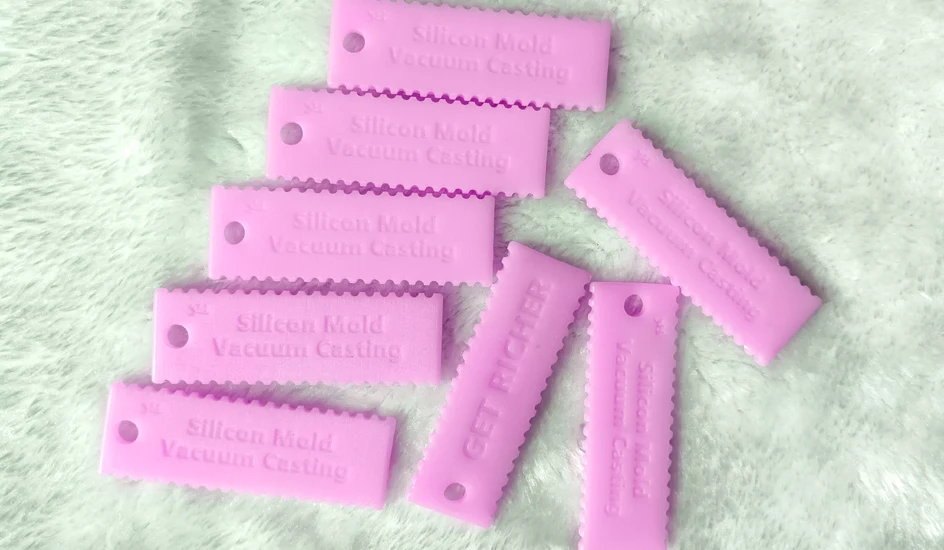
技術 シリコンモールド 真空注型
材料 難燃性 ABS
オリジナルカラー ホワイト/ブラック/カスタムカラー
熱変形 70-80°C
硬度 82D
表面状態 わずかな射出痕および傷
印刷プラットフォームサイズ 900*650*450mm
曲げ弾性率 2100-2300 Mpa
曲げ強度80-90 MPa
引張強さ 60-70 MPa
破断点伸び 8-10 %
ノッチ付き衝撃強度 Izod 15 KJ/m²
公差 製品の局所精度は 0.3-0.5mm ~ 5 ‰ ですが、全体の精度を制御するのは困難です
。プロセス組立、銅ナットはめ込み、物理研磨、塗装、電気めっき、シルクスクリーン、水転写印刷、コーティング
肉厚は0.8mm以上必要、大きな部品は3D図面による
シリコンモールド真空鋳造難燃性ABSの利点は次
のとおりです。安全性: 難燃性 ABS は発火を防止し、炎の広がりを遅らせることで火災の安全性を高めます。
2. 規制への準拠: 自動車産業やエレクトロニクス産業など、防火および規制基準を満たすことが不可欠な用途に最適です。
耐久性と機能性:ABSの耐久性と機能性を維持しつつ、難燃性を備えているため、幅広い用途に適しています。
4.幅広い適用性: 電気エンクロージャ、自動車内装、家庭用電化製品など、火災安全が懸念される環境で役立ちます。
シリコンモールド真空鋳造難燃性 ABS の欠点は次のとおりです。
1.材料の複雑さ: 難燃性 ABS はより複雑な材料であるため、鋳造プロセスがより困難になる可能性があります。
コスト: 難燃性 ABS は標準 ABS よりも高価になる可能性があり、プロジェクト全体のコストが増加します。
材料の選択肢が限られている: 難燃性材料の選択は標準の ABS に比べて限られている可能性があり、プロセスの材料の選択肢が制限されます。
パソコン

技術 シリコンモールド 真空注型
素材 PC
オリジナルカラー 白/黒/半透明/カスタムカラー
熱変形 50-60°C
硬度 80D
表面状況 わずかな射出痕および傷
印刷プラットフォームサイズ 900*650*450mm
曲げ弾性率 1700-1800 Mpa
曲げ強度 80 -90 MPa
引張弾性率 1900-2000 MPa
引張強さ 35-40 MPa
破断点伸び 5-6 %
ノッチ付き衝撃強さ アイゾット 18 KJ/m²
公差 製品の局部精度は 0.3-0.5mm ~ 5 ‰、全体精度は制御が難しい
後工程組立、銅ナットのはめ込み、物理研磨、塗装、電気めっき、シルクスクリーン、水転写印刷、コーティング
肉厚は0.8mm以上必要、大型部品は3D図面による
シリコンモールド真空鋳造PCの利点は
次のとおりです。高い耐衝撃性: PC は入手可能な熱可塑性プラスチックの中で最も耐衝撃性が高く、部品が機械的ストレスや潜在的な衝撃に耐える必要がある用途に適しています。
光学的透明性:PCは優れた光学的透明性と透明性を備えているため、レンズ、カバー、保護シールドなどのシースルーまたは光透過性が必要な部品に最適です。
寸法安定性: PC で製造された部品は温度変化下でも形状と寸法を維持し、安定した性能を保証します。
4.耐薬品性:PCは多くの薬品に対して優れた耐性を持っており、さまざまな物質への曝露が懸念される用途に適しています。
5. 少量生産: シリコーン金型真空鋳造は、特に従来の製造方法では少量生産ではコストが高くなる場合に、少量から中量の PC 部品を生産するのに適しています。
シリコンモールド真空注型 PC の欠点は次のとおりです。
1.リードタイム: 型の作成、硬化、鋳造を含む生産プロセスが完了するまでに数日かかる場合があります。これは、スケジュールが非常に厳しいプロジェクトには適さない可能性があります。
2. 金型の磨耗: シリコーン金型には寿命が限られており、特に PC のような機械的特性の高い樹脂を使用した場合、時間の経過とともに磨耗する可能性があります。大規模な生産では、金型を頻繁に交換する必要がある場合があります。
後処理が必要: 鋳造 PC 部品は、希望の表面仕上げや寸法精度を達成するために、トリミング、サンディング、研磨などの後処理が必要な場合があります。
材料の収縮: PC 樹脂は硬化プロセス中に多少の収縮を経験する可能性があり、寸法の変化を補償するために金型設計の調整が必要になる場合があります。
材料リサイクルの制限: PC を使用したシリコンモールドの真空注型中に発生する余剰材料または廃棄材料は、通常、将来の使用のためにリサイクルできません。
コスト: このプロセスは PC 部品の少量生産では費用対効果が高くなりますが、大規模な生産では射出成形などの従来の製造方法と比較してユニットあたりのコストが高くなる可能性があります。
PP
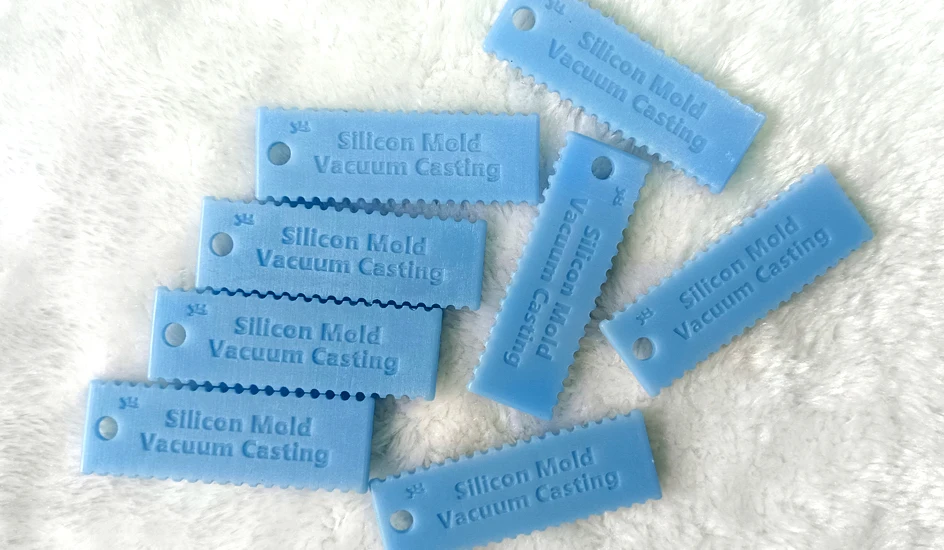
テクノロジー シリコンモールド 真空注型
素材 PP
オリジナルカラー ホワイト/ブラック/カスタムカラー
熱変形 50-60°C
硬度 75-83D
表面状況 わずかな射出痕および傷
印刷プラットフォームサイズ 900*650*450mm
曲げ弾性率 600-1300 Mpa
曲げ強度 20 -50 Mpa
引張強さ 25-35 MPa
破断点伸び 5-6 %
ノッチ付き衝撃強度 Izod 18 KJ/m²
公差 製品の局所精度は 0.3-0.5mm ~ 5 ‰ ですが、全体の精度を
後工程で制御するのは困難です組立、銅ナットはめ込み、物理研磨、塗装、電気めっき、シルクスクリーン、水転写印刷、コーティング
肉厚は0.8mm以上必要、大型部品は3D図面による
シリコンモールド真空鋳造PPの利点は次のとおりです。
1.耐薬品性: PPは多くの化学物質、酸、塩基に対する耐性が高く、部品が腐食性物質にさらされる用途に適しています。
低密度:PPは密度が低いため、軽量です。これは、自動車部品など、軽量化が重要な用途に有利です。
3. 優れた電気絶縁性: PP は優れた電気絶縁体であるため、電気および電子用途に適しています。
柔軟性と靭性:PPは柔軟性と靭性のバランスに優れており、衝撃や疲労に強いです。折り曲げや繰り返しの使用にも耐えます。
5.低吸湿性:PPは低吸湿性を持っており、湿気や湿気への曝露が懸念される用途に有利です。
6. 少量生産: シリコンモールド真空鋳造は、特に従来の製造方法ではコストが非常に高くつく少量生産の PP 部品を少量から中量生産するのに適しています。
シリコンモールド真空注型 PP-ポリプロピレンの欠点は次のとおりです。
1.リードタイム: 型の作成、硬化、注型を含む製造プロセスが完了するまでに数日かかる場合があります。これは、スケジュールが非常に厳しいプロジェクトには適さない可能性があります。
2. 金型の磨耗: シリコーン金型には寿命が限られており、特に PP などの特殊な添加剤や強化材を含む樹脂と一緒に使用した場合、時間の経過とともに磨耗する可能性があります。大規模な生産では、金型を頻繁に交換する必要がある場合があります。
後処理が必要: 鋳造 PP 部品は、所望の外観と寸法精度を達成するために、トリミング、サンディング、表面仕上げなどの後処理が必要な場合があります。
材料の収縮: PP 樹脂は硬化プロセス中に多少の収縮を経験する可能性があり、寸法の変化を補償するために金型設計の調整が必要になる場合があります。
5. 限られた材料リサイクル: シリコンモールドと PP の真空注型中に発生する余剰材料または廃棄材料は、通常、将来の使用のためにリサイクルできません。
6. 限られた温度耐性: PP は熱変形温度が比較的低いため、高温になると変形したり構造的完全性を失ったりする可能性があります。高温用途には適していません。
要約すると、PP を使用したシリコンモールド真空注型には、耐薬品性、低密度、柔軟性という利点があります。ただし、リードタイム、金型の磨耗、後加工の必要性などの制限があります。 PP を使用した 3D プリント プロジェクトでこの方法を選択する場合は、プロジェクトの要件と材料を慎重に検討することが不可欠です。
ナイロン
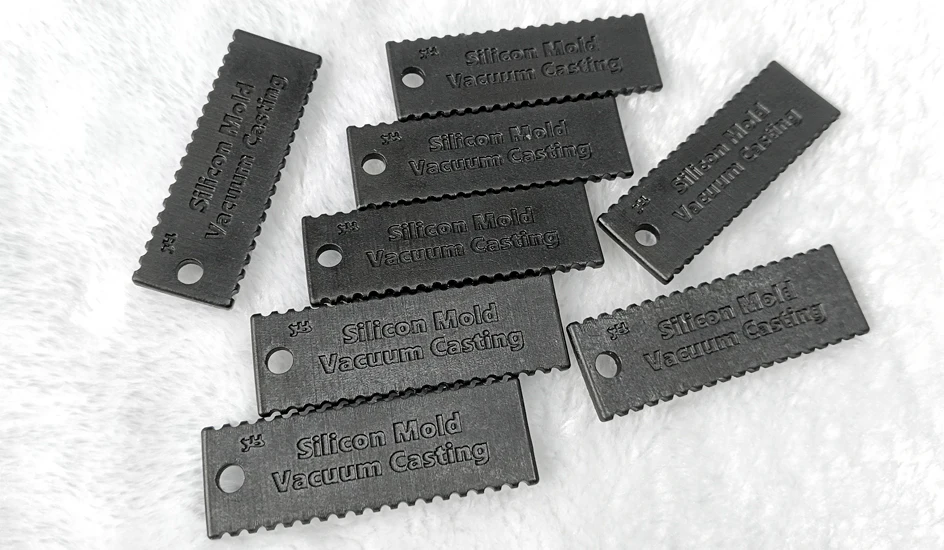
テクノロジー シリコンモールド 真空注型
素材 ナイロン
オリジナルカラー ホワイト/ブラック/カスタムカラー
熱変形 100-120°C
硬度 87D
表面状態 わずかな射出痕および傷
印刷プラットフォームサイズ 900*650*450mm
曲げ弾性率 1800-2000 Mpa
曲げ強度 80-92 Mpa
引張強さ 50-60 MPa
破断点伸び 10-12 %
ノッチ付き衝撃強度 Izod 17 KJ/m²
公差 製品の局所精度は 0.3-0.5mm ~ 5 ‰ ですが、全体の精度を制御するのは困難です
ポストプロセス組み立て、銅ナットはめ込み、物理研磨、塗装、電気めっき、シルクスクリーン、水転写印刷、コーティング
肉厚は0.8mm以上必要、大型部品は3D図面による
シリコンモールド真空鋳造ナイロンの利点は次のとおりです。
1.高い機械的強度: ナイロン部品の製造このプロセスにより、高い引張強度、靭性、耐衝撃性などの優れた機械的特性が得られます。このため、ナイロンは要求の厳しい用途に適しています。
2.耐久性:ナイロンは耐久性と耐摩耗性で知られており、摩擦や磨耗に耐える必要がある部品に最適です。
耐薬品性:ナイロンは多くの薬品、油、溶剤に対して優れた耐性を持っており、さまざまな物質への曝露が懸念される用途に適しています。
低摩擦係数:ナイロンは摩擦係数が低いため、可動部や摺動機構を伴う用途に最適です。
柔軟性: ナイロン部品は、使用されるナイロンの種類に応じて、ある程度の柔軟性を発揮します。そのため、剛性と柔軟性のバランスが必要な用途に適しています。
6. 少量生産: シリコンモールド真空鋳造は、特に従来の製造方法では少量生産ではコストが高くなる場合に、少量から中量のナイロン部品を生産するのに適しています。
シリコンモールド真空注型ガラス繊維ナイロンの欠点は次のとおりです。
1.リードタイム: 型の作成、硬化、注型を含む製造プロセスが完了するまでに数日かかる場合があります。これは、スケジュールが非常に厳しいプロジェクトには適さない可能性があります。
2. 金型の磨耗: シリコーン金型には寿命が限られており、特にナイロンなどの機械的特性の高い樹脂を使用した場合、時間の経過とともに磨耗する可能性があります。大規模な生産では、金型を頻繁に交換する必要がある場合があります。
3. 後処理が必要: 鋳造ナイロン部品は、所望の外観と寸法精度を達成するために、トリミング、サンディング、表面仕上げなどの後処理が必要な場合があります。
材料の収縮: ナイロン樹脂は硬化プロセス中に多少の収縮を経験する可能性があり、寸法の変化を補償するために金型設計の調整が必要になる場合があります。
材料リサイクルの制限: ナイロンを使用したシリコンモールドの真空注型中に発生する余剰材料または廃棄材料は、通常、将来の使用のためにリサイクルできません。
6. 吸湿性: ナイロンは吸湿性があり、時間の経過とともに環境から湿気を吸収する可能性があります。適切に取り扱い、保管しないと、機械的特性に影響を与える可能性があります。
POM
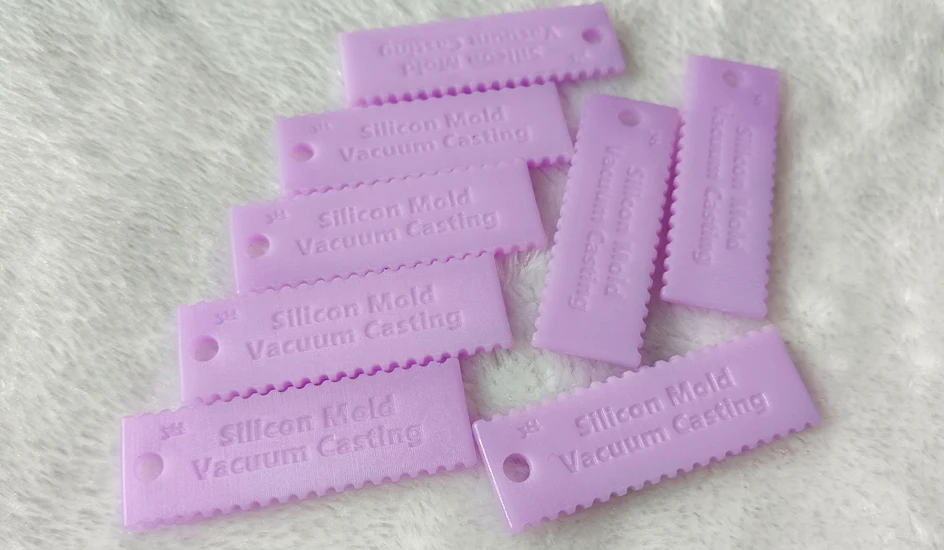
技術 シリコンモールド 真空注型
材料 POM
オリジナルカラー ホワイト/ブラック/カスタムカラー
熱変形 70-80°C
硬度 80D
表面状態 わずかな射出痕および傷
印刷プラットフォームサイズ 900*650*450mm
曲げ弾性率 2400-2500 Mpa
曲げ強度 100-110 Mpa
引張強さ 60-70 MPa
破断点伸び 10-12 %
ノッチ付き衝撃強度 Izod 17 KJ/m²
公差 製品の局所精度は 0.3-0.5mm ~ 5 ‰ ですが、全体の精度を制御するのは困難です
ポストプロセス組み立て、インセット銅ナット、物理研磨、塗装、電気めっき、シルクスクリーン、水転写印刷、コーティング
肉厚は0.8mm以上必要、大型部品は3D図面による
シリコンモールド真空鋳造POMの利点は次のとおりです。
1.優れた機械的特性:POMは優れた特性を示します。高い引張強度、剛性、耐衝撃性などの機械的特性。堅牢で耐久性のあるコンポーネントを必要とするアプリケーションでよく使用されます。
2.低摩擦:POMは摩擦係数が低いため、滑りや回転運動を伴う部品に最適です。これは、摩擦の低減が重要なギア、ベアリング、その他のコンポーネントで一般的に使用されています。
3. 寸法安定性: POM は寸法安定性に優れています。つまり、この材料で作られた部品は、温度変化や機械的ストレス下でも形状とサイズを維持します。
耐薬品性:POMは溶剤、油、燃料など多くの薬品に対して耐性があり、各種物質への暴露が懸念される用途に適しています。
5. 低吸湿性: POM は低吸湿性を備えているため、湿気や湿気にさらされて性能に影響を与える可能性がある用途に有利です。
6. 少量生産: シリコンモールド真空鋳造は、特に従来の製造方法では少量生産ではコストが高くなる場合に、少量から中量の POM 部品を生産するのに適しています。
シリコンモールド真空注型 POM の欠点は次のとおりです。
1.リードタイム: 型の作成、硬化、鋳造を含む製造プロセスが完了するまでに数日かかる場合があります。これは、スケジュールが非常に厳しいプロジェクトには適さない可能性があります。
2. 金型の磨耗: シリコーン金型には寿命が限られており、特に POM のような機械的特性の高い樹脂を使用した場合、時間の経過とともに磨耗する可能性があります。大規模な生産では、金型を頻繁に交換する必要がある場合があります。
後処理が必要: 鋳造 POM 部品は、所望の外観と寸法精度を達成するために、トリミング、サンディング、表面仕上げなどの後処理が必要な場合があります。
材料収縮: POM 樹脂は硬化プロセス中に多少の収縮を経験する可能性があり、寸法変化を補償するために金型設計の調整が必要になる場合があります。
限定された材料リサイクル: POM を使用したシリコンモールドの真空鋳造中に発生する余剰材料または廃棄材料は、通常、将来の使用のためにリサイクルできません。
コスト: このプロセスは POM 部品の少量生産では費用対効果が高くなりますが、大規模な生産では射出成形などの従来の製造方法と比較してユニットあたりのコストが高くなる可能性があります。
要約すると、POM を使用したシリコンモールド真空注型には、優れた機械的特性、低摩擦、耐薬品性という利点があります。ただし、リードタイム、金型の磨耗、後加工の必要性などの制限があります。 POM を使用した 3D プリント プロジェクトでこの方法を選択する場合は、プロジェクトの要件と材料を慎重に検討することが不可欠です。
ケイ素


技術 シリコン型 真空注型
素材 シリコン
オリジナルカラー ホワイト/ブラック/カスタムカラー
熱変形 50-70°C
表面状況 わずかな射出痕と傷
印刷プラットフォーム サイズ 900*650*450mm
公差 製品の局所精度は 0.3-0.5mm です。 ~5 パーセント、ただし全体の精度は制御が難しい
硬度: ショア 30A、40A、50A、60A、70A、80A、90A
肉厚は 0.8mm 以上必要、大きな部品は 3D 図面による
シリコンの利点は次のとおりです。
1. エラストマー特性:シリコーンゴムは、柔軟性と弾力性などの優れたエラストマー特性を示します。柔らかく、柔軟性があり、変形後に元の形状に戻ることが必要な部品の製造に最適です。
耐薬品性:シリコーンは多くの薬品、油、溶剤に対して耐性があり、さまざまな物質への曝露が懸念される用途に適しています。
3. 少量生産: シリコーン金型真空鋳造は、特に従来の製造方法では少量生産ではコストが高くなる場合に、少量から中量の柔軟なシリコーン部品を生産するのに適しています。
4. カスタマイズ: シリコーン材料は、着色、着色、またはブレンドして、さまざまな色を実現したり、特定の美的要件を満たすことができます。
シリコンの欠点は次のとおりです。
1.リードタイム: 型の作成、硬化、鋳造などの製造プロセスが完了するまでに数日かかる場合があります。これは、スケジュールが非常に厳しいプロジェクトには適さない可能性があります。
2. 金型の磨耗: シリコーン金型には寿命が限られており、特に特別な添加剤や強化材を含む樹脂と一緒に使用した場合、時間の経過とともに磨耗する可能性があります。大規模な生産では、金型を頻繁に交換する必要がある場合があります。
3. 後処理が必要: 鋳造シリコン部品は、所望の外観と寸法精度を達成するために、トリミング、サンディング、表面仕上げなどの後処理が必要な場合があります。
材料の収縮: シリコーン樹脂は硬化プロセス中に多少の収縮を経験する可能性があり、寸法の変化を補償するために金型設計の調整が必要になる場合があります。
コスト: このプロセスは、柔軟なシリコーン部品の少量生産では費用対効果が高くなりますが、大規模な生産では射出成形などの従来の製造方法と比較してユニットあたりのコストが高くなる可能性があります。