Materiales: ABS estándar
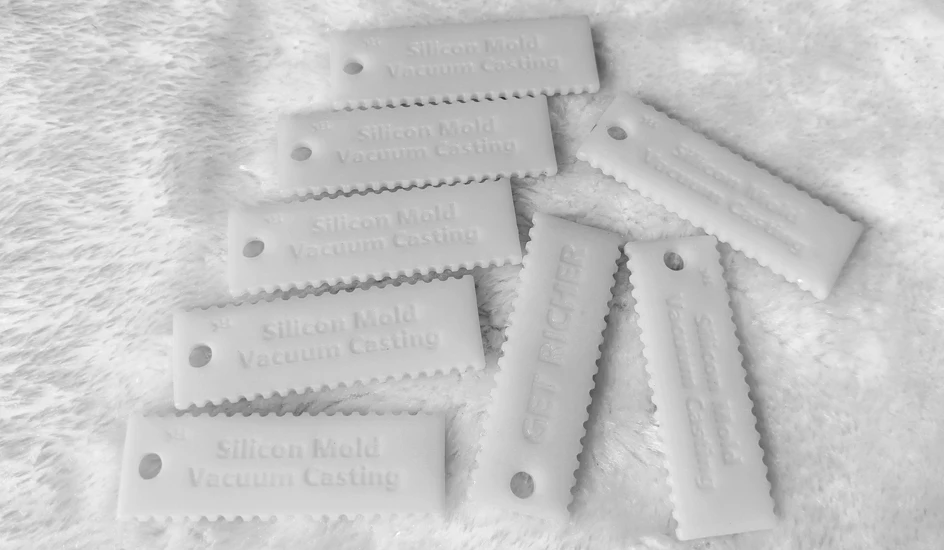
Tecnología de fundición al vacío con moldes de silicio
Material ABS estándar
Color original Blanco/Negro/Color personalizado
Deformación térmica 70-100°C
Dureza 83D
Situación de la superficie Ligeras marcas de inyección y rayones
Tamaño de la plataforma de impresión 900*650*450 mm
Módulo de flexión 2000-2200 Mpa
Resistencia a la flexión 80-100 Mpa
Resistencia a la tracción 75-85 MPa
Elongación de rotura 8-16 %
Resistencia al impacto con muescas Izod 12 KJ/m²
Tolerancia La precisión local del producto está entre 0,3-0,5 mm ~ 5 ‰, mientras que la precisión general es difícil de controlar
Montaje posterior al proceso, tuercas de cobre insertadas, pulido físico, pintura, galvanoplastia, serigrafía, impresión por transferencia de agua, revestimiento
El espesor de pared requerido es superior a 0,8 mm, piezas grandes según dibujos 3D
Las ventajas del ABS estándar de fundición al vacío con molde de silicio son:
1. Replicación precisa: reproduce con precisión las propiedades y detalles de las piezas de ABS.
2. Acabados lisos: da como resultado piezas con una superficie pulida similar a la del moldeo por inyección.
3. Rentabilidad: más asequible que los métodos de gran volumen como el moldeo por inyección.
4.Producción rápida: respuesta rápida para tiradas de producción pequeñas y medianas.
5. Versatilidad del diseño: permite diseños complejos y socavados en las piezas finales.
6. Excelencia en la creación de prototipos: ideal para la creación de prototipos y pruebas funcionales antes de la producción en masa.
7.Flexibilidad de bajo volumen: Adecuado para necesidades de producción de lotes pequeños.
Las desventajas del ABS estándar de fundición al vacío con molde de silicona son:
1. Propiedades limitadas del material: Es posible que las propiedades de las piezas finales de ABS no coincidan perfectamente con las del ABS moldeado por inyección de alta calidad.
2.No es ideal para volúmenes altos: es más adecuado para volúmenes de producción bajos a medianos; puede no ser rentable para la producción a gran escala.
3. Desgaste del molde: Los moldes de silicona utilizados en este proceso pueden degradarse con el tiempo, afectando la calidad y longevidad de los moldes.
4. Plazo de entrega: Implica el tiempo de entrega para la creación y el curado del molde, lo que puede afectar los cronogramas del proyecto.
ABS resistente a la temperatura
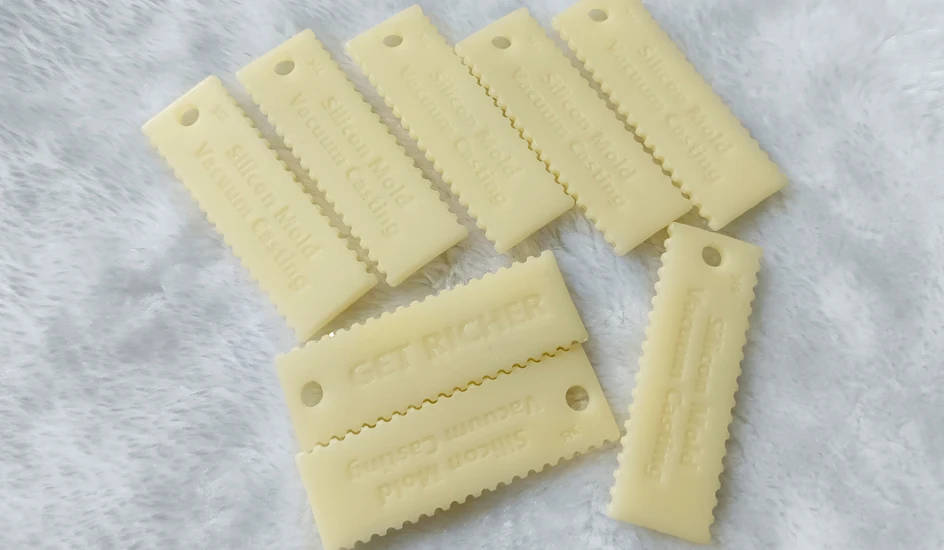
Tecnología de fundición al vacío con moldes de silicio
Material ABS resistente a la temperatura
Color original Blanco/Negro/Color personalizado
Deformación térmica 100-150°C
Dureza 80D
Situación de la superficie Ligeras marcas de inyección y rayones
Tamaño de la plataforma de impresión 900*650*450 mm
Módulo de flexión 2000-2200 Mpa
Resistencia a la flexión 90-115 Mpa
Resistencia a la tracción 55-60 MPa
Elongación de rotura 8-16 %
Resistencia al impacto con muescas Izod 35 KJ/m²
Tolerancia La precisión local del producto está entre 0,3-0,5 mm ~ 5 ‰, mientras que la precisión general es difícil de controlar
Montaje posterior al proceso, tuercas de cobre insertadas, pulido físico, pintura, galvanoplastia, serigrafía, impresión por transferencia de agua, revestimiento
El espesor de pared requerido es superior a 0,8 mm, piezas grandes según dibujos 3D
Las ventajas del ABS resistente a la temperatura de fundición al vacío con molde de silicio son:
1.Resistencia al calor mejorada: el ABS resistente a la temperatura puede soportar temperaturas más altas en comparación con el ABS estándar, ampliando sus aplicaciones en entornos expuestos al calor.
2.Duradero y resistente: las piezas fabricadas con ABS resistente a la temperatura mantienen su integridad estructural y sus propiedades incluso a temperaturas elevadas, lo que garantiza su durabilidad.
3.Amplia gama de aplicaciones: Ideal para piezas necesarias en diversas industrias, como la automotriz, aeroespacial y electrónica, donde la exposición al calor es común.
4.Buena resistencia química: El ABS resistente a la temperatura normalmente posee buena resistencia a los productos químicos, lo que mejora su idoneidad para diversos entornos industriales.
Las desventajas del ABS resistente a la temperatura de fundición al vacío con molde de silicio son:
1. Resistencia al calor limitada: si bien el ABS resistente a la temperatura puede soportar temperaturas más altas que el ABS estándar, aún tiene límites de temperatura y puede deformarse o perder propiedades a temperaturas muy altas.
2. Costo del material: El ABS resistente a la temperatura puede ser más costoso que el ABS estándar, lo que aumenta el costo general del proceso de fundición al vacío.
3. Proceso de moldeo complejo: Lograr resistencia a la temperatura en ABS puede requerir un proceso de moldeo más complejo, lo que hace que crear el molde de silicona sea más difícil y lleve más tiempo.
4.Desgaste del molde: Las temperaturas más altas involucradas pueden acelerar el desgaste del molde de silicona, reduciendo su vida útil y afectando la calidad de los moldes.
ABS retardante de llama
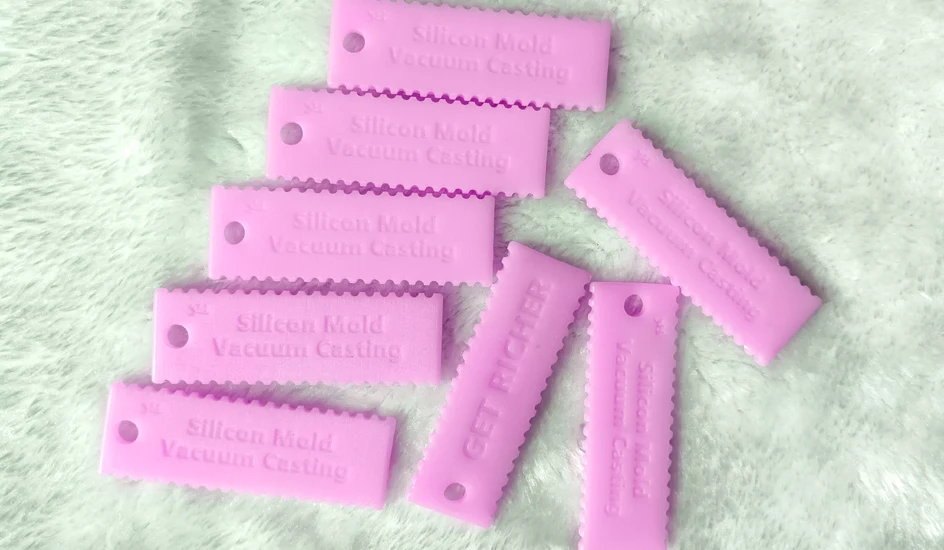
Tecnología de fundición al vacío con moldes de silicio
Material ABS ignífugo
Color original Blanco/Negro/Color personalizado
Deformación térmica 70-80°C
Dureza 82D
Situación de la superficie Ligeras marcas de inyección y rayones
Tamaño de la plataforma de impresión 900*650*450 mm
Módulo de flexión 2100-2300 Mpa
Resistencia a la flexión 80-90 Mpa
Resistencia a la tracción 60-70 MPa
Elongación de rotura 8-10 %
Resistencia al impacto con muescas Izod 15 KJ/m²
Tolerancia La precisión local del producto está entre 0,3-0,5 mm ~ 5 ‰, mientras que la precisión general es difícil de controlar
Montaje posterior al proceso, tuercas de cobre insertadas, pulido físico, pintura, galvanoplastia, serigrafía, impresión por transferencia de agua, revestimiento
El espesor de pared requerido es superior a 0,8 mm, piezas grandes según dibujos 3D
Las ventajas del ABS ignífugo de fundición al vacío con molde de silicio son:
1. Seguridad mejorada: El ABS ignífugo proporciona una mayor seguridad contra incendios al resistir la ignición y ralentizar la propagación de las llamas.
2.Cumplimiento de las regulaciones: Ideal para aplicaciones donde es esencial cumplir con los estándares regulatorios y de seguridad contra incendios, como en las industrias automotriz y electrónica.
3.Duradero y funcional: Mantiene la durabilidad y funcionalidad del ABS al tiempo que incorpora propiedades retardantes de llama, lo que lo hace adecuado para una amplia gama de aplicaciones.
4.Amplia aplicabilidad: útil en entornos donde la seguridad contra incendios es una preocupación, incluidos gabinetes eléctricos, interiores de automóviles y electrónica de consumo.
Las desventajas del ABS ignífugo de fundición al vacío con molde de silicio son:
1. Complejidad del material: El ABS ignífugo es un material más complejo, lo que hace que el proceso de fundición sea potencialmente más desafiante.
2. Costo: El ABS retardante de llama puede ser más costoso que el ABS estándar, lo que aumenta los costos generales del proyecto.
3. Opciones de materiales limitadas: la elección de materiales retardantes de llama puede ser limitada en comparación con el ABS estándar, lo que restringe las opciones de materiales para el proceso.
ordenador personal

Tecnología de fundición al vacío con moldes de silicio
Materiales ordenador personal
Color original Blanco/Negro/Translúcido/Color personalizado
Deformación térmica 50-60°C
Dureza 80D
Situación de la superficie Ligeras marcas de inyección y rayones
Tamaño de la plataforma de impresión 900*650*450 mm
Módulo de flexión 1700-1800 Mpa
Resistencia a la flexión 80-90 Mpa
Módulo de tracción 1900-2000 MPa
Resistencia a la tracción 35-40 MPa
Elongación de rotura 5-6 %
Resistencia al impacto con muescas Izod 18 KJ/m²
Tolerancia La precisión local del producto está entre 0,3-0,5 mm ~ 5 ‰, mientras que la precisión general es difícil de controlar
Montaje posterior al proceso, tuercas de cobre insertadas, pulido físico, pintura, galvanoplastia, serigrafía, impresión por transferencia de agua, revestimiento
El espesor de pared requerido es superior a 0,8 mm, piezas grandes según dibujos 3D
Las ventajas de la PC de fundición al vacío con molde de silicio son:
1. Alta resistencia al impacto: la PC es uno de los termoplásticos más resistentes a los impactos disponibles, lo que lo hace adecuado para aplicaciones donde las piezas deben resistir tensiones mecánicas y posibles impactos.
2.Claridad óptica: la PC ofrece una excelente claridad óptica y transparencia, lo que la hace ideal para piezas que requieren propiedades transparentes o de transmisión de luz, como lentes, cubiertas y escudos protectores.
3. Estabilidad dimensional: las piezas producidas con PC mantienen su forma y dimensiones incluso bajo fluctuaciones de temperatura, lo que garantiza un rendimiento constante.
4.Resistencia química: la PC tiene buena resistencia a muchos químicos, lo que la hace adecuada para aplicaciones donde la exposición a diversas sustancias es una preocupación.
5. Producción de bajo volumen: la fundición al vacío con moldes de silicona es adecuada para producir cantidades pequeñas y medianas de piezas de PC, especialmente cuando los métodos de fabricación tradicionales tendrían un costo prohibitivo para tiradas de bajo volumen.
Las desventajas de la PC de fundición al vacío con molde de silicio son:
1. Plazo de entrega: El proceso de producción, incluida la creación del molde, el curado y la fundición, puede tardar varios días en completarse. Es posible que esto no sea adecuado para proyectos con plazos extremadamente ajustados.
2.Desgaste del molde: Los moldes de silicona tienen una vida útil limitada y pueden desgastarse con el tiempo, especialmente cuando se usan con resinas que tienen altas propiedades mecánicas como la PC. Puede ser necesario reemplazar el molde con frecuencia para grandes tiradas de producción.
3. Se requiere posprocesamiento: las piezas fundidas de PC pueden requerir un posprocesamiento, como recortar, lijar o pulir, para lograr el acabado superficial y la precisión dimensional deseados.
4. Contracción del material: la resina de PC puede experimentar cierta contracción durante el proceso de curado, lo que puede requerir ajustes en el diseño del molde para compensar los cambios dimensionales.
5. Reciclaje limitado de materiales: el exceso o el material de desecho generado durante la fundición al vacío de moldes de silicona con PC generalmente no es reciclable para uso futuro.
6. Costo: si bien este proceso puede ser rentable para la producción de bajo volumen de piezas de PC, puede tener costos por unidad más altos en comparación con los métodos de fabricación tradicionales, como el moldeo por inyección, para tiradas de producción más grandes.
PÁGINAS
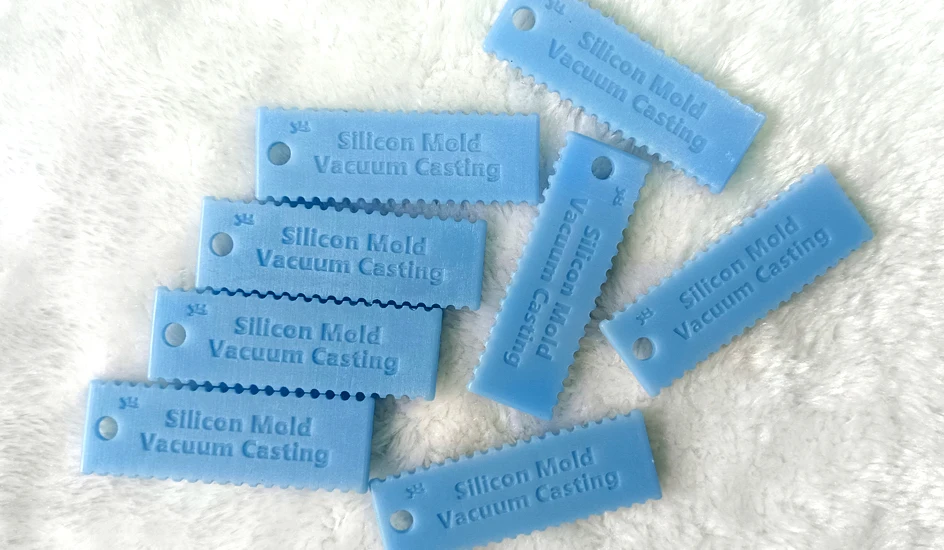
Tecnología de fundición al vacío con moldes de silicio
Material PP
Color original Blanco/Negro/Color personalizado
Deformación térmica 50-60°C
Dureza 75-83D
Situación de la superficie Ligeras marcas de inyección y rayones
Tamaño de la plataforma de impresión 900*650*450 mm
Módulo de flexión 600-1300 Mpa
Resistencia a la flexión 20-50 Mpa
Resistencia a la tracción 25-35 MPa
Elongación de rotura 5-6 %
Resistencia al impacto con muescas Izod 18 KJ/m²
Tolerancia La precisión local del producto está entre 0,3-0,5 mm ~ 5 ‰, mientras que la precisión general es difícil de controlar
Montaje posterior al proceso, tuercas de cobre insertadas, pulido físico, pintura, galvanoplastia, serigrafía, impresión por transferencia de agua, revestimiento
El espesor de pared requerido es superior a 0,8 mm, piezas grandes según dibujos 3D
Las ventajas del PP de fundición al vacío con molde de silicio son:
1.Resistencia química: El PP es altamente resistente a muchos químicos, ácidos y bases, lo que lo hace adecuado para aplicaciones donde las piezas están expuestas a sustancias corrosivas.
2.Baja densidad: el PP tiene una baja densidad, lo que significa que es liviano. Esto resulta ventajoso para aplicaciones en las que la reducción de peso es importante, como los componentes de automoción.
3.Buen aislamiento eléctrico: el PP es un buen aislante eléctrico, lo que lo hace adecuado para aplicaciones eléctricas y electrónicas.
4.Flexibilidad y dureza: el PP tiene un buen equilibrio entre flexibilidad y dureza, lo que lo hace resistente al impacto y la fatiga. Puede soportar la flexión y el uso repetido.
5.Baja absorción de humedad: el PP tiene propiedades de baja absorción de humedad, lo cual es ventajoso en aplicaciones donde la exposición a la humedad es una preocupación.
6. Producción de bajo volumen: la fundición al vacío con moldes de silicona es adecuada para producir cantidades pequeñas y medianas de piezas de PP, especialmente cuando los métodos de fabricación tradicionales tendrían un costo prohibitivo para tiradas de bajo volumen.
Las desventajas del PP-Polipropileno de fundición al vacío con molde de silicio son:
1. Plazo de entrega: El proceso de producción, incluida la creación del molde, el curado y la fundición, puede tardar varios días en completarse. Es posible que esto no sea adecuado para proyectos con plazos extremadamente ajustados.
2.Desgaste del molde: Los moldes de silicona tienen una vida útil limitada y pueden desgastarse con el tiempo, especialmente cuando se usan con resinas que tienen aditivos o refuerzos especiales como el PP. Puede ser necesario reemplazar el molde con frecuencia para grandes tiradas de producción.
3.Se requiere posprocesamiento: las piezas fundidas de PP pueden requerir un posprocesamiento, como recorte, lijado o acabado de superficies, para lograr la apariencia y precisión dimensional deseadas.
4. Contracción del material: la resina de PP puede experimentar cierta contracción durante el proceso de curado, lo que puede requerir ajustes en el diseño del molde para compensar los cambios dimensionales.
5. Reciclaje limitado de material: el exceso o el material de desecho generado durante la fundición al vacío de moldes de silicona con PP generalmente no es reciclable para uso futuro.
6. Resistencia a la temperatura limitada: El PP tiene una temperatura de distorsión por calor relativamente baja, lo que significa que puede deformarse o perder integridad estructural a temperaturas elevadas. No es adecuado para aplicaciones de alta temperatura.
En resumen, la fundición al vacío con moldes de silicona con PP ofrece las ventajas de resistencia química, baja densidad y flexibilidad. Sin embargo, tiene limitaciones como el tiempo de entrega, el desgaste del molde y la necesidad de posprocesamiento. Es esencial considerar cuidadosamente los requisitos y materiales del proyecto al elegir este método para proyectos de impresión 3D que utilizan PP.
Nylon
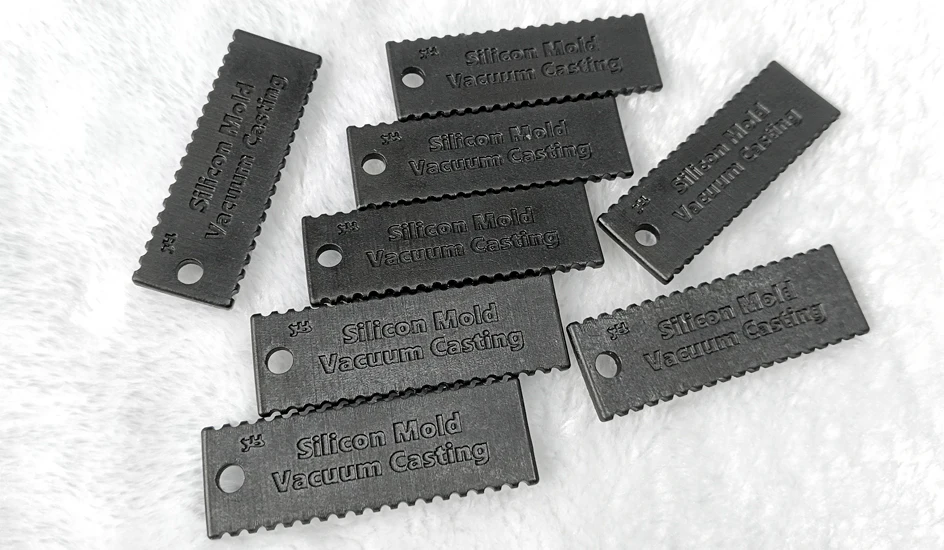
Tecnología de fundición al vacío con moldes de silicio
Material nailon
Color original Blanco/Negro/Color personalizado
Deformación térmica 100-120°C
Dureza 87D
Situación de la superficie Ligeras marcas de inyección y rayones
Tamaño de la plataforma de impresión 900*650*450 mm
Módulo de flexión 1800-2000 Mpa
Resistencia a la flexión 80-92 Mpa
Resistencia a la tracción 50-60 MPa
Elongación de rotura 10-12 %
Resistencia al impacto con muescas Izod 17 KJ/m²
Tolerancia La precisión local del producto está entre 0,3-0,5 mm ~ 5 ‰, mientras que la precisión general es difícil de controlar
Montaje posterior al proceso, tuercas de cobre insertadas, pulido físico, pintura, galvanoplastia, serigrafía, impresión por transferencia de agua, revestimiento
El espesor de pared requerido es superior a 0,8 mm, piezas grandes según dibujos 3D
Las ventajas del nailon de fundición al vacío con molde de silicio son:
1. Alta resistencia mecánica: las piezas de nailon producidas mediante este proceso exhiben excelentes propiedades mecánicas, que incluyen alta resistencia a la tracción, tenacidad y resistencia al impacto. Esto hace que el nailon sea adecuado para aplicaciones exigentes.
2.Durabilidad: El nailon es conocido por su durabilidad y resistencia al desgaste, lo que lo hace ideal para componentes que necesitan resistir la fricción y la abrasión.
3.Resistencia química: el nailon tiene buena resistencia a muchos productos químicos, aceites y disolventes, lo que lo hace adecuado para aplicaciones donde la exposición a diversas sustancias es una preocupación.
4.Bajo coeficiente de fricción: el nailon tiene un bajo coeficiente de fricción, lo que lo hace ideal para aplicaciones que involucran piezas móviles o mecanismos deslizantes.
5.Flexibilidad: Las piezas de nailon pueden presentar cierto grado de flexibilidad, dependiendo del tipo específico de nailon utilizado. Esto lo hace adecuado para aplicaciones que requieren un equilibrio entre rigidez y flexibilidad.
6. Producción de bajo volumen: la fundición al vacío con moldes de silicona es adecuada para producir cantidades pequeñas y medianas de piezas de nailon, especialmente cuando los métodos de fabricación tradicionales tendrían un costo prohibitivo para tiradas de bajo volumen.
Las desventajas del nailon de fibra de vidrio de fundición al vacío con molde de silicio son:
1. Plazo de entrega: El proceso de producción, incluida la creación del molde, el curado y la fundición, puede tardar varios días en completarse. Es posible que esto no sea adecuado para proyectos con plazos extremadamente ajustados.
2.Desgaste del molde: Los moldes de silicona tienen una vida útil limitada y pueden desgastarse con el tiempo, especialmente cuando se usan con resinas que tienen altas propiedades mecánicas como el nailon. Puede ser necesario reemplazar el molde con frecuencia para grandes tiradas de producción.
3. Se requiere posprocesamiento: las piezas de nailon fundido pueden requerir un posprocesamiento, como recorte, lijado o acabado de superficies, para lograr la apariencia y precisión dimensional deseadas.
4. Contracción del material: La resina de nailon puede experimentar cierta contracción durante el proceso de curado, lo que puede requerir ajustes en el diseño del molde para compensar los cambios dimensionales.
5. Reciclaje limitado de materiales: el exceso o el material de desecho generado durante la fundición al vacío de moldes de silicona con nailon generalmente no es reciclable para uso futuro.
6. Naturaleza higroscópica: el nailon es higroscópico, lo que significa que puede absorber la humedad del medio ambiente con el tiempo. Esto puede afectar sus propiedades mecánicas si no se manipula y almacena adecuadamente.
POM
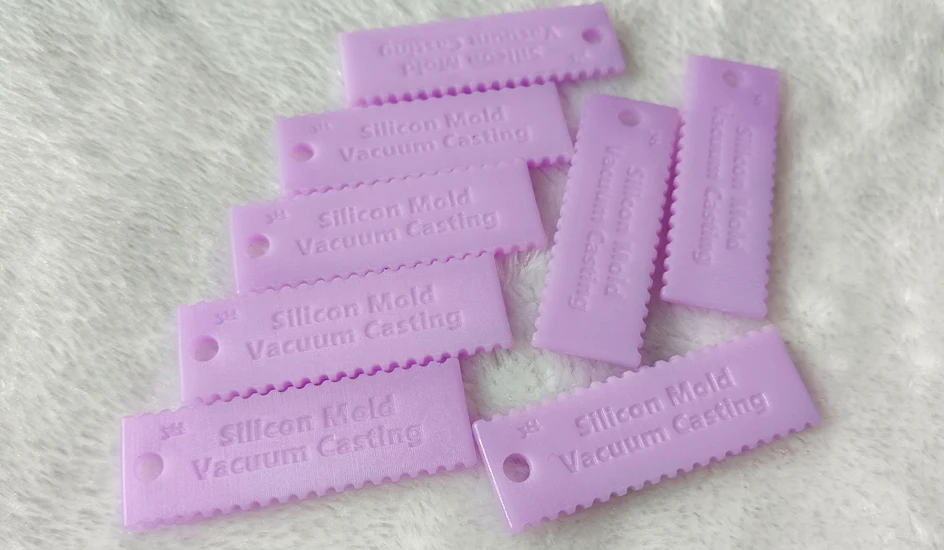
Tecnología de fundición al vacío con moldes de silicio
MaterialPOM
Color original Blanco/Negro/Color personalizado
Deformación térmica 70-80°C
Dureza 80D
Situación de la superficie Ligeras marcas de inyección y rayones
Tamaño de la plataforma de impresión 900*650*450 mm
Módulo de flexión 2400-2500 Mpa
Resistencia a la flexión 100-110 Mpa
Resistencia a la tracción 60-70 MPa
Elongación de rotura 10-12 %
Resistencia al impacto con muescas Izod 17 KJ/m²
Tolerancia La precisión local del producto está entre 0,3-0,5 mm ~ 5 ‰, mientras que la precisión general es difícil de controlar
Montaje posterior al proceso, tuercas de cobre insertadas, pulido físico, pintura, galvanoplastia, serigrafía, impresión por transferencia de agua, revestimiento
El espesor de pared requerido es superior a 0,8 mm, piezas grandes según dibujos 3D
Las ventajas del POM de fundición al vacío con molde de silicio son:
1. Excelentes propiedades mecánicas: POM exhibe excelentes propiedades mecánicas, que incluyen alta resistencia a la tracción, rigidez y resistencia al impacto. A menudo se utiliza en aplicaciones que requieren componentes robustos y duraderos.
2.Baja fricción: POM tiene un bajo coeficiente de fricción, lo que lo hace ideal para piezas que involucran movimientos deslizantes o giratorios. Se usa comúnmente en engranajes, cojinetes y otros componentes donde la reducción de la fricción es crucial.
3. Estabilidad dimensional: POM tiene una excelente estabilidad dimensional, lo que significa que las piezas fabricadas con este material mantienen su forma y tamaño incluso bajo variaciones de temperatura y tensión mecánica.
4.Resistencia química: POM es resistente a muchos productos químicos, incluidos solventes, aceites y combustibles, lo que lo hace adecuado para aplicaciones donde la exposición a diversas sustancias es una preocupación.
5.Baja absorción de humedad: POM tiene propiedades de baja absorción de humedad, lo cual es ventajoso en aplicaciones donde la exposición a la humedad puede afectar el rendimiento.
6. Producción de bajo volumen: la fundición al vacío con moldes de silicona es adecuada para producir cantidades pequeñas y medianas de piezas de POM, especialmente cuando los métodos de fabricación tradicionales tendrían un costo prohibitivo para tiradas de bajo volumen.
Las desventajas del POM de fundición al vacío con molde de silicio son:
1. Plazo de entrega: El proceso de producción, incluida la creación del molde, el curado y la fundición, puede tardar varios días en completarse. Es posible que esto no sea adecuado para proyectos con plazos extremadamente ajustados.
2.Desgaste del molde: Los moldes de silicona tienen una vida útil limitada y pueden desgastarse con el tiempo, especialmente cuando se usan con resinas que tienen altas propiedades mecánicas como POM. Puede ser necesario reemplazar el molde con frecuencia para grandes tiradas de producción.
3. Se requiere posprocesamiento: las piezas fundidas de POM pueden requerir un posprocesamiento, como recorte, lijado o acabado de superficies, para lograr la apariencia y precisión dimensional deseadas.
4. Contracción del material: la resina POM puede experimentar cierta contracción durante el proceso de curado, lo que puede requerir ajustes en el diseño del molde para compensar los cambios dimensionales.
5. Reciclaje limitado de material: el exceso o el material de desecho generado durante la fundición al vacío de moldes de silicona con POM generalmente no es reciclable para uso futuro.
6. Costo: si bien este proceso puede ser rentable para la producción de bajo volumen de piezas de POM, puede tener costos unitarios más altos en comparación con los métodos de fabricación tradicionales, como el moldeo por inyección, para tiradas de producción más grandes.
En resumen, la fundición al vacío con moldes de silicona con POM ofrece las ventajas de excelentes propiedades mecánicas, baja fricción y resistencia química. Sin embargo, tiene limitaciones como el tiempo de entrega, el desgaste del molde y la necesidad de posprocesamiento. Es esencial considerar cuidadosamente los requisitos y materiales del proyecto al elegir este método para proyectos de impresión 3D que utilizan POM.
Silicio


Tecnología de fundición al vacío con moldes de silicio
Material Silicio
Color original Blanco/Negro/Color personalizado
Deformación térmica 50-70°C
Situación de la superficie Ligeras marcas de inyección y rayones
Tamaño de la plataforma de impresión 900*650*450 mm
Tolerancia La precisión local del producto está entre 0,3-0,5 mm ~ 5 ‰, mientras que la precisión general es difícil de controlar
Dureza: Costa 30A, 40A, 50A, 60A, 70A, 80A, 90A
El espesor de pared requerido es superior a 0,8 mm, piezas grandes según dibujos 3D
Las ventajas del Silicio son:
1. Propiedades elastoméricas: el caucho de silicona exhibe excelentes propiedades elastoméricas, incluidas flexibilidad y resistencia. Es ideal para producir piezas que deben ser suaves, flexibles y capaces de volver a su forma original después de la deformación.
2.Resistencia química: la silicona es resistente a muchos productos químicos, aceites y solventes, lo que la hace adecuada para aplicaciones donde la exposición a diversas sustancias es una preocupación.
3. Producción de bajo volumen: la fundición al vacío con moldes de silicona es adecuada para producir cantidades pequeñas a medianas de piezas de silicona flexibles, especialmente cuando los métodos de fabricación tradicionales tendrían un costo prohibitivo para tiradas de bajo volumen.
4.Personalización: Los materiales de silicona se pueden teñir, pigmentar o mezclar para lograr diferentes colores o cumplir con requisitos estéticos específicos.
Las desventajas del silicio son:
1. Plazo de entrega: El proceso de producción, incluida la creación del molde, el curado y la fundición, puede tardar varios días en completarse. Es posible que esto no sea adecuado para proyectos con plazos extremadamente ajustados.
2.Desgaste del molde: Los moldes de silicona tienen una vida útil limitada y pueden desgastarse con el tiempo, especialmente cuando se usan con resinas que tienen aditivos o refuerzos especiales. Puede ser necesario reemplazar el molde con frecuencia para grandes tiradas de producción.
3. Se requiere posprocesamiento: las piezas de silicona fundida pueden requerir un posprocesamiento, como recorte, lijado o acabado de superficies, para lograr la apariencia y precisión dimensional deseadas.
4. Contracción del material: La resina de silicona puede experimentar cierta contracción durante el proceso de curado, lo que puede requerir ajustes en el diseño del molde para compensar los cambios dimensionales.
5. Costo: si bien este proceso puede ser rentable para la producción de bajo volumen de piezas de silicona flexibles, puede tener costos unitarios más altos en comparación con los métodos de fabricación tradicionales, como el moldeo por inyección, para tiradas de producción más grandes.