Malzemeler - Standart ABS
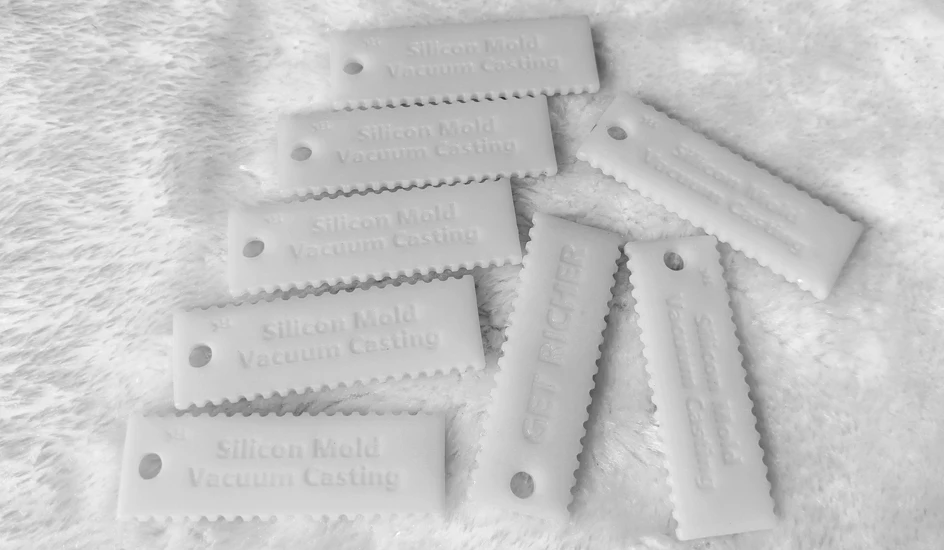
Teknoloji Silikon Kalıp Vakum Döküm
Malzemesi Standart ABS
Orijinal Renk Beyaz/Siyah/Özel Renk
Termal Deformasyon 70-100°C
Sertlik 83D
Yüzey Durumu Hafif Enjeksiyon İzleri ve Çizikler
Baskı Platformu Boyutu 900*650*450mm
Eğilme modülü 2000-2200 Mpa
Eğilme mukavemeti 80- 100 Mpa
Çekme mukavemeti 75-85 MPa
Kopma noktasında uzama 8-16 %
Darbe mukavemeti çentikli Izod 12 KJ/m²
Tolerans Ürünün yerel doğruluğu 0,3-0,5 mm~5 ‰ arasındadır, genel doğruluğun kontrol edilmesi zordur
Post Proses Montajı ,Gömme bakır somunlar, Fiziksel parlatma, Boyama, Elektrokaplama, Serigrafi, Su transfer baskı, Kaplama
Duvar kalınlığı 0,8 mm yukarıda gerekli, 3D çizimlere göre büyük parçalar
Silikon Kalıp Vakumlu Döküm Standart ABS'nin avantajları şunlardır:
1.Doğru Çoğaltma: Tam olarak yeniden üretir ABS parça özellikleri ve detayları.
2.Pürüzsüz Son İşlemler: Parçalarda cilalı, enjeksiyonla kalıplanmışa benzer bir yüzey elde edilir.
3.Maliyet Verimliliği: Enjeksiyon kalıplama gibi yüksek hacimli yöntemlere göre daha ekonomiktir.
4.Hızlı Üretim: Küçük ve orta ölçekli üretim çalışmaları için hızlı geri dönüş.
5.Tasarım Çok Yönlülüğü: Son parçalarda karmaşık tasarımlara ve alttan kesmelere olanak tanır.
6.Prototipleme Mükemmelliği: Seri üretim öncesi prototipleme ve fonksiyonel testler için idealdir.
7.Düşük Hacim Esnekliği: Küçük seri üretim ihtiyaçları için uygundur.
Silikon Kalıp Vakumlu Döküm Standart ABS'nin dezavantajları şunlardır:
1.Sınırlı Malzeme Özellikleri: Nihai ABS parçalarının özellikleri, yüksek dereceli enjeksiyonla kalıplanmış ABS'ninkilerle mükemmel şekilde eşleşmeyebilir.
2.Yüksek Hacimler İçin İdeal Değildir: Düşük ve orta üretim hacimleri için en uygunudur; Büyük ölçekli üretim için uygun maliyetli olmayabilir.
3.Kalıp Aşınması ve Yırtılması: Bu işlemde kullanılan silikon kalıplar zamanla bozulabilir ve dökümlerin kalitesini ve ömrünü etkileyebilir.
4.Teslim Süresi: Proje zaman çizelgelerini etkileyebilecek kalıp oluşturma ve kürleme için teslim süresini içerir.
Sıcaklığa Dayanıklı ABS
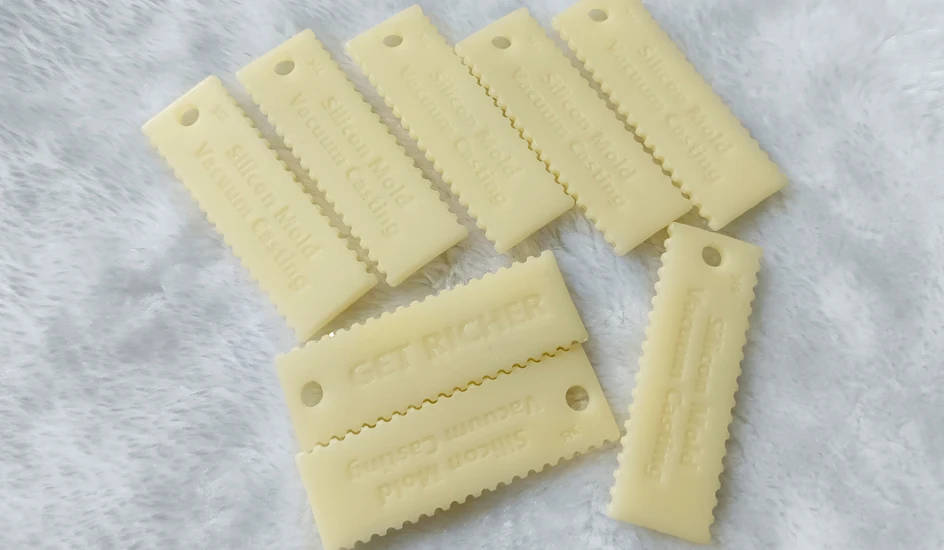
Teknoloji Silikon Kalıp Vakumlu Döküm
Malzemesi Isıya Dayanıklı ABS
Orijinal Renk Beyaz/Siyah/Özel Renk
Termal Deformasyon 100-150°C
Sertlik 80D
Yüzey Durumu Hafif Enjeksiyon İzleri ve Çizikler
Baskı Platformu Boyutu 900*650*450mm
Eğilme Modülü 2000-2200 Mpa
Eğilme Dayanımı 90-115 Mpa
Çekme mukavemeti 55-60 MPa
Kopma noktasında uzama 8-16 %
Darbe mukavemeti çentikli Izod 35 KJ/m²
Tolerans Ürünün yerel doğruluğu 0,3-0,5mm~5 ‰ arasındadır, genel doğruluğun kontrol edilmesi zordur
Post Proses Montajı, İç bakır somunlar, Fiziksel parlatma, Boyama, Elektrokaplama, Serigrafi, Su transfer baskı, Kaplama
Duvar kalınlığı 0,8 mm yukarıda gerekli, 3D çizimlere göre büyük parçalar
Silikon Kalıp Vakumlu Döküm Sıcaklığa Dayanıklı ABS'nin avantajları şunlardır:
1.Geliştirilmiş Isı Direnci: Sıcaklığa dayanıklı ABS, standart ABS'ye kıyasla daha yüksek sıcaklıklara dayanabilir ve ısıya maruz kalan ortamlardaki uygulamalarını genişletir.
2.Dayanıklı ve Sağlam: Sıcaklığa dayanıklı ABS'den yapılmış parçalar, yüksek sıcaklıklarda bile yapısal bütünlüklerini ve özelliklerini koruyarak dayanıklılık sağlar.
3.Geniş Uygulama Aralığı: Isıya maruz kalmanın yaygın olduğu otomotiv, havacılık ve elektronik gibi çeşitli endüstrilerde ihtiyaç duyulan parçalar için idealdir.
4.İyi Kimyasal Direnç: Sıcaklığa dayanıklı ABS tipik olarak kimyasallara karşı iyi bir dirence sahiptir ve çeşitli endüstriyel ortamlara uygunluğunu artırır.
Silikon Kalıp Vakumlu Döküm Sıcaklığa Dayanıklı ABS'nin dezavantajları şunlardır:
1.Sınırlı Isı Direnci: Sıcaklığa dayanıklı ABS, standart ABS'den daha yüksek sıcaklıklara dayanabilirken, yine de sıcaklık sınırları vardır ve çok yüksek sıcaklıklarda deforme olabilir veya özelliklerini kaybedebilir.
2.Malzeme Maliyeti: Sıcaklığa dayanıklı ABS, standart ABS'den daha pahalı olabilir, bu da vakumlu döküm işleminin genel maliyetini artırır.
3.Karmaşık Kalıplama İşlemi: ABS'de sıcaklık direncinin elde edilmesi, daha karmaşık bir kalıplama işlemi gerektirebilir, bu da silikon kalıbın oluşturulmasını daha zor ve daha fazla zaman alıcı hale getirir.
4.Kalıp Aşınması ve Yıpranması: İlgili yüksek sıcaklıklar, silikon kalıbın aşınmasını ve yıpranmasını hızlandırabilir, ömrünü kısaltabilir ve dökümlerin kalitesini etkileyebilir.
Alev Geciktirici ABS
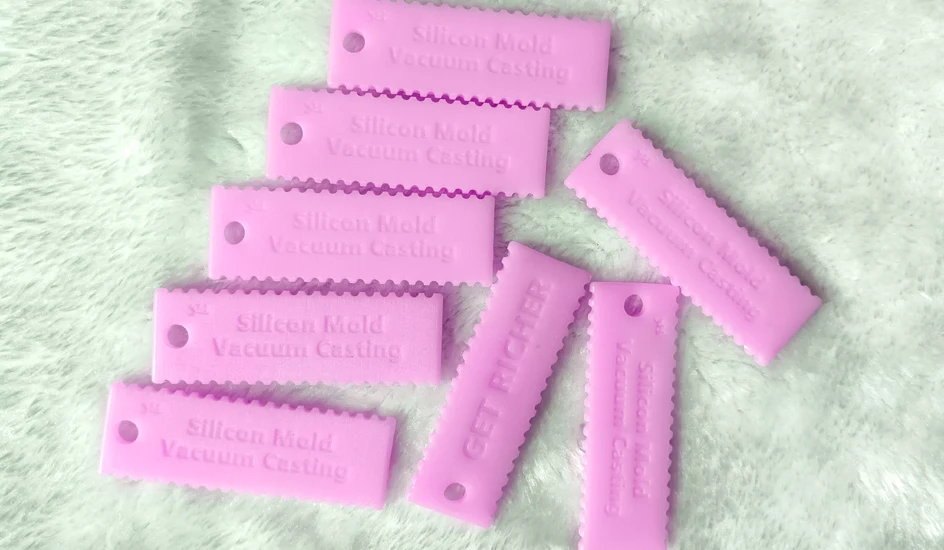
Teknoloji Silikon Kalıp Vakumlu Döküm
Malzemesi Alev Geciktirici ABS
Orijinal Renk Beyaz/Siyah/Özel Renk
Termal Deformasyon 70-80°C
Sertlik 82D
Yüzey Durumu Hafif Enjeksiyon İzleri ve Çizikler
Baskı Platformu Boyutu 900*650*450mm
Eğilme Modülü 2100-2300 Mpa
Eğilme Dayanımı 80-90 Mpa
Çekme mukavemeti 60-70 MPa
Kopma noktasında uzama 8-10 %
Darbe mukavemeti çentikli Izod 15 KJ/m²
Tolerans Ürünün yerel doğruluğu 0,3-0,5mm~5 ‰ arasındadır, genel doğruluğun kontrol edilmesi zordur
Post Proses Montajı, İç bakır somunlar, Fiziksel parlatma, Boyama, Elektrokaplama, Serigrafi, Su transfer baskı, Kaplama
Duvar kalınlığı 0,8 mm yukarıda gerekli, 3D çizimlere göre büyük parçalar
Silikon Kalıp Vakumlu Döküm Alev Geciktirici ABS'nin avantajları şunlardır:
1.Geliştirilmiş Güvenlik: Alev geciktirici ABS, tutuşmaya karşı direnç göstererek ve alevlerin yayılmasını yavaşlatarak artırılmış yangın güvenliği sağlar.
2.Yönetmeliklere Uygunluk: Otomotiv ve elektronik endüstrileri gibi yangın güvenliği ve düzenleyici standartların karşılanmasının gerekli olduğu uygulamalar için idealdir.
3.Dayanıklı ve İşlevsel: ABS'nin dayanıklılığını ve işlevselliğini korurken alev geciktirici özellikler de içerir, bu da onu çok çeşitli uygulamalar için uygun hale getirir.
4.Geniş Uygulanabilirlik: Elektrik muhafazaları, otomotiv iç mekanları ve tüketici elektroniği dahil olmak üzere yangın güvenliğinin önemli olduğu ortamlarda kullanışlıdır.
Silikon Kalıp Vakumlu Döküm Alev Geciktirici ABS'nin dezavantajları şunlardır:
1.Malzeme Karmaşıklığı: Alev geciktirici ABS daha karmaşık bir malzemedir ve döküm sürecini potansiyel olarak daha zorlu hale getirir.
2.Maliyet: Alev geciktirici ABS, standart ABS'den daha pahalı olabilir, bu da genel proje maliyetlerini artırır.
3.Sınırlı Malzeme Seçenekleri: Alev geciktirici malzemelerin seçimi, standart ABS'ye kıyasla sınırlı olabilir, bu da proses için malzeme seçeneklerini kısıtlar.
bilgisayar

Teknoloji Silikon Kalıp Vakumlu Döküm
Malzemesi PC
Orijinal Renk Beyaz/Siyah/Yarı Saydam/Özel Renk
Termal Deformasyon 50-60°C
Sertlik 80D
Yüzey Durumu Hafif Enjeksiyon İzleri ve Çizikler
Baskı Platformu Boyutu 900*650*450mm
Eğilme modülü 1700-1800 Mpa
Eğilme mukavemeti 80 -90 Mpa
Çekme modülü 1900-2000 MPa
Çekme mukavemeti 35-40 MPa
Kopma anında uzama 5-6 %
Darbe mukavemeti çentikli Izod 18 KJ/m²
Tolerans Ürünün yerel doğruluğu 0,3-0,5mm~5 ‰ arasındadır, genel doğruluğu ise kontrol edilmesi zordur
İşlem Sonrası Montaj, İç bakır somunlar, Fiziksel parlatma, Boyama, Elektrokaplama, Serigrafi, Su transfer baskı, Kaplama
Duvar kalınlığı 0,8 mm yukarıda gerekli, 3D çizimlere göre büyük parçalar
Silikon Kalıp Vakumlu Döküm PC'nin avantajları:
1 .Yüksek Darbe Dayanımı: PC, mevcut darbelere en dayanıklı termoplastiklerden biridir ve parçaların mekanik strese ve potansiyel darbelere dayanması gereken uygulamalar için uygun olmasını sağlar.
2.Optik Netlik: PC mükemmel optik netlik ve şeffaflık sunarak lensler, kapaklar ve koruyucu kalkanlar gibi şeffaflık veya ışık geçirme özellikleri gerektiren parçalar için idealdir.
3.Boyutsal Kararlılık: PC ile üretilen parçalar, sıcaklık dalgalanmaları altında bile şekil ve boyutlarını koruyarak tutarlı performans sağlar.
4.Kimyasal Direnç: PC'nin birçok kimyasala karşı iyi bir direnci vardır, bu da onu çeşitli maddelere maruz kalmanın sorun teşkil ettiği uygulamalar için uygun kılar.
5.Düşük Hacimli Üretim: Silikon kalıba vakumlu döküm, özellikle geleneksel üretim yöntemlerinin düşük hacimli çalışmalar için maliyet açısından engelleyici olduğu durumlarda, küçük ve orta miktarlarda PC parçaları üretmek için çok uygundur.
Silikon Kalıp Vakumlu Döküm PC'nin dezavantajları şunlardır:
1.Teslim Süresi: Kalıp oluşturma, kürleme ve döküm dahil üretim sürecinin tamamlanması birkaç gün sürebilir. Bu, son derece sıkı zaman çizelgelerine sahip projeler için uygun olmayabilir.
2.Kalıp Aşınması ve Yırtılması: Silikon kalıpların ömrü sınırlıdır ve özellikle PC gibi yüksek mekanik özelliklere sahip reçinelerle kullanıldığında zamanla aşınabilir. Büyük üretim süreçleri için sık sık kalıp değişimi gerekli olabilir.
3.Son İşleme Gereklidir: Dökme PC parçaları, istenen yüzey kalitesini ve boyutsal doğruluğu elde etmek için düzeltme, zımparalama veya cilalama gibi son işlemler gerektirebilir.
4.Malzeme Büzülmesi: PC reçinesi kürleme işlemi sırasında bir miktar büzülme yaşayabilir, bu da boyut değişikliklerini telafi etmek için kalıp tasarımında ayarlamalar gerektirebilir.
5.Sınırlı Malzeme Geri Dönüşümü: PC ile silikon kalıp vakumlu döküm sırasında üretilen fazla veya atık malzeme genellikle gelecekte kullanılmak üzere geri dönüştürülemez.
6.Maliyet: Bu süreç, PC parçalarının düşük hacimli üretimi için uygun maliyetli olsa da, daha büyük üretim süreçleri için enjeksiyon kalıplama gibi geleneksel üretim yöntemleriyle karşılaştırıldığında birim başına maliyetler daha yüksek olabilir.
PP
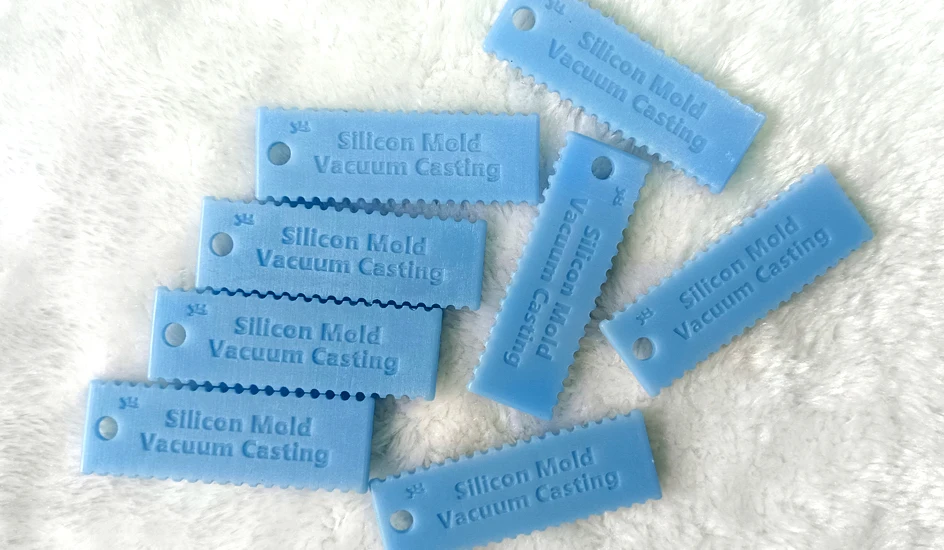
Teknoloji Silikon Kalıp Vakumlu Döküm
Malzemesi PP
Orijinal Renk Beyaz/Siyah/Özel Renk
Termal Deformasyon 50-60°C
Sertlik 75-83D
Yüzey Durumu Hafif Enjeksiyon İzleri ve Çizikler
Baskı Platformu Boyutu 900*650*450mm
Eğilme modülü 600-1300 Mpa
Eğilme mukavemeti 20 -50 Mpa
Çekme mukavemeti 25-35 MPa
Kopma noktasında uzama %5-6
Darbe mukavemeti çentikli Izod 18 KJ/m²
Tolerans Ürünün yerel doğruluğu 0,3-0,5mm~5 ‰ arasındadır, genel doğruluğun ise
Post Proseste kontrol edilmesi zordur Montaj, İç bakır somunlar, Fiziksel parlatma, Boyama, Elektrokaplama, Serigrafi, Su transfer baskı, Kaplama
Duvar kalınlığı 0,8 mm yukarıda gerekli, 3D çizimlere göre büyük parçalar
Silikon Kalıp Vakumlu Döküm PP'nin avantajları şunlardır:
1.Kimyasal Direnç: PP Pek çok kimyasala, asit ve bazlara karşı oldukça dirençli olduğundan parçaların aşındırıcı maddelere maruz kaldığı uygulamalar için uygundur.
2.Düşük Yoğunluk: PP düşük yoğunluğa sahiptir, yani hafiftir. Bu, otomotiv bileşenleri gibi ağırlığın azaltılmasının önemli olduğu uygulamalar için avantajlıdır.
3.İyi Elektrik Yalıtımı: PP iyi bir elektrik yalıtkanıdır, bu da onu elektrik ve elektronik uygulamalar için uygun kılar.
4.Esneklik ve Dayanıklılık: PP, iyi bir esneklik ve dayanıklılık dengesine sahiptir, bu da onu darbelere ve yorulmaya karşı dayanıklı kılar. Bükülmeye ve tekrarlanan kullanıma dayanabilir.
5.Düşük Nem Emilimi: PP, düşük nem emme özelliklerine sahiptir; bu, neme veya neme maruz kalmanın sorun teşkil ettiği uygulamalarda avantajlıdır.
6.Düşük Hacimli Üretim: Silikon kalıba vakumlu döküm, özellikle geleneksel üretim yöntemlerinin düşük hacimli çalışmalar için maliyet açısından engelleyici olduğu durumlarda, küçük ve orta miktarlarda PP parça üretmek için çok uygundur.
Silikon Kalıp Vakumlu Döküm PP-Polipropilenin dezavantajları şunlardır:
1.Teslim Süresi: Kalıp oluşturma, kürleme ve döküm dahil olmak üzere üretim sürecinin tamamlanması birkaç gün sürebilir. Bu, son derece sıkı zaman çizelgelerine sahip projeler için uygun olmayabilir.
2.Kalıp Aşınması ve Yırtılması: Silikon kalıpların sınırlı bir ömrü vardır ve özellikle PP gibi özel katkı maddeleri veya takviyeler içeren reçinelerle kullanıldığında zamanla aşınabilir. Büyük üretim süreçleri için sık sık kalıp değişimi gerekli olabilir.
3.Son İşlem Gereklidir: Dökme PP parçalar, istenen görünümü ve boyutsal doğruluğu elde etmek için düzeltme, zımparalama veya yüzey bitirme gibi son işlemler gerektirebilir.
4.Malzeme Büzülmesi: PP reçine, kürleme işlemi sırasında bir miktar büzülme yaşayabilir ve bu, boyut değişikliklerini telafi etmek için kalıp tasarımında ayarlamalar yapılmasını gerektirebilir.
5.Sınırlı Malzeme Geri Dönüşümü: PP ile silikon kalıp vakumlu döküm sırasında üretilen fazla veya atık malzeme genellikle gelecekte kullanılmak üzere geri dönüştürülemez.
6.Sınırlı Sıcaklık Direnci: PP nispeten düşük bir ısı bozulma sıcaklığına sahiptir; bu, yüksek sıcaklıklarda deforme olabileceği veya yapısal bütünlüğünü kaybedebileceği anlamına gelir. Yüksek sıcaklık uygulamaları için uygun değildir.
Özetle, PP'li silikon kalıba vakumlu döküm, kimyasal direnç, düşük yoğunluk ve esneklik avantajlarını sunar. Ancak teslim süresi, kalıp aşınması ve son işlem ihtiyacı gibi sınırlamalar da beraberinde gelir. PP kullanan 3D baskı projeleri için bu yöntemi seçerken proje gereksinimlerinin ve malzemelerinin dikkatli bir şekilde değerlendirilmesi önemlidir.
Naylon
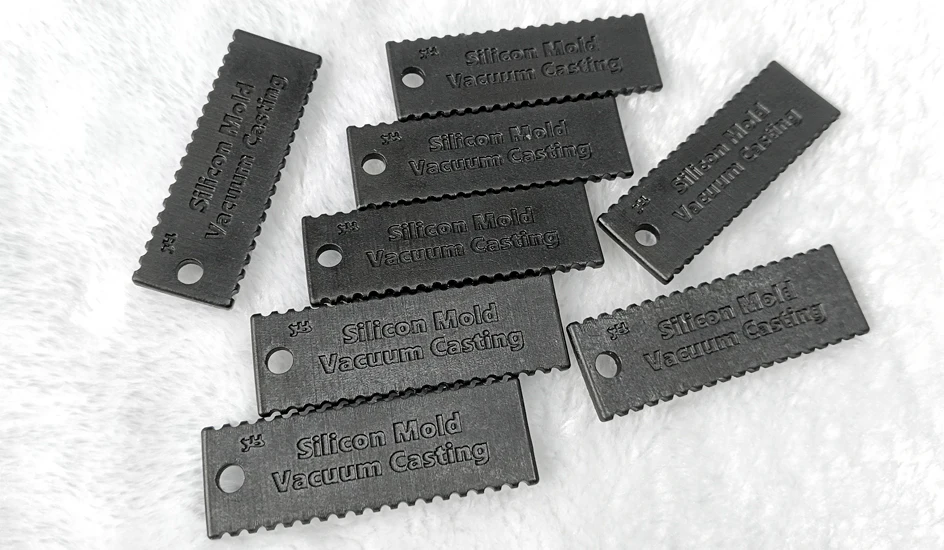
Teknoloji Silikon Kalıp Vakumlu Döküm
Malzemesi Naylon
Orijinal Renk Beyaz/Siyah/Özel Renk
Termal Deformasyon 100-120°C
Sertlik 87D
Yüzey Durumu Hafif Enjeksiyon İzleri ve Çizikler
Baskı Platformu Boyutu 900*650*450mm
Eğilme modülü 1800-2000 Mpa
Eğilme mukavemeti 80-92 Mpa
Çekme mukavemeti 50-60 MPa
Kopma noktasında uzama 10-12 %
Darbe mukavemeti çentikli Izod 17 KJ/m²
Tolerans Ürünün yerel doğruluğu 0,3-0,5mm~5 ‰ arasındadır, genel doğruluğun kontrol edilmesi zordur
Post Proses Montajı, Ankastre bakır somunlar, Fiziksel parlatma, Boyama, Elektrokaplama, Serigrafi, Su transfer baskı, Kaplama
Duvar kalınlığı 0,8 mm yukarıda gerekli, 3D çizimlere göre büyük parçalar
Silikon Kalıp Vakumlu Döküm Naylonun avantajları şunlardır:
1.Yüksek Mekanik Mukavemet: Naylon parçalar üretilir Bu işlem sayesinde yüksek çekme mukavemeti, tokluk ve darbe direnci dahil olmak üzere mükemmel mekanik özellikler sergiler. Bu, Naylon'u zorlu uygulamalar için uygun hale getirir.
2.Dayanıklılık: Naylon, dayanıklılığı ve aşınma ve yıpranmaya karşı direnciyle bilinir; bu da onu sürtünme ve aşınmaya dayanması gereken bileşenler için ideal kılar.
3.Kimyasal Direnç: Naylon birçok kimyasal maddeye, yağa ve solvente karşı iyi bir dirence sahiptir, bu da onu çeşitli maddelere maruz kalmanın endişe verici olduğu uygulamalar için uygun kılar.
4.Düşük Sürtünme Katsayısı: Naylon düşük bir sürtünme katsayısına sahiptir, bu da onu hareketli parçalar veya kayan mekanizmalar içeren uygulamalar için ideal kılar.
5.Esneklik: Naylon parçalar, kullanılan Naylon türüne bağlı olarak bir dereceye kadar esneklik sergileyebilir. Bu, onu sağlamlık ve esneklik arasında denge gerektiren uygulamalar için uygun kılar.
6.Düşük Hacimli Üretim: Silikon kalıba vakumlu döküm, özellikle geleneksel üretim yöntemlerinin düşük hacimli çalışmalar için maliyet açısından engelleyici olduğu durumlarda, küçük ve orta miktarlarda Naylon parça üretmek için çok uygundur.
Silikon Kalıp Vakumlu Döküm Cam elyaf Naylonun dezavantajları şunlardır:
1.Teslim Süresi: Kalıp oluşturma, kürleme ve döküm dahil olmak üzere üretim sürecinin tamamlanması birkaç gün sürebilir. Bu, son derece sıkı zaman çizelgelerine sahip projeler için uygun olmayabilir.
2.Kalıp Aşınması ve Yırtılması: Silikon kalıpların ömrü sınırlıdır ve özellikle Naylon gibi yüksek mekanik özelliklere sahip reçinelerle kullanıldığında zamanla aşınabilir. Büyük üretim süreçleri için sık sık kalıp değişimi gerekli olabilir.
3.Son İşleme Gereklidir: Dökme Naylon parçalar, istenen görünümü ve boyutsal doğruluğu elde etmek için düzeltme, zımparalama veya yüzey bitirme gibi son işlemler gerektirebilir.
4.Malzeme Büzülmesi: Naylon reçine, kürleme işlemi sırasında bir miktar büzülme yaşayabilir ve bu, boyutsal değişiklikleri telafi etmek için kalıp tasarımında ayarlamalar yapılmasını gerektirebilir.
5.Sınırlı Malzeme Geri Dönüşümü: Naylon ile silikon kalıp vakumlu döküm sırasında üretilen fazla veya atık malzeme genellikle gelecekte kullanılmak üzere geri dönüştürülemez.
6.Higroskopik Doğa: Naylon higroskopiktir, yani zamanla ortamdaki nemi emebilir. Bu, uygun şekilde kullanılıp saklanmadığı takdirde mekanik özelliklerini etkileyebilir.
POM
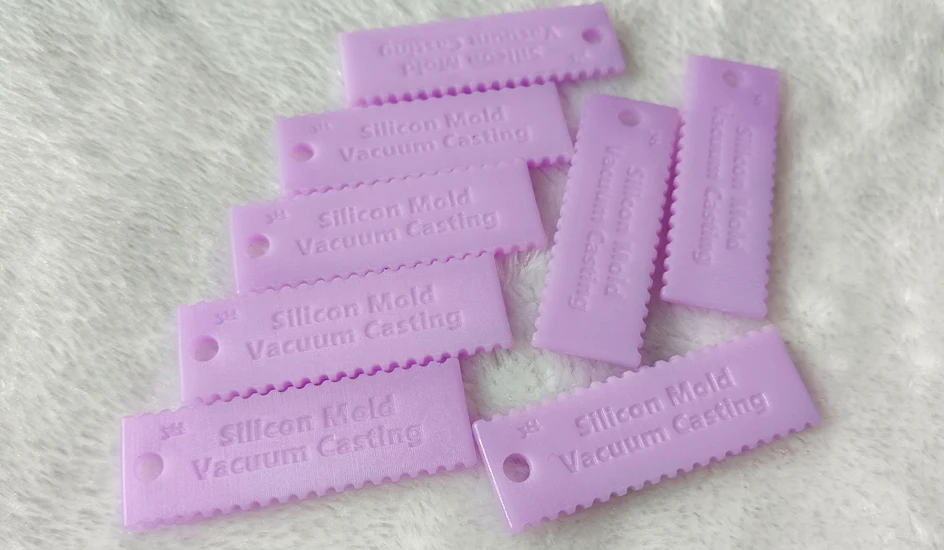
Teknoloji Silikon Kalıp Vakumlu Döküm
Malzemesi POM
Orijinal Renk Beyaz/Siyah/Özel Renk
Termal Deformasyon 70-80°C
Sertlik 80D
Yüzey Durumu Hafif Enjeksiyon İzleri ve Çizikler
Baskı Platformu Boyutu 900*650*450mm
Eğilme modülü 2400-2500 Mpa
Eğilme mukavemeti 100-110 Mpa
Çekme mukavemeti 60-70 MPa
Kopma noktasında uzama 10-12 %
Darbe mukavemeti çentikli Izod 17 KJ/m²
Tolerans Ürünün yerel doğruluğu 0,3-0,5mm~5 ‰ arasındadır, genel doğruluğun kontrol edilmesi zordur
Post Proses Montajı, Ankastre bakır somunlar, Fiziksel parlatma, Boyama, Elektrokaplama, Serigrafi, Su transfer baskı, Kaplama
Duvar kalınlığı 0,8 mm yukarıda gerekli, 3D çizimlere göre büyük parçalar
Silikon Kalıp Vakumlu Döküm POM'un avantajları şunlardır:
1.Mükemmel Mekanik Özellikler: POM olağanüstü sergiler Yüksek çekme mukavemeti, sertlik ve darbe direnci dahil olmak üzere mekanik özellikler. Genellikle sağlam ve dayanıklı bileşenler gerektiren uygulamalarda kullanılır.
2.Düşük Sürtünme: POM'un düşük sürtünme katsayısı vardır, bu da onu kayma veya dönme hareketleri içeren parçalar için ideal kılar. Genellikle dişlilerde, yataklarda ve sürtünmenin azaltılmasının önemli olduğu diğer bileşenlerde kullanılır.
3.Boyutsal Kararlılık: POM mükemmel boyutsal kararlılığa sahiptir; bu, bu malzemeden yapılan parçaların sıcaklık değişimleri ve mekanik stres altında bile şekil ve boyutlarını koruduğu anlamına gelir.
4.Kimyasal Direnç: POM, solventler, yağlar ve yakıtlar da dahil olmak üzere birçok kimyasala karşı dirençlidir, bu da onu çeşitli maddelere maruz kalmanın endişe verici olduğu uygulamalar için uygun kılar.
5.Düşük Nem Emilimi: POM, düşük nem emme özelliklerine sahiptir; bu, neme veya neme maruz kalmanın performansı etkileyebileceği uygulamalarda avantajlıdır.
6.Düşük Hacimli Üretim: Silikon kalıba vakumlu döküm, özellikle geleneksel üretim yöntemlerinin düşük hacimli çalışmalar için maliyet açısından engelleyici olacağı durumlarda, küçük ve orta miktarlarda POM parçaları üretmek için çok uygundur.
Silikon Kalıp Vakumlu Döküm POM'un dezavantajları şunlardır:
1.Teslim Süresi: Kalıp oluşturma, kürleme ve döküm dahil olmak üzere üretim sürecinin tamamlanması birkaç gün sürebilir. Bu, son derece sıkı zaman çizelgelerine sahip projeler için uygun olmayabilir.
2.Kalıp Aşınması ve Yırtılması: Silikon kalıpların ömrü sınırlıdır ve özellikle POM gibi yüksek mekanik özelliklere sahip reçinelerle kullanıldığında zamanla aşınabilir. Büyük üretim süreçleri için sık sık kalıp değişimi gerekli olabilir.
3.Son İşleme Gereklidir: Dökme POM parçaları, istenen görünümü ve boyutsal doğruluğu elde etmek için düzeltme, zımparalama veya yüzey bitirme gibi işlem sonrası işlemleri gerektirebilir.
4.Malzeme Büzülmesi: POM reçinesi kürleme işlemi sırasında bir miktar büzülme yaşayabilir ve bu da boyutsal değişiklikleri telafi etmek için kalıp tasarımında ayarlamalar yapılmasını gerektirebilir.
5.Sınırlı Malzeme Geri Dönüşümü: POM ile silikon kalıp vakumlu döküm sırasında üretilen fazla veya atık malzeme genellikle gelecekte kullanılmak üzere geri dönüştürülemez.
6.Maliyet: Bu süreç, POM parçalarının düşük hacimli üretimi için uygun maliyetli olsa da, daha büyük üretim süreçleri için enjeksiyon kalıplama gibi geleneksel üretim yöntemleriyle karşılaştırıldığında birim başına maliyetler daha yüksek olabilir.
Özetle, POM ile silikon kalıba vakumlu döküm, mükemmel mekanik özellikler, düşük sürtünme ve kimyasal direnç avantajlarını sunar. Ancak teslim süresi, kalıp aşınması ve son işlem ihtiyacı gibi sınırlamalar da beraberinde gelir. POM kullanan 3D baskı projeleri için bu yöntemi seçerken proje gereksinimlerinin ve malzemelerinin dikkatli bir şekilde değerlendirilmesi önemlidir.
Silikon


Teknoloji Silikon Kalıp Vakumlu Döküm
Malzemesi Silikon
Orijinal Renk Beyaz/Siyah/Özel Renk
Termal Deformasyon 50-70°C
Yüzey Durumu Hafif Enjeksiyon İzleri ve Çizikler
Baskı Platformu Boyutu 900*650*450mm
Tolerans Ürünün yerel doğruluğu 0,3-0,5 mm arasındadır. ~5 ‰, genel doğruluğu kontrol etmek zor olsa da
Sertlik: Shore 30A, 40A, 50A, 60A, 70A, 80A, 90A
Duvar kalınlığı 0,8 mm yukarıda gereklidir, 3D çizimlere göre büyük parçalar
Silikonun avantajları şunlardır:
1.Elastomerik Özellikler : Silikon kauçuk, esneklik ve dayanıklılık da dahil olmak üzere mükemmel elastomerik özellikler sergiler. Yumuşak, esnek olması ve deformasyon sonrasında orijinal şekline dönebilmesi gereken parçaların üretimi için idealdir.
2.Kimyasal Direnç: Silikon birçok kimyasal maddeye, yağa ve solvente karşı dirençlidir, bu da onu çeşitli maddelere maruz kalmanın endişe verici olduğu uygulamalar için uygun kılar.
3.Düşük Hacimli Üretim: Silikon kalıba vakumlu döküm, özellikle geleneksel üretim yöntemlerinin düşük hacimli çalışmalar için maliyet açısından engelleyici olduğu durumlarda, küçük ve orta miktarlarda esnek silikon parçalar üretmek için çok uygundur.
4.Kişiselleştirme: Silikon malzemeler farklı renkler elde etmek veya özel estetik gereksinimleri karşılamak için renklendirilebilir, pigmentlenebilir veya harmanlanabilir.
Silikonun dezavantajları şunlardır:
1. Teslim Süresi: Kalıp oluşturma, kürleme ve dökümü de içeren üretim sürecinin tamamlanması birkaç gün sürebilir. Bu, son derece sıkı zaman çizelgelerine sahip projeler için uygun olmayabilir.
2.Kalıp Aşınması ve Yırtılması: Silikon kalıpların ömrü sınırlıdır ve özellikle özel katkı maddeleri veya takviyeler içeren reçinelerle kullanıldığında zamanla aşınabilir. Büyük üretim süreçleri için sık sık kalıp değişimi gerekli olabilir.
3.Son İşlem Gereklidir: Dökme silikon parçalar, istenen görünümü ve boyutsal doğruluğu elde etmek için düzeltme, zımparalama veya yüzey bitirme gibi son işlemler gerektirebilir.
4.Malzeme Büzülmesi: Silikon reçine kürleme işlemi sırasında bir miktar büzülme yaşayabilir ve bu da boyutsal değişiklikleri telafi etmek için kalıp tasarımında ayarlamalar yapılmasını gerektirebilir.
5.Maliyet: Bu süreç, esnek silikon parçaların düşük hacimli üretimi için uygun maliyetli olsa da, daha büyük üretim süreçleri için enjeksiyonlu kalıplama gibi geleneksel üretim yöntemleriyle karşılaştırıldığında birim başına maliyetler daha yüksek olabilir.