Materialen- Standaard ABS
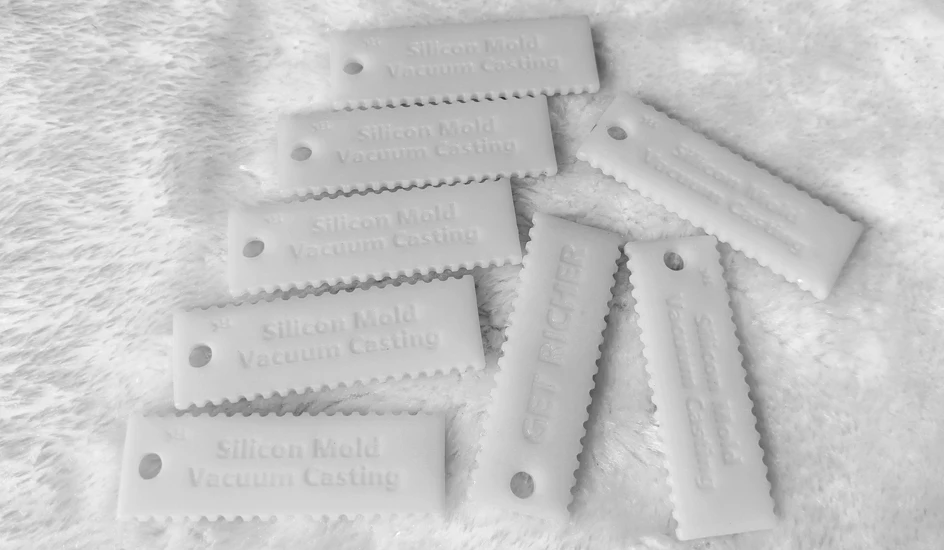
Technologie Siliciumvorm Vacuümgieten
Materiaal Standaard ABS
Originele kleur Wit/zwart/aangepaste kleur
Thermische vervorming 70-100°C
Hardheid 83D
Oppervlaktesituatie Lichte injectiesporen en krassen
Afdrukplatformgrootte 900*650*450mm
Buigmodulus 2000-2200 Mpa
Buigsterkte 80- 100 Mpa
Treksterkte 75-85 MPa
Rek bij breuk 8-16 %
Slagsterkte gekerfd Izod 12 KJ/m²
Tolerantie De lokale nauwkeurigheid van het product ligt tussen 0,3-0,5 mm~5 ‰, terwijl de algehele nauwkeurigheid moeilijk te controleren is
Assemblage na proces , Ingezette koperen moeren, Fysisch polijsten, Schilderen, Galvaniseren, Zeefdruk, Watertransferprinten, Coating
Wanddikte vereist 0,8 mm hierboven, grote onderdelen volgens 3D-tekeningen.
De voordelen van Silicon Mold Vacuum Casting Standaard ABS zijn:
1. Nauwkeurige replicatie: reproduceert nauwkeurig Eigenschappen en details van ABS-onderdelen.
2. Gladde afwerkingen: resulteert in onderdelen met een gepolijst, spuitgegoten oppervlak.
3. Kostenefficiëntie: goedkoper dan grootschalige methoden zoals spuitgieten.
4.Snelle productie: snelle doorlooptijd voor kleine tot middelgrote productieruns.
5. Veelzijdigheid in ontwerp: Maakt ingewikkelde ontwerpen en ondersnijdingen in de laatste onderdelen mogelijk.
6.Prototyping Excellence: Ideaal voor prototyping en functionele testen vóór massaproductie.
7. Flexibiliteit met laag volume: geschikt voor productiebehoeften in kleine batches.
De nadelen van Silicon Mold Vacuum Casting Standaard ABS zijn:
1.Beperkte materiaaleigenschappen: De eigenschappen van de uiteindelijke ABS-onderdelen komen mogelijk niet perfect overeen met die van hoogwaardig spuitgegoten ABS.
2.Niet ideaal voor grote volumes: het meest geschikt voor lage tot gemiddelde productievolumes; is mogelijk niet kosteneffectief voor grootschalige productie.
3.Slijtage van de mal: De siliconen mallen die in dit proces worden gebruikt, kunnen na verloop van tijd verslechteren, wat de kwaliteit en levensduur van de afgietsels beïnvloedt.
4.Doorlooptijd: omvat de doorlooptijd voor het maken en uitharden van mallen, wat van invloed kan zijn op de projecttijdlijnen.
Temperatuurbestendig ABS
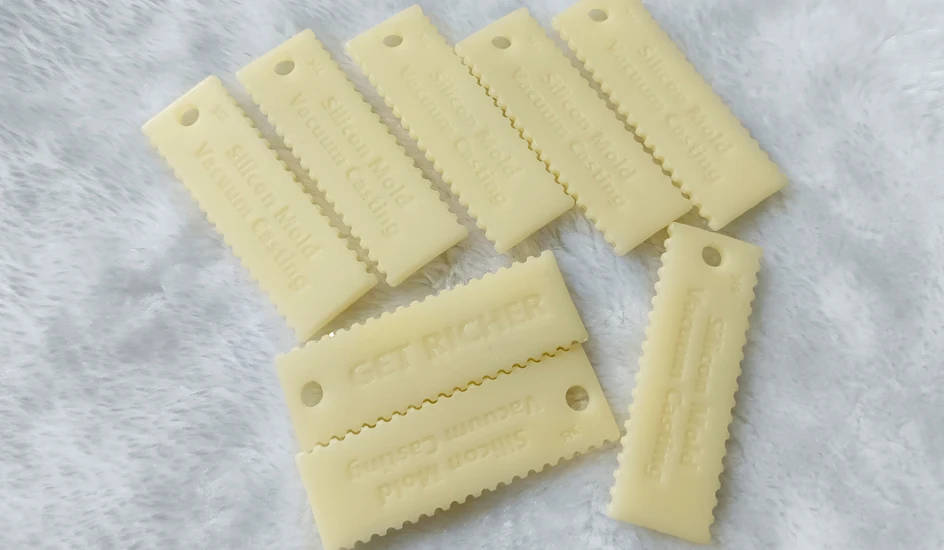
Technologie Siliciumvorm Vacuümgietmateriaal
Temperatuurbestendig ABS
Originele kleur Wit/zwart/aangepaste kleur
Thermische vervorming 100-150°C
Hardheid 80D
Oppervlaktesituatie Lichte injectiesporen en krassen
Afdrukplatformgrootte 900*650*450mm
Buigmodulus 2000-2200 Mpa
Buigsterkte 90-115 Mpa
Treksterkte 55-60 MPa
Rek bij breuk 8-16 %
Slagsterkte gekerfd Izod 35 KJ/m²
Tolerantie De lokale nauwkeurigheid van het product ligt tussen 0,3-0,5 mm~5 ‰, terwijl de algehele nauwkeurigheid moeilijk te controleren is
. Procesassemblage, ingezette koperen moeren, fysiek polijsten, schilderen, galvaniseren, zeefdruk, watertransferprinten, coating
Wanddikte vereist 0,8 mm hierboven, grote onderdelen volgens 3D-tekeningen.
De voordelen van Silicon Mold Vacuümgieten Temperatuurbestendig ABS zijn:
1. Verbeterd Hittebestendigheid: Temperatuurbestendig ABS is bestand tegen hogere temperaturen in vergelijking met standaard ABS, waardoor de toepassingen in aan hitte blootgestelde omgevingen worden uitgebreid.
2.Duurzaam en stevig: onderdelen gemaakt van temperatuurbestendig ABS behouden hun structurele integriteit en eigenschappen, zelfs bij hoge temperaturen, waardoor duurzaamheid wordt gegarandeerd.
3. Breed toepassingsbereik: Ideaal voor onderdelen die nodig zijn in verschillende industrieën, zoals de automobielsector, de ruimtevaart en de elektronica, waar blootstelling aan hitte gebruikelijk is.
4.Goede chemische bestendigheid: Temperatuurbestendig ABS is doorgaans goed bestand tegen chemicaliën, waardoor het geschikt is voor diverse industriële omgevingen.
De nadelen van temperatuurbestendig ABS in siliconenvormvacuümgieten zijn:
1.Beperkte hittebestendigheid: hoewel temperatuurbestendig ABS hogere temperaturen kan weerstaan dan standaard ABS, heeft het nog steeds temperatuurgrenzen en kan het bij zeer hoge temperaturen vervormen of eigenschappen verliezen.
2.Materiaalkosten: Temperatuurbestendig ABS kan duurder zijn dan standaard ABS, waardoor de totale kosten van het vacuümgietproces stijgen.
3.Complex gietproces: Het bereiken van temperatuurbestendigheid in ABS kan een complexer gietproces vereisen, waardoor het moeilijker en tijdrovender wordt om de siliconen mal te maken.
4. Vormslijtage: de hogere temperaturen kunnen de slijtage van de siliconen mal versnellen, de levensduur ervan verkorten en de kwaliteit van de gietstukken beïnvloeden.
Vlamvertragend ABS
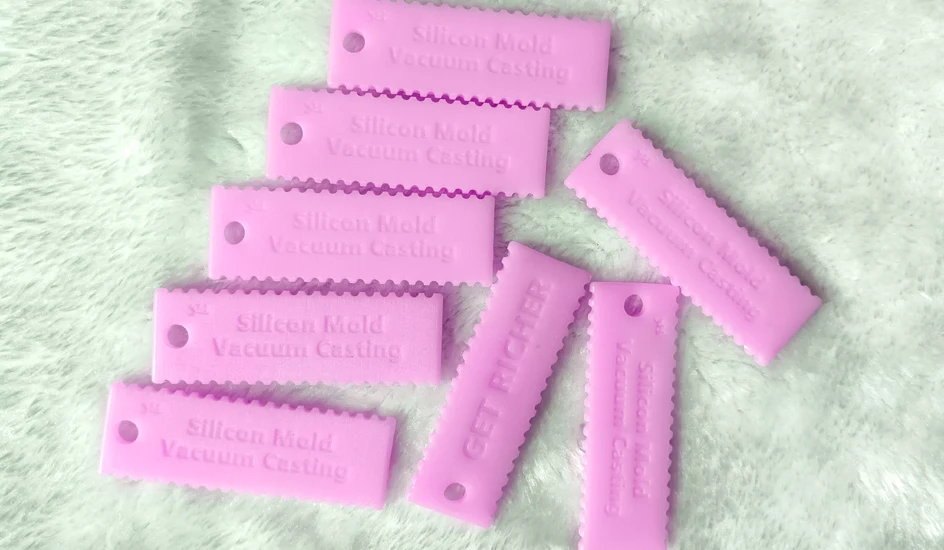
Technologie Siliciumvorm Vacuümgietmateriaal
Vlamvertragend ABS
Originele kleur Wit/zwart/aangepaste kleur
Thermische vervorming 70-80°C
Hardheid 82D
Oppervlaktesituatie Lichte injectiesporen en krassen
Afdrukplatformgrootte 900*650*450mm
Buigmodulus 2100-2300 Mpa
Buigsterkte 80-90 Mpa
Treksterkte 60-70 MPa
Rek bij breuk 8-10 %
Slagsterkte gekerfd Izod 15 KJ/m²
Tolerantie De lokale nauwkeurigheid van het product ligt tussen 0,3-0,5 mm~5 ‰, terwijl de algehele nauwkeurigheid moeilijk te controleren is
. Procesassemblage, ingezette koperen moeren, fysiek polijsten, schilderen, galvaniseren, zeefdruk, watertransferprinten, coating
Wanddikte vereist 0,8 mm hierboven, grote onderdelen volgens 3D-tekeningen.
De voordelen van Silicon Mold Vacuümgieten Vlamvertragend ABS zijn:
1. Verbeterd Veiligheid: Vlamvertragend ABS biedt verhoogde brandveiligheid door weerstand te bieden aan ontsteking en de verspreiding van vlammen te vertragen.
2. Naleving van regelgeving: Ideaal voor toepassingen waarbij het voldoen aan brandveiligheids- en regelgevingsnormen essentieel is, zoals in de auto- en elektronica-industrie.
3.Duurzaam en functioneel: Behoudt de duurzaamheid en functionaliteit van ABS terwijl het vlamvertragende eigenschappen bevat, waardoor het geschikt is voor een breed scala aan toepassingen.
4. Brede toepasbaarheid: Nuttig in omgevingen waar brandveiligheid een probleem is, inclusief elektrische behuizingen, auto-interieurs en consumentenelektronica.
De nadelen van siliciumvorm-vacuümgieten, vlamvertragend ABS zijn:
1.Materiële complexiteit: Vlamvertragend ABS is een complexer materiaal, waardoor het gietproces potentieel uitdagender wordt.
2. Kosten: Vlamvertragend ABS kan duurder zijn dan standaard ABS, waardoor de totale projectkosten stijgen.
3.Beperkte materiaalopties: De keuze aan vlamvertragende materialen kan beperkt zijn in vergelijking met standaard ABS, waardoor de materiaalopties voor het proces beperkt worden.
PC

Technologie Siliciumvorm Vacuümgieten
Materiaal PC
Originele kleur Wit/zwart/doorschijnend/aangepaste kleur
Thermische vervorming 50-60°C
Hardheid 80D
Oppervlaktesituatie Lichte injectiesporen en krassen
Afdrukplatformgrootte 900*650*450mm
Buigmodulus 1700-1800 Mpa
Buigsterkte 80 -90 Mpa
Trekmodulus 1900-2000 MPa
Treksterkte 35-40 MPa
Rek bij breuk 5-6 %
Slagsterkte gekerfd Izod 18 KJ/m²
Tolerantie De lokale nauwkeurigheid van het product ligt tussen 0,3-0,5 mm~5 ‰, terwijl de algehele nauwkeurigheid is moeilijk te controleren
Post-processassemblage, ingezette koperen moeren, fysiek polijsten, schilderen, galvaniseren, zeefdrukken, watertransferprinten, coating
Wanddikte vereist 0,8 mm hierboven, grote onderdelen volgens 3D-tekeningen
De voordelen van Silicon Mold Vacuum Casting PC zijn:
1 .Hoge slagvastheid: PC is een van de meest slagvaste thermoplasten die verkrijgbaar zijn, waardoor het geschikt is voor toepassingen waarbij onderdelen mechanische spanning en potentiële schokken moeten kunnen weerstaan.
2.Optische helderheid: PC biedt uitstekende optische helderheid en transparantie, waardoor het ideaal is voor onderdelen die doorzichtige of lichtdoorlatende eigenschappen vereisen, zoals lenzen, afdekkingen en beschermende schilden.
3.Dimensionale stabiliteit: Onderdelen geproduceerd met PC behouden hun vorm en afmetingen, zelfs onder temperatuurschommelingen, waardoor consistente prestaties worden gegarandeerd.
4. Chemische bestendigheid: PC is goed bestand tegen veel chemicaliën, waardoor het geschikt is voor toepassingen waarbij blootstelling aan verschillende stoffen een probleem is.
5. Productie in laag volume: vacuümgieten in siliconenvormen is zeer geschikt voor het produceren van kleine tot middelgrote hoeveelheden pc-onderdelen, vooral wanneer traditionele productiemethoden onbetaalbaar zouden zijn voor kleine oplages.
De nadelen van Silicon Mold Vacuum Casting PC zijn:
1. Doorlooptijd: het productieproces, inclusief het maken, uitharden en gieten van de mal, kan enkele dagen in beslag nemen. Dit is mogelijk niet geschikt voor projecten met extreem krappe tijdlijnen.
2. Schimmelslijtage: Siliconen mallen hebben een beperkte levensduur en kunnen na verloop van tijd verslijten, vooral bij gebruik met harsen met hoge mechanische eigenschappen zoals PC. Bij grote productieruns kan het regelmatig vervangen van de matrijs nodig zijn.
3. Nabewerking vereist: gegoten pc-onderdelen vereisen mogelijk nabewerking, zoals bijsnijden, schuren of polijsten, om de gewenste oppervlakteafwerking en maatnauwkeurigheid te bereiken.
4. Materiaalkrimp: PC-hars kan tijdens het uithardingsproces enige krimp ervaren, waardoor mogelijk aanpassingen aan het matrijsontwerp nodig zijn om dimensionale veranderingen te compenseren.
5. Beperkte materiaalrecycling: het overtollige of afvalmateriaal dat ontstaat tijdens het vacuümgieten van siliconenvormen met pc is doorgaans niet recycleerbaar voor toekomstig gebruik.
6. Kosten: hoewel dit proces kosteneffectief kan zijn voor de productie van pc-onderdelen in kleine volumes, kan het hogere kosten per eenheid met zich meebrengen in vergelijking met traditionele productiemethoden zoals spuitgieten voor grotere productieruns.
PP
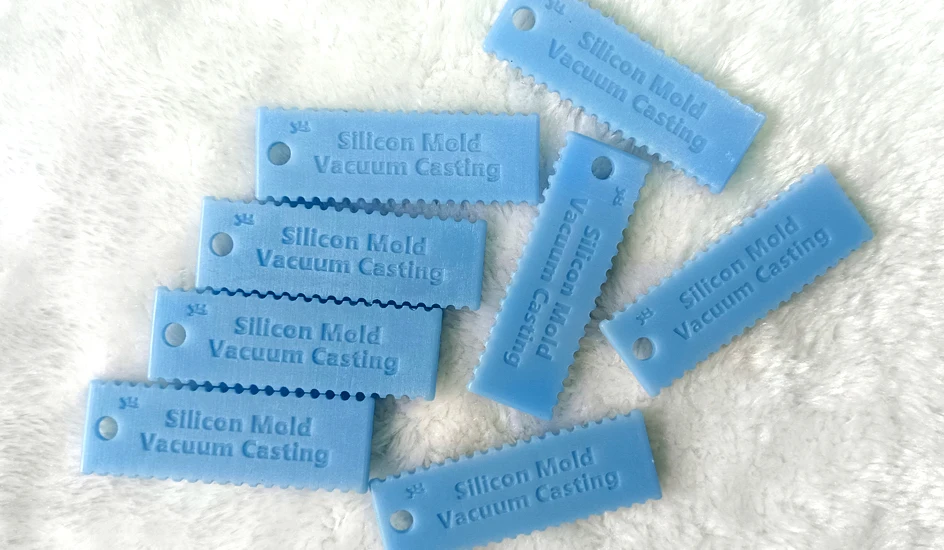
Technologie Siliciumvorm Vacuümgieten
Materiaal PP
Originele kleur Wit/zwart/aangepaste kleur
Thermische vervorming 50-60°C
Hardheid 75-83D
Oppervlaktesituatie Lichte injectiesporen en krassen
Afdrukplatformgrootte 900*650*450mm
Buigmodulus 600-1300 Mpa
Buigsterkte 20 -50 Mpa
Treksterkte 25-35 MPa
Rek bij breuk 5-6 %
Slagsterkte gekerfd Izod 18 KJ/m²
Tolerantie De lokale nauwkeurigheid van het product ligt tussen 0,3-0,5 mm~5 ‰, terwijl de algehele nauwkeurigheid moeilijk te controleren
is Montage, ingezette koperen moeren, fysiek polijsten, schilderen, galvaniseren, zeefdruk, watertransferprinten, coating
Wanddikte vereist 0,8 mm hierboven, grote onderdelen volgens 3D-tekeningen.
De voordelen van Silicon Mold Vacuum Casting PP zijn:
1. Chemische weerstand: PP is zeer goed bestand tegen vele chemicaliën, zuren en basen, waardoor het geschikt is voor toepassingen waarbij onderdelen worden blootgesteld aan corrosieve stoffen.
2. Lage dichtheid: PP heeft een lage dichtheid, wat betekent dat het licht van gewicht is. Dit is voordelig voor toepassingen waarbij gewichtsreductie belangrijk is, zoals bij auto-onderdelen.
3. Goede elektrische isolatie: PP is een goede elektrische isolator, waardoor het geschikt is voor elektrische en elektronische toepassingen.
4.Flexibiliteit en taaiheid: PP heeft een goede balans tussen flexibiliteit en taaiheid, waardoor het bestand is tegen schokken en vermoeidheid. Het is bestand tegen buigen en herhaald gebruik.
5. Lage vochtopname: PP heeft lage vochtabsorptie-eigenschappen, wat voordelig is in toepassingen waarbij blootstelling aan vocht of vochtigheid een probleem is.
6. Productie met laag volume: vacuümgieten in siliconenvormen is zeer geschikt voor het produceren van kleine tot middelgrote hoeveelheden PP-onderdelen, vooral wanneer traditionele productiemethoden onbetaalbaar zouden zijn voor kleine oplages.
De nadelen van PP-polypropyleen vacuümgieten met siliciumvormen zijn:
1. Doorlooptijd: het productieproces, inclusief het maken, uitharden en gieten van de mal, kan enkele dagen in beslag nemen. Dit is mogelijk niet geschikt voor projecten met extreem krappe tijdlijnen.
2. Schimmelslijtage: Siliconen mallen hebben een beperkte levensduur en kunnen na verloop van tijd verslijten, vooral wanneer ze worden gebruikt met harsen die speciale additieven of versterkingen zoals PP hebben. Bij grote productieruns kan het regelmatig vervangen van de matrijs nodig zijn.
3. Nabewerking vereist: Gegoten PP-onderdelen kunnen nabewerking vereisen, zoals bijsnijden, schuren of oppervlakteafwerking, om het gewenste uiterlijk en de maatnauwkeurigheid te bereiken.
4. Materiaalkrimp: PP-hars kan tijdens het uithardingsproces enige krimp ervaren, waardoor mogelijk aanpassingen aan het matrijsontwerp nodig zijn om dimensionale veranderingen te compenseren.
5. Beperkte materiaalrecycling: het overtollige of afvalmateriaal dat ontstaat tijdens het vacuümgieten van siliconenvormen met PP is doorgaans niet recycleerbaar voor toekomstig gebruik.
6.Beperkte temperatuurbestendigheid: PP heeft een relatief lage warmtevervormingstemperatuur, wat betekent dat het bij hogere temperaturen kan vervormen of de structurele integriteit kan verliezen. Het is niet geschikt voor toepassingen bij hoge temperaturen.
Samenvattend biedt vacuümgieten van siliconenvormen met PP de voordelen van chemische bestendigheid, lage dichtheid en flexibiliteit. Het brengt echter beperkingen met zich mee, zoals doorlooptijd, matrijsslijtage en de noodzaak van nabewerking. Een zorgvuldige afweging van projectvereisten en materialen is essentieel bij het kiezen van deze methode voor 3D-printprojecten met PP.
Nylon
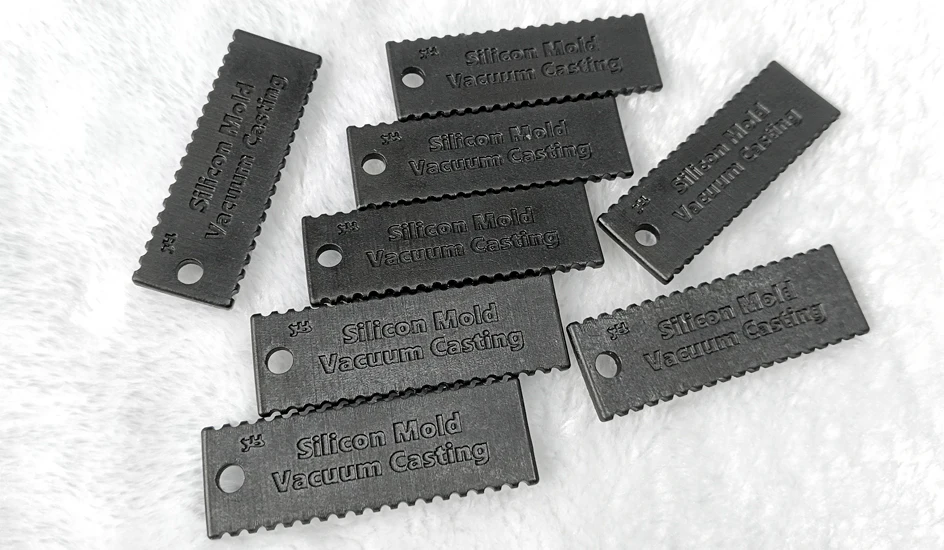
Technologie Siliciumvorm Vacuümgieten
Materiaal Nylon
Originele kleur Wit/zwart/aangepaste kleur
Thermische vervorming 100-120°C
Hardheid 87D
Oppervlaktesituatie Lichte injectiesporen en krassen
Afdrukplatformgrootte 900*650*450mm
Buigmodulus 1800-2000 Mpa
Buigsterkte 80-92 Mpa
Treksterkte 50-60 MPa
Rek bij breuk 10-12 %
Slagsterkte gekerfd Izod 17 KJ/m²
Tolerantie De lokale nauwkeurigheid van het product ligt tussen 0,3-0,5 mm~5 ‰, terwijl de algehele nauwkeurigheid moeilijk te controleren is
. Ingezette koperen moeren, fysiek polijsten, schilderen, galvaniseren, zeefdruk, watertransferprinten, coating
Wanddikte vereist 0,8 mm hierboven, grote onderdelen volgens 3D-tekeningen.
De voordelen van Silicon Mold Vacuum Casting Nylon zijn:
1. Hoge mechanische sterkte: geproduceerde nylon onderdelen vertonen door dit proces uitstekende mechanische eigenschappen, waaronder hoge treksterkte, taaiheid en slagvastheid. Dit maakt Nylon geschikt voor veeleisende toepassingen.
2.Duurzaamheid: Nylon staat bekend om zijn duurzaamheid en weerstand tegen slijtage, waardoor het ideaal is voor componenten die wrijving en slijtage moeten weerstaan.
3. Chemische weerstand: Nylon is goed bestand tegen veel chemicaliën, oliën en oplosmiddelen, waardoor het geschikt is voor toepassingen waarbij blootstelling aan verschillende stoffen een probleem is.
4. Lage wrijvingscoëfficiënt: Nylon heeft een lage wrijvingscoëfficiënt, waardoor het ideaal is voor toepassingen met bewegende delen of schuifmechanismen.
5.Flexibiliteit: Nylon onderdelen kunnen een zekere mate van flexibiliteit vertonen, afhankelijk van het specifieke type nylon dat wordt gebruikt. Dit maakt het geschikt voor toepassingen die een evenwicht tussen stijfheid en flexibiliteit vereisen.
6. Productie met laag volume: vacuümgieten in siliconenvormen is zeer geschikt voor het produceren van kleine tot middelgrote hoeveelheden nylononderdelen, vooral wanneer traditionele productiemethoden onbetaalbaar zouden zijn voor kleine oplages.
De nadelen van Silicon Mold Vacuum Casting glasvezel nylon zijn:
1. Doorlooptijd: het productieproces, inclusief het maken, uitharden en gieten van de mal, kan enkele dagen in beslag nemen. Dit is mogelijk niet geschikt voor projecten met extreem krappe tijdlijnen.
2. Vormslijtage: Siliconen mallen hebben een beperkte levensduur en kunnen na verloop van tijd verslijten, vooral bij gebruik met harsen met hoge mechanische eigenschappen zoals nylon. Bij grote productieruns kan het regelmatig vervangen van de matrijs nodig zijn.
3. Nabewerking vereist: Gegoten nylon onderdelen vereisen mogelijk nabewerking, zoals trimmen, schuren of oppervlakteafwerking, om het gewenste uiterlijk en de maatnauwkeurigheid te bereiken.
4. Materiaalkrimp: Nylonhars kan tijdens het uithardingsproces enige krimp ervaren, waardoor mogelijk aanpassingen aan het matrijsontwerp nodig zijn om dimensionale veranderingen te compenseren.
5. Beperkte materiaalrecycling: het overtollige of afvalmateriaal dat ontstaat tijdens het vacuümgieten van siliconenvormen met nylon is doorgaans niet recycleerbaar voor toekomstig gebruik.
6.Hygroscopische aard: Nylon is hygroscopisch, wat betekent dat het na verloop van tijd vocht uit de omgeving kan opnemen. Dit kan de mechanische eigenschappen beïnvloeden als het niet op de juiste manier wordt behandeld en opgeslagen.
POM
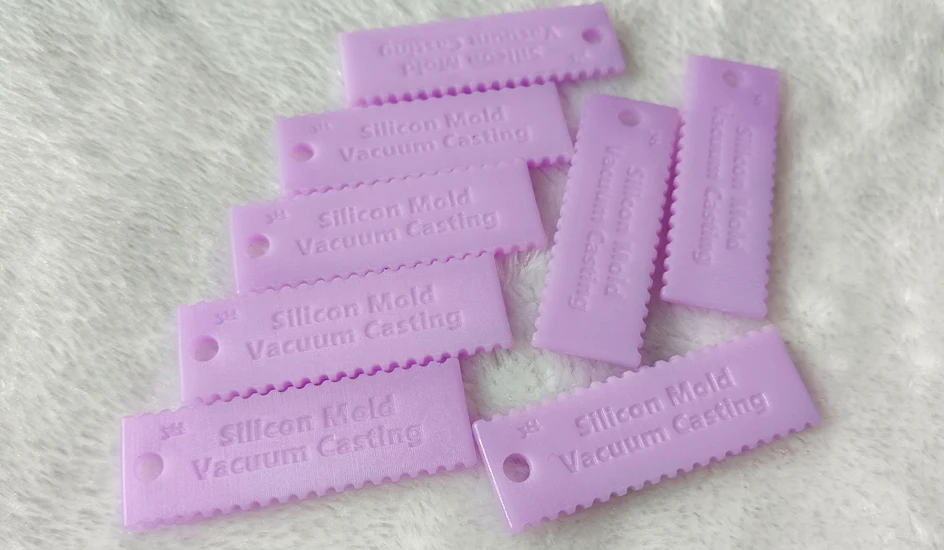
Technologie Siliciumvorm Vacuümgieten
Materiaal POM
Originele kleur Wit/zwart/aangepaste kleur
Thermische vervorming 70-80°C
Hardheid 80D
Oppervlaktesituatie Lichte injectiesporen en krassen
Afdrukplatformgrootte 900*650*450mm
Buigmodulus 2400-2500 Mpa
Buigsterkte 100-110 Mpa
Treksterkte 60-70 MPa
Rek bij breuk 10-12 %
Slagsterkte gekerfd Izod 17 KJ/m²
Tolerantie De lokale nauwkeurigheid van het product ligt tussen 0,3-0,5 mm~5 ‰, terwijl de algehele nauwkeurigheid moeilijk te controleren is
. Ingezette koperen moeren, fysiek polijsten, schilderen, galvaniseren, zeefdruk, watertransferprinten, coating
Wanddikte vereist 0,8 mm hierboven, grote onderdelen volgens 3D-tekeningen.
De voordelen van Silicon Mold Vacuum Casting POM zijn:
1. Uitstekende mechanische eigenschappen: POM vertoont uitstekende mechanische eigenschappen, waaronder hoge treksterkte, stijfheid en slagvastheid. Het wordt vaak gebruikt in toepassingen die robuuste en duurzame componenten vereisen.
2. Lage wrijving: POM heeft een lage wrijvingscoëfficiënt, waardoor het ideaal is voor onderdelen met glijdende of roterende bewegingen. Het wordt vaak gebruikt in tandwielen, lagers en andere componenten waarbij verminderde wrijving cruciaal is.
3.Dimensionale stabiliteit: POM heeft een uitstekende maatvastheid, wat betekent dat onderdelen gemaakt van dit materiaal hun vorm en grootte behouden, zelfs onder temperatuurschommelingen en mechanische belasting.
4. Chemische weerstand: POM is bestand tegen veel chemicaliën, waaronder oplosmiddelen, oliën en brandstoffen, waardoor het geschikt is voor toepassingen waarbij blootstelling aan verschillende stoffen een probleem is.
5. Lage vochtopname: POM heeft lage vochtabsorptie-eigenschappen, wat voordelig is in toepassingen waar blootstelling aan vocht of vochtigheid de prestaties kan beïnvloeden.
6. Productie met laag volume: vacuümgieten in siliconenvormen is zeer geschikt voor het produceren van kleine tot middelgrote hoeveelheden POM-onderdelen, vooral wanneer traditionele productiemethoden onbetaalbaar zouden zijn voor oplages van kleine volumes.
De nadelen van Silicon Mold Vacuum Casting POM zijn:
1. Doorlooptijd: het productieproces, inclusief het maken, uitharden en gieten van de mal, kan enkele dagen in beslag nemen. Dit is mogelijk niet geschikt voor projecten met extreem krappe tijdlijnen.
2. Vormslijtage: Siliconen mallen hebben een beperkte levensduur en kunnen na verloop van tijd verslijten, vooral bij gebruik met harsen met hoge mechanische eigenschappen zoals POM. Bij grote productieruns kan het regelmatig vervangen van de matrijs nodig zijn.
3. Nabewerking vereist: Gegoten POM-onderdelen kunnen nabewerking vereisen, zoals bijsnijden, schuren of oppervlakteafwerking, om het gewenste uiterlijk en de maatnauwkeurigheid te bereiken.
4. Materiaalkrimp: POM-hars kan tijdens het uithardingsproces enige krimp ervaren, waardoor mogelijk aanpassingen aan het matrijsontwerp nodig zijn om dimensionale veranderingen te compenseren.
5. Beperkte materiaalrecycling: het overtollige of afvalmateriaal dat ontstaat tijdens het vacuümgieten van siliconenvormen met POM is doorgaans niet recycleerbaar voor toekomstig gebruik.
6. Kosten: hoewel dit proces kosteneffectief kan zijn voor de productie van POM-onderdelen in kleine volumes, kan het hogere kosten per eenheid met zich meebrengen in vergelijking met traditionele productiemethoden zoals spuitgieten voor grotere productieruns.
Samenvattend biedt vacuümgieten in siliconenvormen met POM de voordelen van uitstekende mechanische eigenschappen, lage wrijving en chemische bestendigheid. Het brengt echter beperkingen met zich mee, zoals doorlooptijd, matrijsslijtage en de noodzaak van nabewerking. Een zorgvuldige afweging van projectvereisten en materialen is essentieel bij het kiezen van deze methode voor 3D-printprojecten met POM.
Silicium


Technologie Siliconen mal Vacuümgieten
Materiaal Silicium
Originele kleur Wit/zwart/aangepaste kleur
Thermische vervorming 50-70°C
Oppervlaktesituatie Lichte injectiesporen en krassen
Afdrukplatformgrootte 900*650*450mm
Tolerantie De lokale nauwkeurigheid van het product ligt tussen 0,3-0,5 mm ~5 ‰, terwijl de algehele nauwkeurigheid moeilijk te controleren is
Hardheid: Shore 30A, 40A, 50A, 60A, 70A, 80A, 90A
Wanddikte vereist 0,8 mm hoger, grote onderdelen volgens 3D-tekeningen
De voordelen van silicium zijn:
1.Elastomere eigenschappen : Siliconenrubber vertoont uitstekende elastomere eigenschappen, waaronder flexibiliteit en veerkracht. Het is ideaal voor het produceren van onderdelen die zacht en buigzaam moeten zijn en na vervorming naar hun oorspronkelijke vorm moeten kunnen terugkeren.
2. Chemische weerstand: Silicone is bestand tegen veel chemicaliën, oliën en oplosmiddelen, waardoor het geschikt is voor toepassingen waarbij blootstelling aan verschillende stoffen een probleem is.
3. Productie met laag volume: vacuümgieten in siliconenvormen is zeer geschikt voor het produceren van kleine tot middelgrote hoeveelheden flexibele siliconenonderdelen, vooral wanneer traditionele productiemethoden onbetaalbaar zouden zijn voor kleine oplagen.
4. Aanpassing: siliconenmaterialen kunnen worden gekleurd, gepigmenteerd of gemengd om verschillende kleuren te verkrijgen of aan specifieke esthetische eisen te voldoen.
De nadelen van silicium zijn:
1. Doorlooptijd: het productieproces, inclusief het maken, uitharden en gieten van mallen, kan enkele dagen in beslag nemen. Dit is mogelijk niet geschikt voor projecten met extreem krappe tijdlijnen.
2. Schimmelslijtage: Siliconen mallen hebben een beperkte levensduur en kunnen na verloop van tijd verslijten, vooral wanneer ze worden gebruikt met harsen die speciale additieven of versterkingen hebben. Bij grote productieruns kan het regelmatig vervangen van de matrijs nodig zijn.
3. Nabewerking vereist: Gegoten siliconenonderdelen kunnen nabewerking vereisen, zoals bijsnijden, schuren of oppervlakteafwerking, om het gewenste uiterlijk en de maatnauwkeurigheid te bereiken.
4. Materiaalkrimp: Siliconenhars kan tijdens het uithardingsproces enige krimp ervaren, waardoor mogelijk aanpassingen aan het matrijsontwerp nodig zijn om dimensionale veranderingen te compenseren.
5. Kosten: hoewel dit proces kosteneffectief kan zijn voor de productie van flexibele siliconenonderdelen in kleine volumes, kan het hogere kosten per eenheid met zich meebrengen in vergelijking met traditionele productiemethoden zoals spuitgieten voor grotere productieruns.